Co je to těžba mědi?
Těžba mědi se týká metod používaných k získávání mědi z jejích rud. Přeměna mědi se skládá z řady fyzikálních a elektrochemických procesů. Metody se vyvíjely a liší se podle země v závislosti na zdroji rudy, místních ekologických předpisech a dalších faktorech.
Jako ve všech těžebních provozech musí být ruda obvykle zhodnocována (koncentrována). Techniky zpracování závisí na povaze rudy. Pokud jsou rudou primárně sulfidické měděné nerosty (jako je chalkopyrit), ruda se drtí a mele, aby se uvolnily cenné nerosty z odpadních ("hlušinových") minerálů. Poté se zahustí pomocí minerální flotace. Koncentrát je pak typicky prodáván do vzdálených hutí, ačkoli některé velké doly mají tavírny umístěné poblíž. Taková kolokace dolů a hutí byla typičtější v 19. a na počátku 20. století, kdy menší hutě mohly být ekonomické. Sulfidové koncentráty se typicky taví v pecích, jako je blesková pec Outokumpu nebo Inco nebo pec ISASMELT, aby se vyrobil kamínek, který se musí přeměnit a rafinovat na výrobu anodové mědi. Konečně konečným procesem rafinace je elektrolýza. Z ekonomických a ekologických důvodů se mnoho vedlejších produktů těžby regeneruje. Například plynný oxid siřičitý je zachycován a přeměněn na kyselinu sírovou – která může být poté použita v procesu extrakce nebo prodána pro takové účely, jako je výroba hnojiv.
Oxidované měděné rudy lze upravovat hydrometalurgickou extrakcí.
Dějiny

Horníci v dole Tamarack v Copper Country, v roce 1905
Nejstarší důkazy o hutnění původní mědi za studena pocházejí z vykopávek v Çayönü Tepesi ve východní Anatolii, které se datují mezi 7200 až 6600 př.nl. [1] Mezi různými předměty považovanými za votivní nebo amulety byl jeden, který vypadal jako rybí háček a jeden jako šídlo. Další nález v jeskyni Shanidar v Mergasuru v Iráku obsahoval měděné korálky z roku 8 700 před Kristem. [2]
Jeden z nejstarších známých měděných dolů na světě, na rozdíl od využívání povrchových ložisek, je v Timna Valley v Izraeli od čtvrtého tisíciletí před naším letopočtem, s povrchovým využíváním od šestého do pátého tisíciletí. [3] [4]
Archeologické naleziště Pločnik v jihovýchodní Evropě (Srbsko) obsahuje nejstarší bezpečně datované [ pochybné – diskutujte ] důkazy o výrobě mědi při vysokých teplotách z doby 5 000 př. n. l. Nález v červnu 2010 rozšiřuje o dalších 500 let dřívější záznam o tavení mědi z Rudné Glavy (Srbsko), datovaný do 5. tisíciletí před naším letopočtem. [5]
Technologie tavení mědi dala vzniknout době měděné, neboli chalkolitické době, a poté době bronzové. Doba bronzová by nebyla možná bez lidí, kteří vyvinuli technologii tavení.
Koncentrace
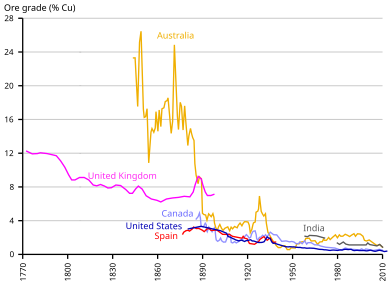
Klesající koncentrace mědi v rudách nyní vyžaduje předúpravu rud.
Většina měděných rud obsahuje pouze malé procento kovové mědi vázané v cenných rudních minerálech, přičemž zbytek rudy jsou nežádoucí horniny nebo gangueminerály, typicky silikátové minerály nebo oxidové minerály, pro které často není žádná hodnota. V některých případech byla hlušina odstraněna, aby se obnovila ztracená hodnota, protože technologie získávání mědi se zlepšila. Průměrná kvalita měděných rud ve 21. století je pod 0,6 % mědi, přičemž podíl ekonomických rudných minerálů (včetně mědi) je menší než 2 % z celkového objemu rudné horniny. Klíčovým cílem při metalurgickém zpracování jakékoli rudy je separace rudních minerálů od horninových minerálů v hornině.
