Qu'est-ce que l'extraction du cuivre ?
L'extraction du cuivre fait référence aux méthodes utilisées pour obtenir du cuivre à partir de ses minerais. La conversion du cuivre consiste en une série de processus physiques et électrochimiques. Les méthodes ont évolué et varient d'un pays à l'autre en fonction de la source de minerai, des réglementations environnementales locales et d'autres facteurs.
Comme dans toutes les opérations minières, le minerai doit généralement être enrichi (concentré). Les techniques de traitement dépendent de la nature du minerai. Si le minerai est principalement constitué de minéraux sulfurés de cuivre (comme la chalcopyrite), le minerai est concassé et broyé pour libérer les minéraux précieux des déchets (« gangue »). Il est ensuite concentré par flottation minérale. Le concentré est généralement ensuite vendu à des fonderies éloignées, bien que certaines grandes mines aient des fonderies situées à proximité. Une telle colocalisation des mines et des fonderies était plus typique au XIXe et au début du XXe siècle, lorsque les petites fonderies pouvaient être économiques. Les concentrés de sulfure sont généralement fondus dans des fours tels que le four flash Outokumpu ou Inco ou le four ISASMELT pour produire de la matte, qui doit être convertie et raffinée pour produire du cuivre d'anode. Enfin, le processus de raffinage final est l'électrolyse. Pour des raisons économiques et environnementales, de nombreux sous-produits de l'extraction sont valorisés. Le dioxyde de soufre gazeux, par exemple, est capturé et transformé en acide sulfurique, qui peut ensuite être utilisé dans le processus d'extraction ou vendu à des fins telles que la fabrication d'engrais.
Les minerais de cuivre oxydés peuvent être traités par extraction hydrométallurgique.
Histoire

Mineurs de la mine Tamarack à Copper Country, en 1905
La première preuve de martelage à froid du cuivre natif provient des fouilles de Çayönü Tepesi dans l'est de l'Anatolie, qui datent de 7200 à 6600 avant notre ère. [1] Parmi les divers objets considérés comme votifs ou amulettes, il y en avait un qui ressemblait à un hameçon et un à un poinçon. Une autre découverte, à la grotte de Shanidar à Mergasur, en Irak, contenait des perles de cuivre datant de 8 700 avant notre ère. [2]
L'une des plus anciennes mines de cuivre connues au monde, par opposition à l'utilisation de gisements de surface, se trouve dans la vallée de Timna, en Israël, depuis le quatrième millénaire avant JC, avec une utilisation de gisements de surface depuis le sixième au cinquième millénaire. [3] [4]
Le site archéologique de Pločnik, dans le sud-est de l'Europe (Serbie), contient la plus ancienne preuve datée [ douteuse - discuter ] de la fabrication du cuivre à haute température, datant de 5 000 avant notre ère. La découverte de juin 2010 prolonge de 500 ans supplémentaires le record antérieur de fusion de cuivre de Rudna Glava (Serbie), daté du 5e millénaire avant notre ère. [5]
La technologie de fusion du cuivre a donné naissance à l'âge du cuivre, alias l'âge chalcolithique, puis à l'âge du bronze. L'âge du bronze n'aurait pas été possible sans que les humains aient développé la technologie de la fonte.
Concentration
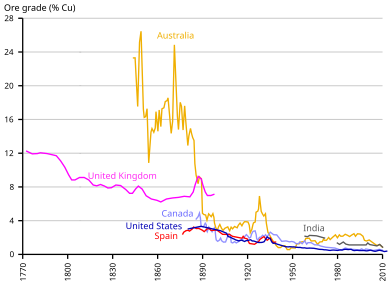
La concentration décroissante de cuivre dans les minerais nécessite désormais un prétraitement des minerais.
