జూన్ 10, 2020 తేదీన, రష్యాలోని టాక్సిమోలో ఒక గోల్డ్ మైన్ ప్లాంట్ కోసం H&G SAG మిల్ లైనర్ను డెలివరీ చేసింది, ఇది MZS5518 గ్రైండింగ్ మిల్లు కోసం, దీనిని చైనాలోని షెన్యాంగ్లోని నార్తర్న్ హెవీ ఇండస్ట్రీస్ గ్రూప్ కో., లిమిటెడ్(NHI) ఉత్పత్తి చేసింది.
SAG అనేది సెమీ-ఆటోజెనస్ గ్రైండింగ్ మిల్ యొక్క సంక్షిప్త రూపం. ఈ రకమైన మిల్లు పెద్ద శకలాలను చిన్న ముక్కలుగా గ్రౌండింగ్ చేయడానికి ఉపయోగిస్తారు. తదుపరి ప్రాసెసింగ్ కోసం ముక్కలు ఉపయోగించబడతాయి. SAG మిల్లులు సాధారణంగా గ్రౌండింగ్ ప్రక్రియలో ఏ రకమైన మెటీరియల్ను ప్రీ-ప్రాసెసింగ్లో ఉపయోగిస్తారు. SAG మిల్లులను మొదటి దశ గ్రైండర్లు అని కూడా అంటారు. ఈ భారీ అవుట్పుట్ SAG మిల్లులు సాధారణంగా విద్యుత్తుతో శక్తిని పొందుతాయి. గ్రౌండింగ్ రంగంలో అవసరాలు మరియు అవసరాలు మెరుగుపరచబడతాయి. మెరుగైన SAG మిల్లులు ట్రెండ్లో వచ్చాయి, ఇది అధిక రేటింగ్ ఉన్న ఉత్పత్తిని ఇస్తుంది. ఈ మిల్లులు గ్రౌండింగ్లో ఎక్కువగా ఉపయోగించే మరియు అవసరమైన పరికరాలలో ఒకటి.
SAG మిల్లు గ్రౌండింగ్ కోసం కొన్ని పెద్ద మరియు గట్టి రాళ్లతో కూడిన ఉక్కు బంతులను ఉపయోగిస్తుంది. ఈ మిల్లులు ముక్కలుగా విరిగిన పదార్థాల పెద్ద శకలాలు తయారు చేయడంలో బంతులను ఉపయోగించుకుంటాయి. SAG మిల్లు యొక్క బాల్ ఛార్జ్ సుమారు 9% నుండి 20% వరకు ఉంటుంది. ఈ ప్రక్రియ SAG మిల్లు యొక్క పెద్ద తిరిగే డ్రమ్ లోపల జరుగుతుంది, ఇది పాక్షికంగా బంతులతో నిండి ఉంటుంది. డ్రమ్ లోపలి భాగం ట్రైనింగ్ ప్లేట్లను ఉపయోగిస్తుంది. డ్రమ్ లోపల ఉన్న ఈ ప్లేట్లు భ్రమణాల సమయంలో మళ్లీ కిందకు పడిపోయేలా గ్రౌండింగ్ మెటీరియల్ని తీయడానికి బాధ్యత వహిస్తాయి. ఉక్కు బంతులు మరియు ముడి పదార్ధాల (ధాతువు) మధ్య పదేపదే ఘర్షణలు, పదార్థాన్ని సూక్ష్మ మరియు చిన్న ముక్కలుగా విభజిస్తాయి. ఈ మొత్తం ప్రక్రియ SAG మిల్లు యొక్క పెద్ద డ్రమ్ లోపల జరుగుతుంది.
అప్లికేషన్:
SAG మిల్లులు పారిశ్రామిక మైనింగ్ యొక్క చాలా ముఖ్యమైన పరికరాలు. SAG మిల్లులను సాధారణంగా మైనింగ్ క్షేత్రాలలో ఉపయోగిస్తారు. తవ్విన బొగ్గు నుండి, ఇది కొన్ని విలువైన లోహాలను వేరు చేస్తుంది. మైనింగ్లో, బంగారం, వెండి, నికెల్ మరియు రాగి వంటి కొన్ని విలువైన లోహాలు కనుగొనబడ్డాయి.