První fází každého procesu v rámci okruhu metalurgického zpracování je přesné mletí nebo drcení , kdy se hornina drtí na malé částice (<100 μm) skládající se z jednotlivých minerálních fází. Tyto částice se poté oddělí, aby se odstranily hlušiny (zbytky hornin), poté následuje proces fyzického uvolnění rudných minerálů z horniny. Proces uvolňování měděných rud závisí na tom, zda se jedná o oxidové nebo sulfidové rudy. [6]
Další kroky závisí na povaze rudy obsahující měď a na tom, co se bude těžit. U oxidových rud se běžně provádí hydrometalurgický proces uvolňování, který využívá rozpustnou povahu rudných minerálů ve prospěch metalurgické úpravny. Pro sulfidové rudy, jak sekundární (supergen), tak primární (hypogen), se pěnová flotace používá k fyzickému oddělení rudy od hlušiny. U speciálních rud obsahujících nativní měď nebo části rudných těles bohatých na supergenní nativní měď lze tento minerál získat pomocí jednoduchého gravitačního okruhu.
Flotace pěny

Pěnové flotační články pro koncentraci minerálů mědi a sulfidu niklu, Falconbridge, Ontario.
Moderní pěnový flotační proces byl nezávisle vynalezen na počátku 20. století v Austrálii CV Potterem a přibližně ve stejnou dobu GD Delpratem. [7]

Vzduchové bubliny naložené sirníkem měďnatým na Jameson Cell ve flotační továrně Prominent Hillmine v jižní Austrálii
Všechny primární sulfidové rudy sulfidů mědi a většina koncentrátů sekundárních sulfidů mědi (které jsou chalkocitem) jsou podrobeny tavení. Existují některé procesy louhování v kádi nebo tlakového louhování pro solubilizaci chalkocitových koncentrátů a výrobu měděné katody z výsledného roztoku výluhu, ale to je menší část trhu.
Uhličitanové koncentráty jsou relativně menším produktem vyráběným z cementáren mědi, typicky jako konečný stupeň operace vyluhování haldy. Takové uhličitanové koncentráty mohou být zpracovány v zařízení pro extrakci rozpouštědlem a elektrolytické získávání (SX-EW) nebo tavení.
Měděná ruda se drtí a mele na takovou velikost, aby došlo k přijatelně vysokému stupni uvolňování mezi minerály sulfidové mědi a minerály hlušiny. Ruda se pak smáčí, suspenduje v kaši a mísí se s xantháty nebo jinými činidly, díky nimž jsou částice sulfidu hydrofobní. Typická činidla zahrnují ethylxanthát draselný a ethylxanthát sodný, ale používají se také dithiofosfáty a dithiokarbamáty.
Upravená ruda se zavádí do vodou naplněné provzdušňovací nádrže obsahující povrchově aktivní látku, jako je methylisobutylkarbinol (MIBC). Suspenzí je neustále protlačován vzduch a vzduchové bubliny se přichycují k hydrofobním částicím sulfidu mědi, které jsou odváděny na povrch, kde tvoří pěnu a jsou sbírány. Tyto stěrky jsou obecně podrobeny čistší zachycovací cele, aby se odstranily přebytečné křemičitany a odstranily se další sulfidové minerály, které mohou nepříznivě ovlivnit kvalitu koncentrátu (typicky galenit) a konečný koncentrát se posílá k tavení. Hornina, která nevyplavila ve flotační cele, se buď vyhodí jako hlušina, nebo se dále zpracuje k extrakci jiných kovů, jako je olovo (z galenitu) a zinek (ze sfaleritu), pokud existují. Pro zlepšení efektivity procesu se používá vápno ke zvýšení pH vodní lázně, čímž se kolektor více ionizuje a přednostně se váže na chalkopyrit (CuFeS 2) a vyhýbá se pyritu (FeS 2). Železo se vyskytuje v minerálech obou primárních zón. Měděné rudy obsahující chalkopyrit lze koncentrovat za vzniku koncentrátu s obsahem mezi 20 % a 30 % mědi v koncentrátu (obvykle 27–29 % mědi); zbytek koncentrátu tvoří železo a síra v chalkopyritu a nežádoucí nečistoty, jako jsou silikátové hlušinové minerály nebo jiné sulfidové minerály, typicky menší množství pyritu, sfaleritu nebo galenitu. Chalkocitové koncentráty obvykle obsahují 37 % až 40 % mědi v koncentrátu, protože chalkocit neobsahuje v minerálu žádné železo.