La plupart des minerais de cuivre ne contiennent qu'un petit pourcentage de cuivre métallique lié à des minerais précieux, le reste du minerai étant de la roche ou des ganguemineraux indésirables, généralement des minéraux silicatés ou des minéraux oxydés pour lesquels il n'y a souvent aucune valeur. Dans certains cas, les résidus ont été retraités pour récupérer la valeur perdue à mesure que la technologie de récupération du cuivre s'est améliorée. La teneur moyenne des minerais de cuivre au 21e siècle est inférieure à 0,6% de cuivre, la proportion de minerais économiques (y compris le cuivre) étant inférieure à 2% du volume total de la roche minérale. Un objectif clé dans le traitement métallurgique de tout minerai est la séparation des minéraux de minerai des minéraux de la gangue dans la roche.
La première étape de tout processus au sein d'un circuit de traitement métallurgique est un broyage ou une fragmentation précise , où la roche est concassée pour produire de petites particules (<100 μm) constituées de phases minérales individuelles. Ces particules sont ensuite séparées pour éliminer la gangue (résidus de roches), suivi ensuite d'un processus de libération physique des minerais de la roche. Le processus de libération des minerais de cuivre dépend du fait qu'il s'agisse de minerais d'oxyde ou de sulfure. [6]
Les étapes suivantes dépendent de la nature du minerai contenant le cuivre et de ce qui sera extrait. Pour les minerais oxydés, un processus de libération hydrométallurgique est normalement entrepris, qui utilise la nature soluble des minerais au profit de l'usine de traitement métallurgique. Pour les minerais sulfurés, à la fois secondaires (supergènes) et primaires (hypogènes), la flottation par mousse est utilisée pour séparer physiquement le minerai de la gangue. Pour les gisements spéciaux contenant du cuivre natif ou des sections de gisements riches en cuivre natif supergène, ce minéral peut être récupéré par un simple circuit gravitaire.
Flottation en mousse

Cellules de flottation par mousse pour concentrer les minéraux sulfurés de cuivre et de nickel, Falconbridge, Ontario.
Le processus moderne de flottation par mousse a été inventé indépendamment au début des années 1900 en Australie par CV Potter et à peu près à la même époque par GD Delprat. [7]

Bulles d'air chargées de sulfure de cuivre sur une cellule Jameson à l'usine de flottation de la mine Prominent Hillmine en Australie du Sud
Tous les minerais sulfurés primaires de sulfures de cuivre et la plupart des concentrés de sulfures de cuivre secondaires (étant la chalcocite) sont soumis à la fusion. Certains procédés de lixiviation en cuve ou de lixiviation sous pression existent pour solubiliser les concentrés de chalcocite et produire une cathode de cuivre à partir de la solution de lixiviation résultante, mais il s'agit d'une partie mineure du marché.
Les concentrés de carbonate sont un produit relativement mineur fabriqué à partir d'usines de cémentation du cuivre, généralement à l'étape finale d'une opération de lixiviation en tas. De tels concentrés de carbonate peuvent être traités par une installation d'extraction par solvant et d'extraction électrolytique (SX-EW) ou fondus.
Le minerai de cuivre est concassé et broyé à une taille telle qu'un degré acceptablement élevé de libération s'est produit entre les minerais de sulfure de cuivre et les minéraux de la gangue. Le minerai est ensuite mouillé, mis en suspension dans une bouillie et mélangé avec des xanthates ou d'autres réactifs, qui rendent les particules de sulfure hydrophobes. Les réactifs typiques comprennent l'éthylxanthate de potassium et l'éthylxanthate de sodium, mais des dithiophosphates et des dithiocarbamates sont également utilisés.