ఆటోజెనస్ మిల్లు అనేది అణిచివేత మరియు గ్రౌండింగ్ ఫంక్షన్లతో కూడిన కొత్త రకం గ్రౌండింగ్ పరికరాలు. ఇది పరస్పర ప్రభావం మరియు గ్రైండింగ్ ప్రభావం ద్వారా కమ్యునిషన్ సాధించడానికి గ్రైండింగ్ మెటీరియల్ను మాధ్యమంగా ఉపయోగిస్తుంది. సెమీ ఆటోజెనస్ మిల్లు ఆటోజెనస్ మిల్లులో తక్కువ సంఖ్యలో ఉక్కు బంతులను జోడించడం, దాని ప్రాసెసింగ్ సామర్థ్యాన్ని 10% - 30% పెంచవచ్చు, యూనిట్ ఉత్పత్తికి శక్తి వినియోగం 10% - 20% వరకు తగ్గించవచ్చు, కానీ లైనర్ వేర్ సాపేక్షంగా 15% పెరిగింది మరియు ఉత్పత్తి చక్కదనం ముతకగా ఉంటుంది. సెమీ-ఆటోజెనస్ మిల్లులో కీలకమైన భాగంగా, SAG మిల్లు యొక్క ఆపరేషన్ సమయంలో మరొక చివర లైనర్పై లైనర్ లిఫ్టింగ్ బీమ్ ఎత్తిన స్టీల్ బాల్ ప్రభావం కారణంగా సిలిండర్ బాడీ యొక్క షెల్ లైనర్లు తీవ్రంగా దెబ్బతిన్నాయి.
2009లో, 7.53 × 4.27 వ్యాసం కలిగిన రెండు కొత్త సెమీ-ఆటోజెనస్ మిల్లులు పంజిహువా ఐరన్ అండ్ స్టీల్ కో., లిమిటెడ్లో నిర్మించబడ్డాయి, వార్షిక డిజైన్ సామర్థ్యం 2 మిలియన్ టన్నులు/సెట్తో. 2011లో, 9.15 × 5.03 వ్యాసం కలిగిన ఒక కొత్త సెమీ-ఆటోజెనస్ మిల్లు 5 మిలియన్ టన్నుల వార్షిక డిజైన్ సామర్థ్యంతో Panzhihua Iron and Steel Co. Ltd. యొక్క బైమా కేంద్రీకరణలో నిర్మించబడింది. 9.15 × 5.03 వ్యాసం కలిగిన సెమీ-ఆటోజెనస్ మిల్లు యొక్క ట్రయల్ ఆపరేషన్ నుండి, మిల్లు యొక్క షెల్ లైనర్లు మరియు గ్రిడ్ ప్లేట్ తరచుగా విరిగిపోతాయి మరియు ఆపరేషన్ రేటు కేవలం 55% మాత్రమే, ఇది ఉత్పత్తి మరియు సామర్థ్యాన్ని తీవ్రంగా ప్రభావితం చేస్తుంది.
పంజిహువా ఐరన్ అండ్ స్టీల్ గ్రూప్కు చెందిన బైమా గనిలోని 9.15 మీటర్ల సెమీ ఆటోజెనస్ మిల్లు అనేక తయారీదారులచే ఉత్పత్తి చేయబడిన సిలిండర్ లైనర్ను ఉపయోగించింది. సుదీర్ఘ సేవా జీవితం 3 నెలల కన్నా తక్కువ, మరియు తక్కువ జీవితం కేవలం ఒక వారం మాత్రమే, ఇది సెమీ-ఆటోజెనస్ మిల్లు యొక్క తక్కువ సామర్థ్యానికి మరియు ఉత్పత్తి ఖర్చు బాగా పెరిగింది. H&G మెషినరీ కో.; Ltd నిరంతర పరిశోధన మరియు పరీక్ష కోసం 9.15 మీటర్ల సెమీ ఆటోజెనస్ మిల్లు ఉన్న ప్రదేశంలోకి లోతుగా వెళ్లింది. కాస్టింగ్ మెటీరియల్, కాస్టింగ్ ప్రక్రియ మరియు హీట్ ట్రీట్మెంట్ ప్రక్రియ యొక్క ఆప్టిమైజేషన్ ద్వారా, బైమా గనిలో ఉత్పత్తి చేయబడిన షెల్ లైనర్ల సేవ జీవితం 4 నెలలు మించిపోయింది మరియు ప్రభావం స్పష్టంగా ఉంటుంది.