Hydrometalurgická těžba
Sulfidové rudy
Sekundární sulfidy – ty vzniklé supergenním sekundárním obohacením – jsou odolné ( refrakterní ) vůči sírovému vyluhování. Tyto rudy jsou směsí uhličitanu měďnatého, síranu, fosforečnanu a oxidových minerálů a sekundárních sulfidických minerálů, převážně chalkocitu, ale v některých ložiskách mohou být důležité i jiné minerály, jako je digenit.
Supergenní rudy bohaté na sulfidy lze koncentrovat pomocí pěnové flotace. Typický koncentrát chalkocitu může třídit mezi 37 % a 40 % mědi v sulfidu, což je činí relativně levně tavitelnými ve srovnání s chalkopyritovými koncentráty.
Některá supergenní sulfidová ložiska mohou být vyluhována pomocí bakteriálního oxidačního procesu vyluhování haldy k oxidaci sulfidů na kyselinu sírovou, což také umožňuje současné vyluhování s kyselinou sírovou za vzniku roztoku síranu měďnatého. Stejně jako u oxidových rud se k získávání mědi z vyluhovacího roztoku používají technologie extrakce rozpouštědlem a elektrolytické získávání.
Supergenní sulfidové rudy bohaté na přírodní měděné minerály jsou odolné vůči zpracování kyselinou sírovou vyluhováním ve všech proveditelných časových měřítcích a husté kovové částice nereagují s pěnovým flotačním médiem. Typicky, pokud je nativní měď minoritní součástí supergenního profilu, nebude obnovena a bude hlásit hlušinu. Když jsou dostatečně bohaté, mohou být tělesa nativní měděné rudy zpracována, aby se získala obsažená měď prostřednictvím gravitačního separačního okruhu, kde se hustota kovu používá k jeho uvolnění z lehčích silikátových minerálů. Často je důležitá povaha hlušiny, protože původní měděné rudy bohaté na jíl se obtížně osvobozují.
Oxidové rudy
Oxidovaná tělíska měděné rudy mohou být zpracována několika procesy, přičemž hydrometalurgické procesy používané k úpravě oxidových rud dominují minerály uhličitanu měďnatého, jako je azurit a malachit, a další rozpustné minerály, jako jsou křemičitany, jako je chryzokol, nebo sírany, jako je atacamit a tak dále.
Takové oxidové rudy se obvykle louhují kyselinou sírovou, obvykle v procesu loužení na hromadě nebo skládkovém loužení, aby se uvolnily minerály mědi do roztoku kyseliny sírové nasycené síranem měďnatým v roztoku. Roztok síranu měďnatého (těhotný louhovací roztok) je poté zbaven mědi prostřednictvím extrakce rozpouštědlem a elektrovýroby (SX-EW), přičemž zakázaná (denudovaná) kyselina sírová se recykluje zpět na hromady. Alternativně může být měď vysrážena z těhotného roztoku jeho kontaktováním se železným šrotem; proces zvaný cementace. Cementová měď je obvykle méně čistá než měď SX-EW. Kyselina sírová se běžně používá jako výluh pro oxid měďnatý, ačkoli je možné použít vodu, zejména pro rudy bohaté na ultrarozpustné síranové minerály. [ vyžaduje citaci ]
Obecně se pěnová flotace nepoužívá ke koncentraci rud oxidu měďnatého, protože oxidové minerály nereagují na chemikálie nebo proces pěnové flotace (tj. nevážou se na chemikálie na bázi petroleje). Rudy oxidu měďnatého byly příležitostně zpracovány pomocí pěnové flotace přes sulfidaci nerostů oxidu s určitými chemikáliemi, které reagují s částicemi oxidového minerálu za vzniku tenkého sulfidu (obvykle chalkocitu), který pak může být aktivován zařízením na flotaci pěny.
Tavení sulfidu
Až do druhé poloviny 20. století bylo tavení sirníkových rud téměř jediným způsobem výroby měděného kovu z vytěžených rud ( primární výroba mědi). Davenport a kol. v roce 2002 poznamenali, že i tehdy 80 % celosvětové primární produkce mědi pocházelo z měď-železo-sírových minerálů a že velká většina z nich byla zpracována tavením.