Le minerai traité est introduit dans un réservoir d'aération rempli d'eau contenant un tensioactif tel que le méthylisobutyl carbinol (MIBC). L'air est constamment forcé à travers la boue et les bulles d'air se fixent aux particules hydrophobes de sulfure de cuivre, qui sont conduites à la surface, où elles forment une mousse et sont écrémées. Ces écumages sont généralement soumis à une cellule de nettoyage-récupération pour éliminer les silicates en excès et pour éliminer les autres minéraux sulfurés qui peuvent avoir un impact néfaste sur la qualité du concentré (généralement, la galène) et le concentré final envoyé pour la fusion. La roche qui n'a pas flotté dans la cellule de flottation est soit rejetée en tant que résidus, soit traitée ultérieurement pour extraire d'autres métaux tels que le plomb (de la galène) et le zinc (de la sphalérite), s'ils existent. Pour améliorer l'efficacité du procédé, la chaux est utilisée pour élever le pH du bain d'eau, ce qui amène le collecteur à s'ioniser davantage et à se lier préférentiellement à la chalcopyrite (CuFeS 2) et à éviter la pyrite (FeS 2). Le fer existe dans les deux minéraux de la zone primaire. Les minerais de cuivre contenant de la chalcopyrite peuvent être concentrés pour produire un concentré contenant entre 20% et 30% de cuivre en concentré (généralement 27 à 29% de cuivre); le reste du concentré est du fer et du soufre dans la chalcopyrite, et des impuretés indésirables telles que des minéraux de gangue de silicate ou d'autres minéraux sulfurés, généralement des quantités mineures de pyrite, de sphalérite ou de galène. Les concentrés de chalcocite contiennent généralement entre 37% et 40% de cuivre dans le concentré, car la chalcocite ne contient pas de fer dans le minéral.
Extraction hydrométallurgique
Minerais sulfurés
Les sulfures secondaires - ceux formés par l'enrichissement secondaire supergène - sont résistants ( réfractaires ) à la lixiviation sulfurique. Ces minerais sont un mélange de carbonate de cuivre, de sulfate, de phosphate et de minéraux oxydés et de minéraux sulfurés secondaires, principalement de la chalcocite, mais d'autres minéraux tels que la digénite peuvent être importants dans certains gisements.
Les minerais supergènes riches en sulfures peuvent être concentrés par flottation par mousse. Un concentré typique de chalcocite peut contenir entre 37% et 40% de cuivre en sulfure, ce qui les rend relativement bon marché à fondre par rapport aux concentrés de chalcopyrite.
Certains dépôts de sulfure supergène peuvent être lessivés à l'aide d'un processus de lixiviation en tas par oxydation bactérienne pour oxyder les sulfures en acide sulfurique, ce qui permet également une lixiviation simultanée avec de l'acide sulfurique pour produire une solution de sulfate de cuivre. Comme pour les minerais oxydés, les technologies d'extraction par solvant et d'extraction électrolytique sont utilisées pour récupérer le cuivre de la solution de lixiviation mère.
Les minerais sulfurés supergènes riches en minéraux de cuivre natifs sont réfractaires au traitement par lixiviation à l'acide sulfurique à toutes les échelles de temps réalisables, et les particules métalliques denses ne réagissent pas avec les milieux de flottation par mousse. Généralement, si le cuivre natif est une partie mineure d'un profil de supergène, il ne sera pas récupéré et se rapportera aux résidus. Lorsqu'ils sont suffisamment riches, les gisements de minerai de cuivre natif peuvent être traités pour récupérer le cuivre contenu via un circuit de séparation par gravité où la densité du métal est utilisée pour le libérer des minéraux silicatés plus légers. Souvent, la nature de la gangue est importante, car les minerais de cuivre natifs riches en argile s'avèrent difficiles à libérer.
Minerais oxydés
Les corps de minerai de cuivre oxydé peuvent être traités via plusieurs procédés, avec des procédés hydrométallurgiques utilisés pour traiter les minerais d'oxyde dominés par les minéraux de carbonate de cuivre tels que l'azurite et la malachite, et d'autres minéraux solubles tels que les silicates comme la chrysocolle, ou les sulfates comme l'atacamite, etc.
