Con data do 10 de abril de 2020, H&G entregou a Armenia un forro de molinos de bolas FLSmidth cun diámetro de 20' x 31' e para o molino de automoción, o diámetro é de 34' x 15' a Armenia. Os forros están no estándar de material AS2074 L2C, HB325 -375. Cr-Mo Alloyed SAG Mill revestimento, revestimentos AG Mill para ouro, cobre, planta de mina Molybendum.
FLSmidth & Co. A/S é unha empresa de enxeñería danesa con sede en Copenhague, Dinamarca. Con case 11.700 empregados en todo o mundo, ofrece fábricas, maquinaria, servizos e know-how ás industrias de cemento e minerais mundiais. FLSmidth cotiza no NASDAQ OMX Nordic Copenhagen (a antiga Bolsa de Valores de Copenhague) no índice C20 e ten oficinas en máis de 50 países en todo o mundo.
En liña co seu maior enfoque en áreas de negocios principais como o cemento e os minerais, FLSmidth cedeu as vendas de capital de fornos de cal e equipos de recaustificación para o seu uso en plantas de licor branco na industria de pasta e papel. O negocio foi cedido a Metso Paper Sweden AB [25] mediante un acordo de licenza. A licenza era perpetua e exclusiva en relación con FLSmidth.
Armenia é un importante produtor de molibdeno, que se usa nalgunhas formas de aceiro de alta calidade e outras aliaxes. O complexo de cobre-molibdeno Zangezur posúe grandes reservas de molibdeno que se concentran no depósito de Kajaran. Ademais do molibdeno, Armenia ten importantes xacementos de cobre e ouro; depósitos máis pequenos de chumbo, prata e cinc; e depósitos de minerais industriais, incluíndo basalto, diatomita, granito, xeso, pedra caliza e perlita.
Segundo a Axencia de Desenvolvemento Armenia, Armenia ten máis de 670 minas de construción e minerais agregados, incluíndo 30 minas de metais básicos e de metais preciosos. Entre estas minas, actualmente están en explotación preto de 400 minas, entre elas 22 de metais comúns, metais non férreos e metais preciosos.
Entre os xacementos de metais básicos e de metais preciosos, hai 7 minas de cobre-molibdeno, 3 minas de cobre, 13 minas de ouro e ouro-polimetálico, 2 minas de polimetálico e 2 minas de mineral de ferro. Ademais das minas rexistradas no inventario estatal de recursos minerais, hai 115 xacementos adicionais de varios xacementos que foron descubertos.
O muíño autóxeno é un novo tipo de equipo de moenda con funcións de trituración e moenda. Usa o propio material de moenda como medio, a través do impacto mutuo e do efecto de moenda para lograr a trituración. O muíño semi-autóxeno é engadir un pequeno número de bolas de aceiro ao molino autóxeno, a súa capacidade de procesamento pode aumentarse nun 10% - 30%, o consumo de enerxía por unidade de produto pódese reducir nun 10% - 20%, pero o O desgaste do revestimento aumenta relativamente nun 15% e a finura do produto é máis grosa. Como parte fundamental do muíño semi-autóxeno, os revestimentos do corpo do cilindro están seriamente danados debido ao impacto da bola de aceiro levantada polo feixe de elevación do revestimento no outro extremo durante o funcionamento do muíño SAG.
En 2009, construíronse dous novos muíños semiautóxenos cun diámetro de 7,53 × 4,27 en Panzhihua Iron and Steel Co., Ltd., cunha capacidade de deseño anual de 2 millóns de toneladas por conxunto. En 2011, construíuse un novo muíño semi-autóxeno cun diámetro de 9,15 × 5,03 na concentradora Baima de Panzhihua Iron and Steel Co., Ltd., cunha capacidade de deseño anual de 5 millóns de toneladas. Desde a operación de proba do muíño semi-autóxeno cun diámetro de 9,15 × 5,03, os revestimentos de casca e a placa de reixa do muíño adoitan romperse e a taxa de operación é só do 55%, o que afecta seriamente a produción e a eficiencia.
O muíño semiautóxeno de 9,15 m da mina Baima de Panzhihua Iron and Steel Group utilizou o revestimento do cilindro producido por moitos fabricantes. A vida útil máis longa é de menos de 3 meses e a vida máis curta é de só unha semana, o que leva á baixa eficiencia do muíño semiautóxeno e ao custo de produción moito maior. H&G Machinery Co.; Ltd afondou no sitio dun muíño semi autóxeno de 9,15 m para unha investigación e proba continuas. A través da optimización do material de fundición, o proceso de fundición e o proceso de tratamento térmico, a vida útil dos revestimentos de casca producidos na mina de Baima superou os 4 meses e o efecto é obvio.