Měď se zpočátku získávala ze sulfidových rud přímým tavením rudy v peci. [9] Hutě byly zpočátku umístěny v blízkosti dolů, aby se minimalizovaly náklady na dopravu. Tím se předešlo neúměrným nákladům na přepravu odpadních minerálů a síry a železa přítomných v minerálech obsahujících měď. Jak však koncentrace mědi v rudných tělesech klesala, energetické náklady na tavení celé rudy se také staly neúnosnými a bylo nutné nejprve koncentrovat rudy.
Techniky počáteční koncentrace zahrnovaly ruční třídění [10] a gravitační koncentraci. Vedly k vysokým ztrátám mědi. V důsledku toho byl vývoj procesu pěnové flotace velkým krokem vpřed ve zpracování minerálů. [11] Umožnil rozvoj obřího dolu Bingham Canyon v Utahu. [12]
Ve dvacátém století byla většina rud koncentrována před tavením. Tavení se zpočátku provádělo v aglomeracích a vysokých pecích [13] nebo v pražírnách a dozvukových pecích. [14] Pražení a tavení v dozvukové peci dominovalo primární výrobě mědi až do 60. let 20. století. [8]
Pražení
Proces pražení se obecně provádí v kombinaci s dozvukovými pecemi. V pekáči se měděný koncentrát částečně oxiduje za vzniku „kalcinu“ a plynného oxidu siřičitého. Stechiometrie probíhající reakce je:
- 2 CuFeS 2 + 3 O 2 → 2 FeO + 2 CuS + 2 SO 2
Pražením obecně zůstává v kalcinovaném produktu více síry (15 % v případě pražírny v dolech Mount Isa [15] ), než aglomerace zanechá ve slinutém produktu (asi 7 % v případě huti pro elektrolytickou rafinaci a tavení [ 15] ). 16] ).
Od roku 2005 již není pražení při úpravě měděného koncentrátu běžné, protože jeho kombinace s dozvukovými pecemi není energeticky účinná a koncentrace SO 2 v odplynu z pražírny je příliš zředěná pro nákladově efektivní zachycení. [8] Nyní je upřednostňováno přímé tavení, např. pomocí následujících technologií tavení: bleskové tavení, pece Isasmelt, Noranda, Mitsubishi nebo El Teniente. [8]
Tavení

Náhrada tavení dozvukové pece bleskovým tavením, související s počtem měděných hutí využívajících tuto technologii.
Počáteční tavení materiálu určeného k tavení se obvykle nazývá tavení nebo matného tavení . Lze ji provádět v různých pecích, včetně převážně zastaralých vysokých pecí a pecí s dozvukem, jakož i bleskových pecí, pecí Isasmelt atd. [8] Produktem této fáze tavení je směs mědi, železa a síry, která je obohacen o měď, a která se nazývá mat nebo měděný mat.[8] Termín kamínek se běžně používá k označení obsahu mědi v kamínku. [17]
Účelem fáze matného tavení je odstranit co nejvíce nežádoucích minerálů železa, síry a hlušiny (jako je oxid křemičitý, hořčík, oxid hlinitý a vápenec) a zároveň minimalizovat ztráty mědi. [17] Toho je dosaženo reakcí sulfidů železa s kyslíkem (ve vzduchu nebo kyslíkem obohaceném vzduchu) za vzniku oxidů železa (hlavně jako FeO, ale s trochou magnetitu (Fe 3O 4)) a oxidu siřičitého. [17]
Sulfid měďnatý a oxid železa se mohou mísit, ale když se přidá dostatečné množství oxidu křemičitého, vytvoří se samostatná vrstva strusky. [18] Přidání oxidu křemičitého také snižuje bod tání (nebo přesněji teplotu likvidu) strusky, což znamená, že proces tavení může být provozován při nižší teplotě. [18]
Reakce tvorby strusky je:
- FeO + SiO 2 → FeO.SiO 2[17]
Struska je méně hustá než mat, takže tvoří vrstvu, která plave na povrchu matu. [19]
Měď se může z kamínku ztrácet třemi způsoby: jako oxid měďný (Cu 2O) rozpuštěný ve strusce, [20] jako sulfidická měď rozpuštěná ve strusce [21] nebo jako drobné kapičky (nebo hrudky ) kamínku suspendované ve strusce. struska. [22] [23]
Množství ztracené mědi, když se oxid mědi zvyšuje, když se zvyšuje kyslíkový potenciál strusky. [23] Potenciál kyslíku se obecně zvyšuje se zvyšujícím se obsahem mědi v kamínku. [24] Ztráta mědi jako oxidu se tedy zvyšuje se zvyšujícím se obsahem mědi v kamínku. [25]