Ces minerais d'oxyde sont généralement lessivés par de l'acide sulfurique, généralement dans un processus de lixiviation en tas ou de lixiviation en décharge pour libérer les minéraux de cuivre dans une solution d'acide sulfurique chargée de sulfate de cuivre en solution. La solution de sulfate de cuivre (la solution de lixiviation enceinte) est ensuite débarrassée du cuivre via une installation d'extraction par solvant et d'extraction électrolytique (SX-EW), l'acide sulfurique barré (dénudé) étant recyclé sur les tas. Alternativement, le cuivre peut être précipité hors de la solution mère en le mettant en contact avec de la ferraille ; un processus appelé cimentation. Le cuivre de ciment est normalement moins pur que le cuivre SX-EW. L'acide sulfurique est couramment utilisé comme agent de lixiviation pour l'oxyde de cuivre, bien qu'il soit possible d'utiliser de l'eau, en particulier pour les minerais riches en minéraux sulfatés ultra-solubles. [ citation nécessaire ]
En général, la flottation par mousse n'est pas utilisée pour concentrer les minerais d'oxyde de cuivre, car les minéraux oxydés ne réagissent pas aux produits chimiques ou au processus de flottation par mousse (c'est-à-dire qu'ils ne se lient pas aux produits chimiques à base de kérosène). Les minerais d'oxyde de cuivre ont parfois été traités par flottation par mousse via la sulfuration des minéraux oxydés avec certains produits chimiques qui réagissent avec les particules minérales d'oxyde pour produire un mince givre de sulfure (généralement de la chalcocite), qui peut ensuite être activé par l'usine de flottation par mousse.
Fusion de sulfure
Jusqu'à la seconde moitié du 20e siècle, la fusion des minerais sulfurés était presque le seul moyen de produire du cuivre métal à partir de minerais extraits ( production primaire de cuivre). Davenport, et al, ont noté en 2002 que même alors, 80% de la production mondiale de cuivre primaire provenait de minéraux de cuivre-fer-soufre et que la grande majorité de ceux-ci étaient traités par fusion.
Le cuivre était initialement récupéré à partir de minerais sulfurés en fondant directement le minerai dans un four. [9] Les fonderies étaient initialement situées près des mines pour minimiser le coût du transport. Cela a évité les coûts prohibitifs du transport des déchets minéraux et du soufre et du fer présents dans les minéraux contenant du cuivre. Cependant, à mesure que la concentration de cuivre dans les corps minéralisés diminuait, les coûts énergétiques de la fusion de tout le minerai devenaient également prohibitifs et il devenait nécessaire de concentrer d'abord les minerais.
Les techniques de concentration initiales comprenaient le tri manuel [10] et la concentration par gravité. Ils ont entraîné de fortes pertes de cuivre. Par conséquent, le développement du procédé de flottation par mousse a été une avancée majeure dans le traitement des minéraux. [11] Il a rendu possible le développement de la mine géante de Bingham Canyon dans l'Utah. [12]
Au XXe siècle, la plupart des minerais étaient concentrés avant d'être fondus. La fusion a été initialement entreprise à l'aide d'usines d'agglomération et de hauts fourneaux, [13] ou avec des torréfacteurs et des fours à réverbère. [14] La torréfaction et la fusion des fours à réverbère ont dominé la production primaire de cuivre jusqu'aux années 1960. [8]
Grillage
Le processus de torréfaction est généralement entrepris en combinaison avec des fours à réverbère. Dans le four de torréfaction, le concentré de cuivre est partiellement oxydé pour produire de la «calcine» et du dioxyde de soufre gazeux. La stoechiométrie de la réaction qui se produit est :
- 2 CuFeS 2 + 3 O 2 → 2 FeO + 2 CuS + 2 SO 2
La torréfaction laisse généralement plus de soufre dans le produit calciné (15 % dans le cas du torréfacteur de Mount Isa Mines [15] ) qu'une usine de frittage n'en laisse dans le produit fritté (environ 7 % dans le cas de la fonderie Electrolytic Refining and Smelting [ 16] ).
Depuis 2005, la torréfaction n'est plus courante dans le traitement des concentrés de cuivre, car sa combinaison avec des fours à réverbère n'est pas économe en énergie et la concentration de SO 2 dans les effluents gazeux du torréfacteur est trop diluée pour une capture rentable. [8] La fusion directe est désormais privilégiée, par exemple en utilisant les technologies de fusion suivantes : fusion éclair, fours Isasmelt, Noranda, Mitsubishi ou El Teniente. [8]
Fonte

Remplacement de la fusion au four à réverbère par la fusion éclair, lié au nombre de fonderies de cuivre utilisant cette technologie.