Análise das causas da curta vida útil dos revestimentos de muíños SAG
Os parámetros e a estrutura do muíño semiautóxeno φ 9,15 × 5,03 no concentrador Baima. A táboa 1 é a táboa de parámetros:
Elemento | Datos | Elemento | Datos | Elemento | Datos |
Diámetro do cilindro (mm) | 9150 | Volume efectivo (M3) | 322 | Tamaño do material | ≤300 |
Lonxitude do cilindro (mm) | 5030 | Diámetro da bola de aceiro (mm) | <150 | Capacidade de deseño | 5 millóns de toneladas/ano |
Potencia do motor (KW) | 2*4200 | Taxa de recheo de bólas | 8 % ~ 12 % | Manipulación de materiais | Magnetita V-Ti |
Velocidade (R/min) | 10.6 | Taxa de recheo de material | 45% ~ 55% | Material de forros de molino | Aceiro de aliaxe |
Análise de avarías dos antigos revestimentos de muíños SAG
Desde a posta en funcionamento do muíño semiautóxeno φ 9,15 × 5,03 no concentrador de Baima, a taxa de operación é de só un 55% debido ao dano irregular e á substitución dos revestimentos do muíño, o que afecta gravemente os beneficios económicos. O principal modo de falla do forro de casca móstrase na figura 1 (a). Segundo a investigación in situ, os revestimentos de casca do muíño SAG e a placa de celosía son as principais partes de falla, que son consistentes coa situación da figura 2 (b). Excluímos outros factores, só da propia análise do forro, os principais problemas son os seguintes:
1. Debido á selección inadecuada do material, a placa de revestimento do cilindro defórmase no proceso de uso, o que resulta na extrusión mutua da placa de revestimento, resultando en fractura e chatarra;
2. Como a parte clave do revestimento do cilindro, debido á falta de resistencia ao desgaste, cando o grosor do revestimento é duns 30 mm, a resistencia global da fundición diminúe e o impacto da bola de aceiro non se pode resistir, o que provoca fracturas e desguace;
3. Os defectos de calidade da fundición, como as impurezas no aceiro fundido, o alto contido de gas e a estrutura non compacta, reducen a resistencia e a dureza das fundicións.
Novo deseño de material dos revestimentos de muíños SAG
O principio da selección da composición química é facer que as propiedades mecánicas do forro e da placa de reixa cumpran os seguintes requisitos:
1) Alta resistencia ao desgaste. O desgaste do forro e da placa de reixa é o principal factor que leva á diminución da vida útil do revestimento e a resistencia ao desgaste representa a vida útil do forro e da placa de reixa.
2) Alta tenacidade ao impacto. A dureza ao impacto é unha característica que pode recuperar o estado orixinal despois de soportar certa forza externa ao instante. Para que o forro e a placa da reixa non se rachen durante o impacto da bola de aceiro.
Composición Química
1) O contido de carbono e C está controlado entre o 0,4% e o 0,6% en diferentes condicións de desgaste, especialmente a carga de impacto;
2) Os resultados mostran que o contido de Si e Si fortalece a ferrita, aumenta a relación de rendemento, reduce a dureza e plasticidade e ten a tendencia a aumentar a fraxilidade do tempero e o contido está controlado entre 0,2-0,45%;
3) Contido de Mn, o elemento Mn desempeña principalmente o papel de fortalecemento da solución, mellorando a resistencia, a dureza e a resistencia ao desgaste, aumentando a fraxilidade do tempero e a estrutura engrosada, e o contido está controlado entre 0,8-2,0%;
4) O contido de cromo, o elemento Cr, un elemento importante do aceiro resistente ao desgaste, ten un gran efecto de fortalecemento do aceiro e pode mellorar a resistencia, a dureza e a resistencia ao desgaste do aceiro, e o contido está controlado entre 1,4-3,0%;
5) Contido de Mo, o elemento Mo é un dos principais elementos do aceiro resistente ao desgaste, fortalecendo a ferrita, refinando o gran, reducindo ou eliminando a fraxilidade do tempero, mellorando a resistencia e dureza do aceiro, o contido está controlado entre 0,4-1,0%;
6) O contido de Ni está controlado dentro do 0,9-2,0%,
7) Cando o contido de vanadio é pequeno, refírase o tamaño do gran e mellora a dureza. O contido de vanadio pódese controlar dentro de 0,03-0,08%;
8) Os resultados mostran que o efecto de desoxidación e refinamento do gran do titanio é obvio e o contido está controlado entre o 0,03% e o 0,08%;
9) Re pode purificar o aceiro fundido, refinar a microestrutura, reducir o contido de gas e outros elementos nocivos no aceiro. A resistencia, a plasticidade e a resistencia á fatiga do aceiro alto pódense controlar nun 0,04-0,08%;
10) O contido de P e s debe controlarse por debaixo do 0,03%.