Na druhé straně se rozpustnost sulfidické mědi ve strusce snižuje, když se obsah mědi v kamínku zvyšuje nad přibližně 40 %. [21] Nagamori vypočítal, že více než polovina mědi rozpuštěné ve struskách z kamínků obsahujících méně než 50 % mědi je sulfidická měď. Nad tímto číslem začíná dominovat oxidická měď. [21]
Ztráta mědi ve formě částic suspendovaných ve strusce závisí na velikosti částic, viskozitě strusky a dostupné době usazování. [26] Rosenqvist navrhl, že asi polovina ztrát mědi ve strusce byla způsobena suspendovanými granulemi. [26]
Množství strusky generované ve fázi tavení závisí na obsahu železa v materiálu přiváděném do tavicí pece a na cílové kvalitě kamínku. Čím větší je obsah železa v nástřiku, tím více železa bude muset být odmítnuto do strusky pro daný druh kamínku. Podobně zvýšení cílového jakosti kamínku vyžaduje vyřazení většího množství železa a zvýšení objemu strusky.
Dva faktory, které nejvíce ovlivňují ztrátu mědi na strusku ve fázi tavení, jsou:
- kamínek
- hmotnost strusky. [18]
To znamená, že existuje praktický limit toho, jak vysoký může být matný stupeň, pokud má být ztráta mědi na strusku minimalizována. Proto jsou nutné další stupně zpracování (konverze a zušlechťování ohněm).
Následující podkapitoly stručně popisují některé procesy používané při tavení matu.
Tavení v dozvukové peci
Reverberatorní pece jsou dlouhé pece, které mohou zpracovávat vlhký, suchý nebo pražený koncentrát. [8] Většina dozvukových pecí používaných v posledních letech zpracovávala upražený koncentrát, protože vkládání suchých vstupních materiálů do dozvukové pece je energeticky účinnější a protože odstranění části síry v pražiči má za následek vyšší kvalitu matného povrchu. [8]
Nástřik do pece s dozvukem se přidává do pece přívodními otvory po stranách pece. [8] Za normálních okolností se přidává další oxid křemičitý, aby pomohl vytvořit strusku. V peci se topí hořáky na práškové uhlí, topný olej nebo zemní plyn [27] a tuhá vsázka se taví.
Reverberatorní pece mohou být dodatečně napájeny roztavenou struskou z pozdějšího stupně konverze, aby se získala obsažená měď a další materiály s vysokým obsahem mědi. [27]
Vzhledem k tomu, že lázeň dozvukové pece je v klidu, dochází k velmi malé oxidaci nástřiku (a tudíž je z koncentrátu vyloučeno velmi málo síry). Jde v podstatě o proces tavení. [26] V důsledku toho mají dozvukové pece s mokrým plněním méně mědi ve svém kamínkovém produktu než pece s výpalem a také mají nižší ztráty mědi na strusku. [27] Gill uvádí hodnotu mědi ve strusce 0,23 % pro mokrou dozvukovou pec vs. 0,37 % pro pec plněnou kalcinem. [27]
V případě pecí s kalcinem byla značná část síry odstraněna během fáze pražení a kalcin se skládá ze směsi oxidů a sulfidů mědi a železa. Reverberatorní pec funguje tak, že umožňuje těmto druhům přiblížit se k chemické rovnováze při provozní teplotě pece (přibližně 1600 °C na konci hořáku a přibližně 1200 °C na konci kouřovodu; [28] kamínek má přibližně 1100 °C a struska má asi 1195 °C [27] ). V tomto ekvilibračním procesu se kyslík spojený se sloučeninami mědi vyměňuje se sírou spojenou se sloučeninami železa, čímž se zvyšuje obsah oxidu železa v peci, a oxidy železa interagují s oxidem křemičitým a jinými oxidovými materiály za vzniku strusky. [27]
Hlavní ekvilibrační reakce je:
- Cu 2O + FeS = Cu 2S + FeO [27]
Struska a kamínek tvoří odlišné vrstvy, které mohou být odstraněny z pece jako samostatné proudy. Vrstva strusky se periodicky nechává protékat otvorem ve stěně pece nad výškou vrstvy kamínku. Kamínek se odstraňuje odvodněním otvorem do naběraček, aby byl jeřábem dopraven ke konvertorům. [27] Tento proces odvodnění je známý jako odpich pece. [27] Matný odpichový otvor je obvykle otvor skrz vodou chlazený měděný blok, který zabraňuje erozi žáruvzdorných cihel vyzdívajících pec. Když je odstranění kamínku nebo strusky dokončeno, otvor se normálně ucpe jílem, který se odstraní, když je pec připravena k opětovnému odpichu.