La fusion initiale du matériau à fondre est généralement appelée étape de fusion ou de fusion de la matte . Elle peut être entreprise dans une variété de fours, y compris les hauts fourneaux et les fours à réverbère largement obsolètes, ainsi que les fours éclair, les fours Isasmelt, etc. [8] Le produit de cette étape de fusion est un mélange de cuivre, de fer et de soufre qui est enrichi en cuivre, et que l'on appelle matte ou de fusion de la cuivre.[8] Le terme qualité de matte est normalement utilisé pour désigner la teneur en cuivre de la matte. [17]
Le but de l'étape de fusion de la matte est d'éliminer autant que possible les minéraux indésirables de fer, de soufre et de gangue (tels que la silice, la magnésie, l'alumine et le calcaire), tout en minimisant la perte de cuivre. [17] Ceci est réalisé en faisant réagir des sulfures de fer avec de l'oxygène (dans de l'air ou de l'air enrichi en oxygène) pour produire des oxydes de fer (principalement sous forme de FeO, mais avec un peu de magnétite (Fe 3O 4)) et du dioxyde de soufre. [17]
Le sulfure de cuivre et l'oxyde de fer peuvent se mélanger, mais lorsqu'une quantité suffisante de silice est ajoutée, une couche de laitier séparée se forme. [18] L'ajout de silice réduit également le point de fusion (ou, plus correctement, la température de liquidus) du laitier, ce qui signifie que le processus de fusion peut être opéré à une température plus basse. [18]
La réaction de formation de laitier est :
- FeO + SiO 2 → FeO.SiO 2[17]
Le laitier est moins dense que la matte, il forme donc une couche qui flotte au-dessus de la matte. [19]
Le cuivre peut être perdu de la matte de trois manières : sous forme d'oxyde cuivreux (Cu 2O) dissous dans le laitier, [20] sous forme de sulfure de cuivre dissous dans le laitier [21] ou sous forme de minuscules gouttelettes (ou granules ) de matte en suspension dans le laitier. scories. [22] [23]
La quantité de cuivre perdue sous forme d'oxyde de cuivre augmente à mesure que le potentiel d'oxygène du laitier augmente. [23] Le potentiel d'oxygène augmente généralement à mesure que la teneur en cuivre de la matte augmente. [24] Ainsi, la perte de cuivre sous forme d'oxyde augmente à mesure que la teneur en cuivre de la matte augmente. [25]
D'autre part, la solubilité du cuivre sulfurique dans le laitier diminue lorsque la teneur en cuivre de la matte augmente au-delà d'environ 40 %. [21] Nagamori a calculé que plus de la moitié du cuivre dissous dans les scories de mattes contenant moins de 50 % de cuivre est du cuivre sulfurique. Au-dessus de ce chiffre, le cuivre oxydé commence à dominer. [21]
La perte de cuivre sous forme de granules en suspension dans le laitier dépend de la taille des granules, de la viscosité du laitier et du temps de décantation disponible. [26] Rosenqvist a suggéré qu'environ la moitié des pertes de cuivre dans les scories étaient dues aux granules en suspension. [26]
La masse de laitier générée lors de l'étape de fusion dépend de la teneur en fer du matériau introduit dans le four de fusion et de la qualité de matte cible. Plus la teneur en fer de la charge est élevée, plus il faudra rejeter de fer dans le laitier pour un grade de matte donné. De même, l'augmentation de la teneur en matte cible nécessite le rejet de plus de fer et une augmentation du volume de laitier.
Ainsi, les deux facteurs qui affectent le plus la perte de cuivre dans les scories au stade de la fusion sont :
- qualité de matte
- masse de laitier. [18]
Cela signifie qu'il existe une limite pratique à la hauteur de la qualité de la matte si la perte de cuivre dans les scories doit être minimisée. Par conséquent, d'autres étapes de traitement (conversion et affinage au feu) sont nécessaires.