Cause analysis of short life of SAG mill shell liners
బైమా కాన్సంట్రేటర్లో φ 9.15 × 5.03 సెమీ-ఆటోజెనస్ మిల్లు యొక్క పారామితులు మరియు నిర్మాణం. టేబుల్ 1 అనేది పారామితి పట్టిక:
అంశం | సమాచారం | అంశం | సమాచారం | అంశం | సమాచారం |
సిలిండర్ వ్యాసం (మిమీ) | 9150 | ఎఫెక్టివ్ వాల్యూమ్ (M3) | 322 | మెటీరియల్ పరిమాణం | ≤300 |
సిలిండర్ పొడవు (మిమీ) | 5030 | స్టీల్ బాల్ యొక్క వ్యాసం (మిమీ) | <150 | డిజైన్ సామర్థ్యం | సంవత్సరానికి 5 మిలియన్ టన్నులు |
మోటారు శక్తి (KW) | 2*4200 | బాల్ ఫిల్లింగ్ రేటు | 8% - 12% | నిర్వహణ పదార్థాలు | V-Ti మాగ్నెటైట్ |
వేగం (R / min) | 10.6 | మెటీరియల్ నింపే రేటు | 45% -55% | మిల్ లైనర్స్ మెటీరియల్ | మిశ్రమం ఉక్కు |
పాత SAG మిల్లు షెల్ లైనర్ల వైఫల్య విశ్లేషణ
బైమా కాన్సంట్రేటర్లో φ 9.15 × 5.03 సెమీ-ఆటోజెనస్ మిల్లును ప్రారంభించినప్పటి నుండి, మిల్లు లైనర్లను సక్రమంగా దెబ్బతీయడం మరియు భర్తీ చేయడం వల్ల ఆపరేషన్ రేటు కేవలం 55% మాత్రమే, ఇది ఆర్థిక ప్రయోజనాలను తీవ్రంగా ప్రభావితం చేస్తుంది. షెల్ లైనర్ యొక్క ప్రధాన వైఫల్య మోడ్ అంజీర్ 1 (a)లో చూపబడింది. ఆన్-సైట్ పరిశోధన ప్రకారం, SAG మిల్లు షెల్ లైనర్లు మరియు లాటిస్ ప్లేట్ ప్రధాన వైఫల్య భాగాలు, ఇవి అంజీర్ 2 (బి)లోని పరిస్థితికి అనుగుణంగా ఉంటాయి. మేము ఇతర కారకాలను మినహాయించాము, లైనర్ విశ్లేషణ నుండి మాత్రమే, ప్రధాన సమస్యలు క్రింది విధంగా ఉన్నాయి:
1. సరికాని పదార్థ ఎంపిక కారణంగా, సిలిండర్ యొక్క లైనర్ ప్లేట్ ఉపయోగ ప్రక్రియలో వైకల్యం చెందుతుంది, దీని ఫలితంగా లైనర్ ప్లేట్ పరస్పరం వెలికితీస్తుంది, దీని ఫలితంగా పగుళ్లు మరియు స్క్రాప్ ఏర్పడతాయి;
2. సిలిండర్ లైనర్ యొక్క కీలక భాగం, దుస్తులు నిరోధకత లేకపోవడం వల్ల, లైనర్ మందం సుమారు 30 మిమీ ఉన్నప్పుడు, కాస్టింగ్ యొక్క మొత్తం బలం తగ్గుతుంది, మరియు స్టీల్ బాల్ ప్రభావాన్ని నిరోధించలేము, ఫలితంగా పగులు మరియు స్క్రాపింగ్;
3. కరిగిన ఉక్కు, అధిక గ్యాస్ కంటెంట్ మరియు నాన్-కాంపాక్ట్ స్ట్రక్చర్ వంటి మలినాలను కాస్టింగ్ నాణ్యత లోపాలు, కాస్టింగ్ యొక్క బలం మరియు మొండితనాన్ని తగ్గిస్తాయి.