Reverberatorní pece byly často používány ke zpracování roztavené konvertorové strusky, aby se získala měď. [27] Ten by se do pecí naléval z pánví nesených jeřáby. Konvertorová struska má však vysoký obsah magnetitu [29] a část tohoto magnetitu by se vysrážela z konvertorové strusky (kvůli jejímu vyššímu bodu tání), vytvořila by se na nístěji dozvukové pece a vyžadovalo by odstavení pece. odstranit akreci. [29] Tato tvorba akrece omezuje množství konvertorové strusky, kterou lze zpracovat v dozvukové peci. [29]
Zatímco dozvukové pece mají velmi nízké ztráty mědi na strusku, nejsou příliš energeticky účinné a nízké koncentrace oxidu siřičitého v jejich odpadních plynech činí jeho zachycování neekonomickým. [8] V důsledku toho provozovatelé hutí věnovali v 70. a 80. letech mnoho peněz na vývoj nových, účinnějších procesů tavení mědi. [30] Kromě toho byly v dřívějších letech vyvinuty technologie bleskového tavení, které začaly nahrazovat reverberační pece. Do roku 2002 bylo odstaveno 20 ze 30 dozvukových pecí, které byly v provozu ještě v roce 1994. [8]
Tavení v bleskové peci
Při bleskovém tavení je koncentrát dispergován v proudu vzduchu nebo kyslíku a tavicí reakce jsou z velké části dokončeny, zatímco minerální částice jsou stále v letu. [30] Zreagované částice se pak usazují v lázni na dně pece, kde se chovají jako kalcin v dozvukové peci. [31] Na povrchu matné vrstvy se vytvoří vrstva strusky, kterou lze z pece samostatně odpichovat. [31]
Konverze

Bezkyslíkatá měď alias „houževnatá“ měď (čistota cca 98 %), obsahující antimon a nikl
Kamínek, který se v huti vyrábí, obsahuje 30–70 % mědi (v závislosti na použitém procesu a provozní filozofii huti), především jako sulfid mědi a také sulfid železa. Síra se odstraňuje při vysoké teplotě jako oxid siřičitý profukováním vzduchu roztaveným kamínkem:
- 2 CuS + 3 O 2 → 2 CuO + 2 SO 2
- CuS + O 2 → Cu + SO 2
V paralelní reakci se sulfid železa přemění na strusku:
- 2 FeS + 3 O 2 → 2 FeO + 2 SO 2
- 2 FeO + SiO 2 → Fe 2SiO 4
Čistota tohoto produktu je 98 %, je znám jako puchýř , protože jeho povrch vznikl únikem oxidu siřičitého při ochlazování puchýřových měděných slitek nebo ingotů. Vedlejšími produkty vznikajícími při procesu jsou oxid siřičitý a struska. Oxid siřičitý se zachycuje pro použití v dřívějších procesech loužení.
Rafinace ohněm
Bublinková měď se vloží do anodové pece, pece, která zušlechťuje bublinkovou měď na anodovou měď ve dvou stupních odstraněním většiny zbývající síry a železa a poté odstraněním kyslíku zavedeného během prvního stupně. Tato druhá fáze, často označovaná jako pole, se provádí profukováním zemního plynu nebo jiného redukčního činidla skrz roztavený oxid mědi. Když tento plamen hoří zeleně, což ukazuje na spektrum oxidace mědi, kyslík byl většinou spálen. To vytváří měď s čistotou asi 99 %.