Les sous-sections suivantes décrivent brièvement certains des processus utilisés dans la fusion de la matte.
Fusion au four à réverbère
Les fours à réverbère sont des fours longs pouvant traiter des concentrés humides, secs ou torréfiés. [8] La plupart des fours à réverbère utilisés au cours des dernières années traitaient du concentré torréfié parce que le fait de mettre des matières premières sèches dans le four à réverbère est plus économe en énergie et parce que l'élimination d'une partie du soufre dans le torréfacteur se traduit par des qualités de matte plus élevées. [8]
L'alimentation du four à réverbère est ajoutée au four par des trous d'alimentation le long des côtés du four. [8] De la silice supplémentaire est normalement ajoutée pour aider à former le laitier. Le four est alimenté par des brûleurs utilisant du charbon pulvérisé, du mazout ou du gaz naturel [27] et la charge solide est fondue.
Les fours à réverbère peuvent en outre être alimentés avec du laitier fondu provenant de l'étape de conversion ultérieure pour récupérer le cuivre contenu et d'autres matériaux à haute teneur en cuivre. [27]
Du fait que le bain du four à réverbère est au repos, il se produit très peu d'oxydation de la charge (et donc très peu de soufre est éliminé du concentré). Il s'agit essentiellement d'un processus de fusion. [26] Par conséquent, les fours à réverbère à charge humide ont moins de cuivre dans leur produit de matte que les fours à charge calcinatrice, et ils ont également des pertes de cuivre plus faibles dans les scories. [27] Gill cite une valeur de cuivre dans les scories de 0,23 % pour un four à réverbère à charge humide contre 0,37 % pour un four à charge calcinatrice. [27]
Dans le cas des fours chargés en calcine, une partie importante du soufre a été éliminée lors de l'étape de grillage, et la calcine est constituée d'un mélange d'oxydes et de sulfures de cuivre et de fer. Le four à réverbère agit pour permettre à ces espèces de s'approcher de l'équilibre chimique à la température de fonctionnement du four (environ 1 600 °C à l'extrémité du brûleur du four et environ 1 200 °C à l'extrémité de la cheminée ; [28] la matte est d'environ 1 100 °C et le laitier est d'environ 1195 °C [27] ). Dans ce processus d'équilibrage, l'oxygène associé aux composés de cuivre échange avec le soufre associé aux composés de fer, augmentant la teneur en oxyde de fer du four, et les oxydes de fer interagissent avec la silice et d'autres matériaux oxydes pour former le laitier. [27]
La principale réaction d'équilibrage est :
- Cu 2O + FeS = Cu 2S + FeO [27]
Le laitier et la matte forment des couches distinctes qui peuvent être retirées du four sous forme de flux séparés. On laisse périodiquement la couche de laitier s'écouler à travers un trou dans la paroi du four au-dessus de la hauteur de la couche de matte. La matte est évacuée en la drainant par un trou dans des poches pour être acheminée par grue jusqu'aux convertisseurs. [27] Ce processus de vidange est connu sous le nom de piquage du four. [27] Le trou de coulée matte est normalement un trou à travers un bloc de cuivre refroidi à l'eau qui empêche l'érosion des briques réfractaires tapissant le four. Lorsque l'élimination de la matte ou du laitier est terminée, le trou est normalement bouché avec de l'argile, qui est retirée lorsque le four est prêt à être à nouveau coulé.