SAG మిల్ షెల్ లైనర్ల కొత్త మెటీరియల్ డిజైన్
రసాయన కూర్పు ఎంపిక సూత్రం షెల్ లైనర్ మరియు గ్రిడ్ ప్లేట్ యొక్క యాంత్రిక లక్షణాలను క్రింది అవసరాలను తీర్చడం:
1) అధిక దుస్తులు నిరోధకత. షెల్ లైనర్ మరియు గ్రిడ్ ప్లేట్ యొక్క దుస్తులు షెల్ లైనర్ యొక్క సేవా జీవితాన్ని తగ్గించడానికి దారితీసే ప్రధాన అంశం, మరియు దుస్తులు నిరోధకత షెల్ లైనర్ మరియు గ్రిడ్ ప్లేట్ యొక్క సేవా జీవితాన్ని సూచిస్తుంది.
2) అధిక ప్రభావం దృఢత్వం. ప్రభావం దృఢత్వం అనేది నిర్దిష్ట బాహ్య శక్తిని తక్షణమే భరించిన తర్వాత అసలు స్థితిని పునరుద్ధరించగల లక్షణం. తద్వారా స్టీల్ బాల్ తాకిన సమయంలో షెల్ లైనర్ మరియు గ్రిడ్ ప్లేట్ పగుళ్లు రావు.
రసాయన కూర్పు
1) కార్బన్ మరియు C యొక్క కంటెంట్ వివిధ దుస్తులు పరిస్థితులలో 0.4% మరియు 0.6% మధ్య నియంత్రించబడుతుంది, ముఖ్యంగా ప్రభావం లోడ్;
2) Si మరియు Si యొక్క కంటెంట్ ఫెర్రైట్ను బలపరుస్తుందని, దిగుబడి నిష్పత్తిని పెంచుతుందని, మొండితనాన్ని మరియు ప్లాస్టిసిటీని తగ్గిస్తుంది మరియు పెళుసుదనాన్ని పెంచే ధోరణిని కలిగి ఉంటుందని ఫలితాలు చూపిస్తున్నాయి మరియు కంటెంట్ 0.2-0.45% మధ్య నియంత్రించబడుతుంది;
3) Mn కంటెంట్, Mn మూలకం ప్రధానంగా పరిష్కారం బలపరిచే పాత్రను పోషిస్తుంది, బలం, కాఠిన్యం మరియు దుస్తులు నిరోధకతను మెరుగుపరుస్తుంది, నిగ్రహాన్ని పెళుసుగా మరియు ముతకగా మార్చే నిర్మాణాన్ని పెంచుతుంది మరియు కంటెంట్ 0.8-2.0% మధ్య నియంత్రించబడుతుంది;
4) Chromium కంటెంట్, Cr మూలకం, దుస్తులు-నిరోధక ఉక్కు యొక్క ముఖ్యమైన అంశం, ఉక్కుపై గొప్ప బలపరిచే ప్రభావాన్ని కలిగి ఉంటుంది మరియు ఉక్కు యొక్క బలం, కాఠిన్యం మరియు దుస్తులు నిరోధకతను మెరుగుపరుస్తుంది మరియు కంటెంట్ 1.4-3.0% మధ్య నియంత్రించబడుతుంది;
5) మో కంటెంట్, మో ఎలిమెంట్ అనేది వేర్-రెసిస్టెంట్ స్టీల్, ఫెర్రైట్ను బలోపేతం చేయడం, ధాన్యాన్ని శుద్ధి చేయడం, టెంపర్ పెళుసుదనాన్ని తగ్గించడం లేదా తొలగించడం, ఉక్కు యొక్క బలం మరియు కాఠిన్యాన్ని మెరుగుపరచడం, కంటెంట్ 0.4-1.0% మధ్య నియంత్రించబడుతుంది;
6) Ni యొక్క కంటెంట్ 0.9-2.0% లోపల నియంత్రించబడుతుంది,