Elektrorafinace

Zařízení pro elektrolytickou rafinaci mědi
Měď se rafinuje elektrolýzou. Anody odlité ze zpracované měděné bubliny jsou umístěny do vodného roztoku 3–4 % síranu měďnatého a 10–16 % kyseliny sírové. Katody jsou tenké válcované plechy z vysoce čisté mědi nebo v dnešní době častěji znovu použitelné výchozí plechy z nerezové oceli (jako v procesu IsaKidd). [32] Pro zahájení procesu je zapotřebí potenciál pouze 0,2–0,4 voltu. V průmyslových závodech jsou možné proudové hustoty až 420 A/m 2 . [33] Na anodě se rozpouští měď a méně ušlechtilé kovy. Ušlechtilejší kovy jako stříbro, zlato, selen a telur se usazují na dně článku jako anodový sliz, který tvoří prodejný vedlejší produkt. Ionty mědi (II) migrují elektrolytem ke katodě. Na katodě, měděné plechy, ale méně ušlechtilé složky, jako je arsen a zinek, zůstávají v roztoku, pokud není použito vyšší napětí. [34] Reakce jsou:
Na anodě: Cu (s) → Cu 2+ (aq) + 2e −
Na katodě: Cu 2+ (aq) + 2e − → Cu (s)
Koncentrovaný a měděný marketing
Koncentráty mědi vyrobené v dolech se prodávají hutím a rafineriím, které upravují rudu a zušlechťují měď a za tuto službu účtují poplatky za úpravu (TC) a rafinérské poplatky (RC). Globální trh s měděným koncentrátem [35] byl v roce 2019 oceněn na 81 miliard USD a předpokládá se, že do roku 2027 dosáhne 93 miliard USD a rozšíří se při CAGR 2,5 %. TC jsou účtovány v USD za tunu upraveného koncentrátu a RC jsou účtovány v centech za libru upraveného, denominované v amerických dolarech, s referenčními cenami, které každoročně stanovují hlavní japonské hutě. Zákazníkem může být v tomto případě tavič, který dále prodává blistrové měděné ingoty rafinerii, nebo tavič-rafinér, který je vertikálně integrovaný.
Jedna převládající forma měděného koncentrátu obsahuje zlato a stříbro, jako ta, kterou vyrábí Bougainville Copper Limited z dolu Panguna od počátku 70. do konce 80. let.
Typická smlouva pro těžaře je denominována proti ceně na londýnské burze kovů, po odečtení TC-RC a všech příslušných pokut nebo kreditů. Tresty mohou být u měděných koncentrátů stanoveny podle úrovně škodlivých prvků, jako je arsen, vizmut, olovo nebo wolfram. Protože velká část tělísek rud sulfidů mědi obsahuje stříbro nebo zlato v nezanedbatelném množství, lze za tyto kovy těžaři připsat kredit, pokud jejich koncentrace v koncentrátu překročí určité množství. Rafinér nebo huť obvykle účtuje těžaři poplatek na základě koncentrace; typická smlouva bude specifikovat, že kredit je splatný za každou unci kovu v koncentrátu nad určitou koncentraci; pod tím, pokud se získá, huť si kov ponechá a prodá jej na úhradu nákladů.
Měděný koncentrát je obchodován buď prostřednictvím spotových kontraktů, nebo na základě dlouhodobých kontraktů jako samostatný meziprodukt. Huť často prodává měděný kov sám jménem horníka. Těžaři se platí cena v době, kdy huť-rafinér provede prodej, nikoli cena v den dodání koncentrátu. V rámci systému cenové nabídky je cena dohodnuta k pevnému datu v budoucnosti, obvykle 90 dnů od doby dodání do huti.
Měděná katoda třídy A je z 99,99 % mědi v plátech o tloušťce 1 cm a přibližně 1 metr čtvereční o hmotnosti přibližně 200 liber. Jde o skutečnou komoditu, kterou lze doručit a obchodovat na burzách kovů v New Yorku (COMEX), Londýně (London Metals Exchange) a Šanghaji (Shanghai Futures Exchange). S měděnou katodou se na burzách často obchoduje nepřímo prostřednictvím warrantů, opcí nebo swapových smluv tak, že většina mědi se obchoduje na LME/COMEX/SFE, ale dodání je dosaženo přímo, logistickým přesunem fyzické mědi a převodem měděného plechu z samotné fyzické sklady.
Chemická specifikace pro elektrolytickou měď je ASTM B 115-00 (norma, která specifikuje čistotu a maximální elektrický odpor produktu).
Mr. Nick Sun [email protected]
Čas odeslání: 27. září 2020