Así, a composición química dos revestimentos de muíños SAG de novo deseño son:
A composición química do novo deseño SAG Mill Shell Liners | |||||||||||
Elemento | C | Si | Mn | P | S | Cr | Ni | Mo | V | Ti | Re |
Contido (%) | 0,4-0,6 | 0,2-0,45 | 0,8-2,0 | ≤0. 03 | ≤0. 03 | 1,4-3,0 | 0,9-2,0 | 0,4-1,0 | rastro | rastro | rastro |
Tecnoloxía de fundición
Puntos clave da tecnoloxía de fundición
- A area autoendurecible de silicato sódico de dióxido de carbono úsase para controlar estrictamente o contido de humidade da area de moldeo;
- Empregarase revestimento en po puro de circón a base de alcohol e non se utilizarán produtos caducados;
- Usando escuma para facer a mostra sólida enteira, cada filete de fundición debe sacarse sobre o corpo, requirindo o tamaño preciso e unha estrutura razoable;
- No proceso de moldaxe, a deformación debe controlarse estritamente e o operador debe poñer area uniformemente e o molde de area debe ser o suficientemente compacto e uniforme e, ao mesmo tempo, debe evitarse a deformación da mostra real;
- No proceso de modificación do molde, o tamaño debe ser controlado rigorosamente para garantir a precisión dimensional do molde de area;
- O molde de area debe secar antes de pechar a caixa;
- Comprobe o tamaño de cada núcleo para evitar un grosor desigual da parede.
Proceso de fundición
A temperatura de vertido é o principal factor que afecta a estrutura interna das pezas de fundición. Se a temperatura de vertido é demasiado alta, a calor superenriquecida do aceiro fundido é grande, a fundición é fácil de producir porosidade de contracción e estrutura grosa; se a temperatura de vertido é demasiado baixa, a calor sobrequente do aceiro líquido é pequena e o vertido non é suficiente. A temperatura de vertido está controlada entre 1510 ℃ e 1520 ℃, o que pode garantir unha boa microestrutura e un recheo completo. A velocidade de vertido adecuada é a clave para a estrutura compacta e sen cavidade de encollemento no riser. Cando a velocidade de vertedura está próxima á posición do tubo de auga de refrixeración, seguirase o principio de "primeiro lento, despois rápido e despois lento". Iso é comezar a verter lentamente. Cando o aceiro fundido entra no corpo de fundición, a velocidade de vertido aumenta para facer que o aceiro fundido suba rapidamente ao riser e, a continuación, o vertido é lento. Cando o aceiro fundido entra en 2/3 da altura do vértice, utilízase para facer o vertido ata o final do vertido.
Tratamento térmico
A aliaxe axeitada de aceiros estruturais de medio e baixo carbono pode atrasar significativamente a transformación da perlita e resaltar a transformación de bainita para que a estrutura dominada por bainita poida obterse nun gran intervalo de velocidade de arrefriamento continuo despois da austenitización, que se denomina aceiro bainítico. O aceiro bainitico pode obter propiedades completas máis altas cunha taxa de arrefriamento máis baixa, simplificando así o proceso de tratamento térmico e reducindo a deformación.
Tratamento isotérmico
É un gran logro no campo da metalurxia do ferro e do aceiro obter materiais de aceiro bainita mediante tratamento isotérmico, que é unha das direccións de desenvolvemento de materiais de aceiro super e nano aceiro. Non obstante, o proceso e os equipos de austempering son complexos, o consumo de enerxía é grande, o custo do produto é alto, o ambiente de contaminación medio sofocante, o ciclo de produción longo, etc.
Tratamento de arrefriamento por aire
Para superar as deficiencias do tratamento isotérmico, preparouse unha especie de aceiro bainítico por arrefriamento por aire despois da fundición. Non obstante, para obter máis bainita hai que engadir cobre, molibdeno, níquel e outras aliaxes preciosas, que non só teñen un alto custo senón que tamén teñen unha escasa tenacidade.