7) వెనాడియం యొక్క కంటెంట్ తక్కువగా ఉన్నప్పుడు, ధాన్యం పరిమాణం శుద్ధి చేయబడుతుంది మరియు దృఢత్వం మెరుగుపడుతుంది. వనాడియం యొక్క కంటెంట్ 0.03-0.08% లోపల నియంత్రించబడుతుంది;
8) ఫలితాలు టైటానియం యొక్క డీఆక్సిడేషన్ మరియు ధాన్యం శుద్ధీకరణ ప్రభావం స్పష్టంగా ఉన్నాయని మరియు కంటెంట్ 0.03% మరియు 0.08% మధ్య నియంత్రించబడుతుంది;
9) రీ కరిగిన ఉక్కును శుద్ధి చేయగలదు, సూక్ష్మ నిర్మాణాన్ని మెరుగుపరుస్తుంది, గ్యాస్ కంటెంట్ను తగ్గిస్తుంది మరియు ఉక్కులోని ఇతర హానికరమైన మూలకాలను తగ్గిస్తుంది. అధిక ఉక్కు యొక్క బలం, ప్లాస్టిసిటీ మరియు అలసట నిరోధకతను 0.04-0.08% లోపల నియంత్రించవచ్చు;
10) P మరియు s యొక్క కంటెంట్ 0.03% కంటే తక్కువగా నియంత్రించబడాలి.
కాబట్టి కొత్త డిజైన్ SAG మిల్ షెల్ లైనర్ల రసాయన కూర్పు:
The Chemical Composition Of New Design SAG Mill Shell Liners | |||||||||||
మూలకం | సి | సి | Mn | పి | ఎస్ | Cr | ని | మో | వి | టి | రె |
విషయము (%) | 0.4-0.6 | 0.2-0.45 | 0.8-2.0 | ≤0. 03 | ≤0. 03 | 1.4-3.0 | 0.9-2.0 | 0.4-1.0 | జాడ కనుగొను | జాడ కనుగొను | జాడ కనుగొను |
కాస్టింగ్ టెక్నాలజీ
కాస్టింగ్ టెక్నాలజీ యొక్క ముఖ్య అంశాలు
- కార్బన్ డయాక్సైడ్ సోడియం సిలికేట్ స్వీయ గట్టిపడే ఇసుకను అచ్చు ఇసుక యొక్క తేమను ఖచ్చితంగా నియంత్రించడానికి ఉపయోగిస్తారు;
- ఆల్కహాల్ ఆధారిత స్వచ్ఛమైన జిర్కాన్ పౌడర్ పూత ఉపయోగించబడుతుంది మరియు గడువు ముగిసిన ఉత్పత్తులను ఉపయోగించకూడదు;
- మొత్తం ఘన నమూనాను తయారు చేయడానికి నురుగును ఉపయోగించి, ప్రతి కాస్టింగ్ ఫిల్లెట్ తప్పనిసరిగా శరీరంపైకి తీసుకురావాలి, ఖచ్చితమైన పరిమాణం మరియు సహేతుకమైన నిర్మాణం అవసరం;
- అచ్చు ప్రక్రియలో, వైకల్యం ఖచ్చితంగా నియంత్రించబడాలి మరియు ఆపరేటర్ ఇసుకను సమానంగా వేయాలి మరియు ఇసుక అచ్చు తగినంతగా మరియు సమానంగా ఉండాలి మరియు అదే సమయంలో, నిజమైన నమూనా యొక్క వైకల్పనాన్ని నివారించాలి;
- అచ్చు సవరణ ప్రక్రియలో, ఇసుక అచ్చు యొక్క డైమెన్షనల్ ఖచ్చితత్వాన్ని నిర్ధారించడానికి పరిమాణాన్ని ఖచ్చితంగా తనిఖీ చేయాలి;
- పెట్టెను మూసివేయడానికి ముందు ఇసుక అచ్చును ఎండబెట్టాలి;
- అసమాన గోడ మందాన్ని నివారించడానికి ప్రతి కోర్ యొక్క పరిమాణాన్ని తనిఖీ చేయండి.