Les fours à réverbère étaient souvent utilisés pour traiter les scories fondues des convertisseurs afin de récupérer le cuivre contenu. [27] Celui-ci serait versé dans les fours à partir de poches portées par des grues. Cependant, le laitier du convertisseur est riche en magnétite [29] et une partie de cette magnétite précipiterait du laitier du convertisseur (en raison de son point de fusion plus élevé), formant une accrétion sur la sole du four à réverbère et nécessitant des arrêts du four pour enlever l'accrétion. [29] Cette formation d'accrétion limite la quantité de laitier de convertisseur qui peut être traitée dans un four à réverbère. [29]
Alors que les fours à réverbère ont de très faibles pertes de cuivre vers les scories, ils ne sont pas très économes en énergie et les faibles concentrations de dioxyde de soufre dans leurs effluents gazeux rendent sa capture non rentable. [8] Par conséquent, les exploitants de fonderies ont consacré beaucoup d'argent dans les années 1970 et 1980 au développement de nouveaux procédés de fusion du cuivre plus efficaces. [30] En outre, les technologies de fusion éclair ont été développées au cours des années précédentes et ont commencé à remplacer les fours à réverbère. En 2002, 20 des 30 fours à réverbère encore en activité en 1994 avaient été arrêtés. [8]
Fusion en four éclair
Dans la fusion éclair, le concentré est dispersé dans un courant d'air ou d'oxygène et les réactions de fusion sont en grande partie terminées alors que les particules minérales sont encore en vol. [30] Les particules ayant réagi se déposent ensuite dans un bain au fond du four, où elles se comportent comme le fait la calcine dans un four à réverbère. [31] Une couche de laitier se forme au-dessus de la couche de matte, et ils peuvent être extraits séparément du four. [31]
Conversion

Cuivre sans oxygène alias cuivre "Tough-pitch" (environ 98% pur), contenant de l'antimoine et du nickel
La matte, qui est produite dans la fonderie, contient 30 à 70 % de cuivre (selon le procédé utilisé et la philosophie d'exploitation de la fonderie), principalement sous forme de sulfure de cuivre, ainsi que de sulfure de fer. Le soufre est éliminé à haute température sous forme de dioxyde de soufre en soufflant de l'air à travers la matte fondue :
- 2 CuS + 3 O 2 → 2 CuO + 2 SO 2
- CuS + O2 2 → Cu + SO2
Dans une réaction parallèle, le sulfure de fer est converti en laitier :
- 2 FeS + 3 O 2 → 2 FeO + 2 SO 2
- 2 FeO + SiO 2 → Fe 2SiO 4
La pureté de ce produit est de 98%, il est connu sous le nom de blister en raison de la surface brisée créée par l'échappement de dioxyde de soufre gazeux lors du refroidissement des porcs ou des lingots de cuivre blister. Les sous-produits générés dans le processus sont le dioxyde de soufre et les scories. Le dioxyde de soufre est capturé pour être utilisé dans les processus de lixiviation antérieurs.
Affinage au feu
Le cuivre blister est placé dans un four à anodes, un four qui affine le cuivre blister en cuivre de qualité anode en deux étapes en éliminant la majeure partie du soufre et du fer restants, puis en éliminant l'oxygène introduit au cours de la première étape. Cette deuxième étape, souvent appelée polarisation , est réalisée en soufflant du gaz naturel, ou un autre agent réducteur, à travers l'oxyde de cuivre fondu. Lorsque cette flamme brûle en vert, indiquant le spectre d'oxydation du cuivre, l'oxygène a en grande partie été brûlé. Cela crée du cuivre à environ 99% pur.