Tratamento de arrefriamento controlado
O arrefriamento controlado foi orixinalmente un concepto no proceso de laminación controlada de aceiro. Nos últimos anos, converteuse nun método de tratamento térmico eficiente e de aforro enerxético. Durante o tratamento térmico pódese obter a microestrutura deseñada e mellorar as propiedades do aceiro mediante o arrefriamento controlado. A investigación sobre laminación e arrefriamento controlado do aceiro mostra que o arrefriamento controlado pode promover a formación de bainita de baixo carbono forte e resistente cando a composición química do aceiro é adecuada. Os métodos de arrefriamento controlado comúnmente utilizados inclúen o arrefriamento por chorro de presión, o arrefriamento laminar, o arrefriamento por cortina de auga, o arrefriamento por atomización, o arrefriamento por pulverización, o arrefriamento turbulento de placas, o arrefriamento por pulverización con auga e o aire e o enfriamento directo, etc. .
Método de tratamento térmico
Segundo o estado dos equipos e as condicións reais da empresa, adoptamos un método de tratamento térmico de refrixeración continua. O proceso específico é aumentar a temperatura de quecemento en AC3 + (50 ~ 100) centígrados segundo unha determinada taxa de quecemento e acelerar o arrefriamento mediante o dispositivo de refrixeración por pulverización de auga e aire desenvolvido pola nosa empresa para que o material se arrefríe por aire e autoendurecido. Pode obter unha estrutura de bainita completa e homoxénea, conseguir un excelente rendemento, obviamente superior aos mesmos produtos, e eliminar os segundos tipos de fraxilidade do tempero.
Os Resultados
- Estrutura metalográfica: grao 6,5. Granulometría
- HRC 45-50
- O revestimento de casca da gran fábrica semi-autóxena producida pola nosa empresa foi utilizada durante case 3,5 anos no muíño semi-autóxeno Φ 9,15 m na mina de Baima de Panzhihua Iron and Steel Group Co., Ltd. a vida útil é máis de 4 meses, e a vida útil máis longa é de 7 meses. Co aumento da vida útil, o custo unitario de moenda redúcese moito, a frecuencia de substitución da placa de revestimento redúcese moito, a eficiencia de produción mellora significativamente e o beneficio é obvio.
- A selección de material é a clave para mellorar a vida útil dos revestimentos de muíños da gran fábrica semi-autóxena, e a aliaxe de calidades de aceiro é unha forma eficaz de mellorar a resistencia ao desgaste.
- A estrutura de bainita con alta resistencia e alta tenacidade é a garantía de mellorar a vida útil do forro de casca do muíño semiautóxeno.
- O proceso de fundición e o proceso de tratamento térmico son perfectos para garantir que a estrutura de fundición sexa densa, o que pode mellorar eficazmente a vida útil do revestimento de casca do muíño semi-autóxeno.
Nick Sun [email protected]
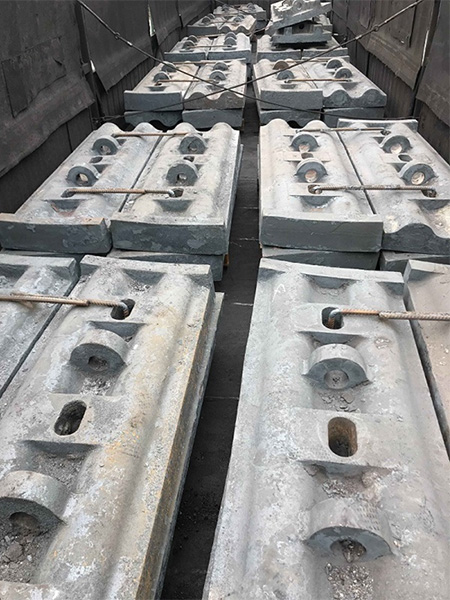
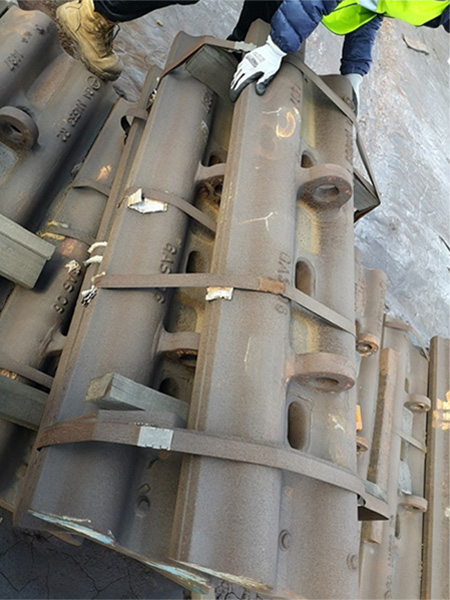
Hora de publicación: 19-maio-2020