కాస్టింగ్ ప్రక్రియ
పోయడం ఉష్ణోగ్రత అనేది తారాగణం యొక్క అంతర్గత నిర్మాణాన్ని ప్రభావితం చేసే ప్రధాన అంశం. పోయడం ఉష్ణోగ్రత చాలా ఎక్కువగా ఉంటే, కరిగిన ఉక్కు యొక్క వేడెక్కిన వేడి పెద్దది, కాస్టింగ్ సంకోచం సారంధ్రత మరియు ముతక నిర్మాణాన్ని ఉత్పత్తి చేయడం సులభం; పోయడం ఉష్ణోగ్రత చాలా తక్కువగా ఉంటే, ద్రవ ఉక్కు యొక్క వేడెక్కిన వేడి తక్కువగా ఉంటుంది మరియు పోయడం సరిపోదు. పోయడం ఉష్ణోగ్రత 1510 ℃ మరియు 1520 ℃ మధ్య నియంత్రించబడుతుంది, ఇది మంచి సూక్ష్మ నిర్మాణాన్ని మరియు పూర్తి పూరకాన్ని నిర్ధారిస్తుంది. సరైన పోయడం వేగం కాంపాక్ట్ నిర్మాణానికి కీలకం మరియు రైసర్లో సంకోచం కుహరం లేదు. పోయడం వేగం శీతలీకరణ నీటి పైపు యొక్క స్థానానికి దగ్గరగా ఉన్నప్పుడు, "మొదట నెమ్మదిగా, తరువాత వేగంగా, ఆపై నెమ్మదిగా" అనే సూత్రాన్ని అనుసరించాలి. అంటే నెమ్మదిగా పోయడం ప్రారంభించాలి. కరిగిన ఉక్కు కాస్టింగ్ బాడీలోకి ప్రవేశించినప్పుడు, కరిగిన ఉక్కును రైసర్కు వేగంగా పైకి లేపడానికి పోయడం వేగం పెరుగుతుంది, ఆపై పోయడం నెమ్మదిగా ఉంటుంది. కరిగిన ఉక్కు రైసర్ ఎత్తులో 2/3లోకి ప్రవేశించినప్పుడు, పోయడం ముగిసే వరకు రైసర్ను పోయడానికి ఉపయోగిస్తారు.
వేడి చికిత్స
మీడియం మరియు తక్కువ కార్బన్ స్ట్రక్చరల్ స్టీల్స్ యొక్క సరైన మిశ్రమం పెర్లైట్ పరివర్తనను గణనీయంగా ఆలస్యం చేస్తుంది మరియు బైనైట్ పరివర్తనను హైలైట్ చేస్తుంది, తద్వారా బైనైట్ ఆధిపత్య నిర్మాణాన్ని ఆస్టెనిటైజింగ్ తర్వాత నిరంతర శీతలీకరణ రేటు యొక్క పెద్ద శ్రేణిలో పొందవచ్చు, దీనిని బైనిటిక్ స్టీల్ అంటారు. బైనిటిక్ స్టీల్ తక్కువ శీతలీకరణ రేటుతో అధిక సమగ్ర లక్షణాలను పొందగలదు, తద్వారా వేడి చికిత్స ప్రక్రియను సులభతరం చేస్తుంది మరియు వైకల్యాన్ని తగ్గిస్తుంది.