Électroraffinage

Appareil pour l'affinage électrolytique du cuivre
Le cuivre est affiné par électrolyse. Les anodes coulées à partir de cuivre blister traité sont placées dans une solution aqueuse de 3 à 4% de sulfate de cuivre et de 10 à 16% d'acide sulfurique. Les cathodes sont de fines feuilles laminées de cuivre très pur ou, plus communément de nos jours, des feuilles de départ réutilisables en acier inoxydable (comme dans le procédé IsaKidd). [32] Un potentiel de seulement 0,2 à 0,4 volt est nécessaire pour que le processus commence. Dans les installations industrielles, des densités de courant jusqu'à 420 A/m 2 sont possibles. [33] À l'anode, le cuivre et les métaux moins nobles se dissolvent. Des métaux plus nobles tels que l'argent, l'or, le sélénium et le tellure se déposent au fond de la cellule sous forme de boue d'anode, qui forme un sous-produit commercialisable. Les ions cuivre(II) migrent à travers l'électrolyte vers la cathode. A la cathode, le cuivre métallique se plaque, mais les constituants moins nobles tels que l'arsenic et le zinc restent en solution à moins qu'une tension plus élevée ne soit utilisée. [34] Les réactions sont :
A l'anode : Cu (s) → Cu 2+ (aq) + 2e −
A la cathode : Cu 2+ (aq) + 2e − → Cu (s)
Commercialisation du concentré et du cuivre
Les concentrés de cuivre produits par les mines sont vendus aux fonderies et aux affineries qui traitent le minerai et raffinent le cuivre et facturent ce service via des frais de traitement (TC) et des frais de raffinage (RC). Le marché mondial des concentrés de cuivre [35] était évalué à 81 milliards de dollars américains en 2019 et devrait atteindre 93 milliards de dollars américains d'ici 2027, avec un TCAC de 2,5 %. Les TC sont facturés en dollars américains par tonne de concentré traité et les RC sont facturés en cents par livre traitée, libellés en dollars américains, avec des prix de référence fixés annuellement par les principales fonderies japonaises. Dans ce cas, le client peut être une fonderie, qui revend des lingots de cuivre blister à un raffineur, ou une fonderie-raffineur intégrée verticalement.
Une forme répandue de concentré de cuivre contient de l'or et de l'argent, comme celui produit par Bougainville Copper Limited à partir de la mine Panguna du début des années 1970 à la fin des années 1980.
Le contrat typique pour un mineur est libellé par rapport au prix du London Metal Exchange, moins les TC-RC et les pénalités ou crédits applicables. Des sanctions peuvent être imposées contre les concentrés de cuivre en fonction du niveau d'éléments nocifs tels que l'arsenic, le bismuth, le plomb ou le tungstène. Étant donné qu'une grande partie des gisements de sulfure de cuivre contiennent de l'argent ou de l'or en quantités appréciables, un crédit peut être versé au mineur pour ces métaux si leur concentration dans le concentré est supérieure à une certaine quantité. Habituellement, le raffineur ou la fonderie facture au mineur des frais basés sur la concentration; un contrat typique précisera qu'un crédit est dû pour chaque once de métal dans le concentré au-dessus d'une certaine concentration ; en dessous, s'il est récupéré, la fonderie conservera le métal et le revendra pour défrayer les coûts.
Le concentré de cuivre est négocié soit via des contrats au comptant, soit dans le cadre de contrats à long terme en tant que produit intermédiaire à part entière. Souvent, la fonderie vend elle-même le cuivre métal au nom du mineur. Le mineur est payé au prix au moment où la fonderie-affinerie effectue la vente, et non au prix à la date de livraison du concentré. Dans le cadre d'un système de prix de cotation, le prix est convenu à une date fixe dans le futur, généralement 90 jours à compter de la livraison à la fonderie.
La cathode en cuivre de qualité A est composée à 99,99 % de cuivre en feuilles de 1 cm d'épaisseur et d'environ 1 mètre carré pesant environ 200 livres. C'est une véritable marchandise, livrable et négociable sur les bourses des métaux de New York (COMEX), Londres (London Metals Exchange) et Shanghai (Shanghai Futures Exchange). Souvent, la cathode de cuivre est négociée indirectement sur les bourses via des bons de souscription, des options ou des contrats d'échange, de sorte que la majorité du cuivre est négociée sur le LME / COMEX / SFE, mais la livraison est réalisée directement, en déplaçant logistiquement le cuivre physique et en transférant la feuille de cuivre de les entrepôts physiques eux-mêmes.
La spécification chimique pour le cuivre de qualité électrolytique est la norme ASTM B 115-00 (une norme qui spécifie la pureté et la résistivité électrique maximale du produit).
Mr. Nick Sun [email protected]
Heure de publication : 27 septembre 2020