ఐసోథర్మల్ చికిత్స
ఐసోథర్మల్ ట్రీట్మెంట్ ద్వారా బైనైట్ ఉక్కు పదార్థాలను పొందడం ఇనుము మరియు ఉక్కు మెటలర్జీ రంగంలో గొప్ప విజయం, ఇది సూపర్ స్టీల్ మరియు నానో స్టీల్ పదార్థాలను అభివృద్ధి చేసే దిశలలో ఒకటి. ఏది ఏమైనప్పటికీ, ఆస్టంపరింగ్ ప్రక్రియ మరియు పరికరాలు సంక్లిష్టంగా ఉంటాయి, శక్తి వినియోగం పెద్దది, ఉత్పత్తి ధర ఎక్కువగా ఉంటుంది, మధ్యస్థ కాలుష్య వాతావరణాన్ని అణచివేయడం, సుదీర్ఘ ఉత్పత్తి చక్రం మరియు మొదలైనవి
గాలి శీతలీకరణ చికిత్స
ఐసోథర్మల్ ట్రీట్మెంట్లోని లోపాలను అధిగమించడానికి, కాస్టింగ్ తర్వాత గాలి శీతలీకరణ ద్వారా ఒక రకమైన బైనిటిక్ స్టీల్ తయారు చేయబడింది. అయినప్పటికీ, మరింత బైనైట్ పొందాలంటే, రాగి, మాలిబ్డినం, నికెల్ మరియు ఇతర విలువైన మిశ్రమాలను జోడించాలి, ఇది అధిక ధరను కలిగి ఉండటమే కాకుండా పేలవమైన మొండితనాన్ని కూడా కలిగి ఉంటుంది.
నియంత్రిత శీతలీకరణ చికిత్స
నియంత్రిత శీతలీకరణ అనేది స్టీల్ కంట్రోల్డ్ రోలింగ్ ప్రక్రియలో ఒక భావన. ఇటీవలి సంవత్సరాలలో, ఇది సమర్థవంతమైన మరియు శక్తిని ఆదా చేసే వేడి చికిత్స పద్ధతిగా అభివృద్ధి చేయబడింది. హీట్ ట్రీట్మెంట్ సమయంలో, డిజైన్ చేయబడిన మైక్రోస్ట్రక్చర్ను పొందవచ్చు మరియు నియంత్రిత శీతలీకరణ ద్వారా ఉక్కు యొక్క లక్షణాలను మెరుగుపరచవచ్చు. ఉక్కు యొక్క నియంత్రిత రోలింగ్ మరియు శీతలీకరణపై పరిశోధనలో నియంత్రిత శీతలీకరణ ఉక్కు యొక్క రసాయన కూర్పు అనుకూలంగా ఉన్నప్పుడు బలమైన మరియు కఠినమైన తక్కువ కార్బన్ బైనైట్ ఏర్పడటానికి ప్రోత్సహిస్తుంది. నియంత్రిత శీతలీకరణ యొక్క సాధారణంగా ఉపయోగించే పద్ధతులలో ప్రెజర్ జెట్ కూలింగ్, లామినార్ కూలింగ్, వాటర్ కర్టెన్ కూలింగ్, అటామైజేషన్ కూలింగ్, స్ప్రే కూలింగ్, ప్లేట్ టర్బులెంట్ కూలింగ్, వాటర్-ఎయిర్ స్ప్రే కూలింగ్ మరియు డైరెక్ట్ క్వెన్చింగ్ మొదలైనవి ఉన్నాయి. 8 రకాల కంట్రోల్ కూలింగ్ పద్ధతులు సాధారణంగా ఉపయోగించబడతాయి. .
వేడి చికిత్స ప్రాసెసింగ్ పద్ధతి
కంపెనీ పరికరాల స్థితి మరియు వాస్తవ పరిస్థితుల ప్రకారం, మేము నిరంతర శీతలీకరణ వేడి చికిత్స పద్ధతిని అనుసరిస్తాము. నిర్దిష్ట హీటింగ్ రేటు ప్రకారం AC3 + (50~100) సెంటీగ్రేడ్ ద్వారా తాపన ఉష్ణోగ్రతను పెంచడం మరియు మా కంపెనీ అభివృద్ధి చేసిన వాటర్-ఎయిర్ స్ప్రే కూలింగ్ పరికరాన్ని ఉపయోగించడం ద్వారా శీతలీకరణను వేగవంతం చేయడం నిర్దిష్ట ప్రక్రియ, తద్వారా పదార్థం గాలితో చల్లబడుతుంది మరియు స్వీయ గట్టిపడిన. ఇది పూర్తి మరియు సజాతీయ బైనైట్ నిర్మాణాన్ని పొందవచ్చు, అద్భుతమైన పనితీరును సాధించగలదు, అదే ఉత్పత్తుల కంటే స్పష్టంగా ఉన్నతమైనది మరియు రెండవ రకాల నిగ్రహాన్ని తొలగించగలదు.
ఫలితాలు
- మెటాలోగ్రాఫిక్ నిర్మాణం: 6.5 గ్రేడ్ ధాన్యం పరిమాణం
- HRC 45-50
- మా కంపెనీ ఉత్పత్తి చేసిన పెద్ద సెమీ-ఆటోజెనస్ మిల్లు యొక్క షెల్ లైనర్ దాదాపు 3.5 సంవత్సరాలుగా Φ 9.15 మీటర్ల సెమీ ఆటోజెనస్ మిల్లులో పంజిహువా ఐరన్ అండ్ స్టీల్ గ్రూప్ కో., లిమిటెడ్ యొక్క బైమా గనిలో ఉపయోగించబడింది. సేవా జీవితం కంటే ఎక్కువ. 4 నెలలు, మరియు సుదీర్ఘ సేవా జీవితం 7 నెలలు. సేవ జీవితం యొక్క పెరుగుదలతో, యూనిట్ గ్రౌండింగ్ ఖర్చు బాగా తగ్గింది, లైనింగ్ ప్లేట్ స్థానంలో ఫ్రీక్వెన్సీ బాగా తగ్గింది, ఉత్పత్తి సామర్థ్యం గణనీయంగా మెరుగుపడింది మరియు ప్రయోజనం స్పష్టంగా ఉంటుంది.
- పెద్ద సెమీ-ఆటోజెనస్ మిల్లు యొక్క మిల్లు లైనర్ల సేవా జీవితాన్ని మెరుగుపరచడానికి మెటీరియల్ ఎంపిక కీలకం, మరియు దుస్తులు నిరోధకతను మెరుగుపరచడానికి ఉక్కు గ్రేడ్ల మిశ్రమం ప్రభావవంతమైన మార్గం.
- అధిక బలం మరియు అధిక మొండితనం కలిగిన బైనైట్ నిర్మాణం సెమీ-ఆటోజెనస్ మిల్లు యొక్క షెల్ లైనర్ యొక్క సేవ జీవితాన్ని మెరుగుపరిచే హామీ.
- కాస్టింగ్ ప్రక్రియ మరియు హీట్ ట్రీట్మెంట్ ప్రాసెస్ అనేది కాస్టింగ్ నిర్మాణం దట్టంగా ఉందని నిర్ధారించడానికి ఖచ్చితంగా సరిపోతాయి, ఇది సెమీ-ఆటోజెనస్ మిల్ షెల్ లైనర్ యొక్క సేవ జీవితాన్ని ప్రభావవంతంగా మెరుగుపరుస్తుంది.
Nick Sun [email protected]
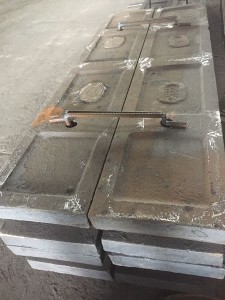
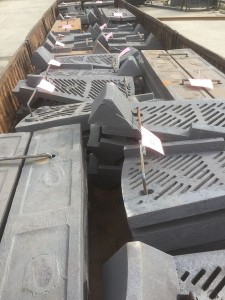
పోస్ట్ సమయం: జూన్-12-2020