Apa itu Ekstraksi Tembaga?
Ekstraksi tembaga mengacu pada metode yang digunakan untuk mendapatkan tembaga dari bijihnya. Konversi tembaga terdiri dari serangkaian proses fisik dan elektrokimia. Metode telah berkembang dan bervariasi di setiap negara tergantung pada sumber bijih, peraturan lingkungan setempat, dan faktor lainnya.
Seperti dalam semua operasi penambangan, bijih biasanya harus diambil manfaat (konsentrat). Teknik pengolahan tergantung pada sifat bijih. Jika bijih terutama mineral tembaga sulfida (seperti kalkopirit), bijih dihancurkan dan digiling untuk membebaskan mineral berharga dari mineral limbah ('gangue'). Kemudian dipekatkan menggunakan flotasi mineral. Konsentrat biasanya kemudian dijual ke smelter yang jauh, meskipun beberapa tambang besar memiliki smelter yang berlokasi di dekatnya. Kolokasi tambang dan peleburan seperti itu lebih umum terjadi pada abad ke-19 dan awal abad ke-20, ketika peleburan yang lebih kecil dapat menjadi ekonomis. Konsentrat sulfida biasanya dilebur dalam tungku seperti tungku flash Outokumpu atau Inco atau tungku ISASMELT untuk menghasilkan matte, yang harus diubah dan dimurnikan untuk menghasilkan tembaga anoda. Akhirnya, proses pemurnian terakhir adalah elektrolisis. Untuk alasan ekonomi dan lingkungan, banyak produk sampingan dari ekstraksi direklamasi. Gas belerang dioksida, misalnya, ditangkap dan diubah menjadi asam sulfat — yang kemudian dapat digunakan dalam proses ekstraksi atau dijual untuk tujuan seperti pembuatan pupuk.
Bijih tembaga teroksidasi dapat diolah dengan ekstraksi hidrometalurgi.
Sejarah

Penambang di tambang Tamarack di Negara Tembaga, pada tahun 1905
Bukti paling awal dari pemalu dingin tembaga asli berasal dari penggalian di ayönü Tepesi di Anatolia timur, yang berlangsung antara 7200 hingga 6600 SM. [1] Di antara berbagai barang yang dianggap sebagai nazar atau jimat, ada satu yang tampak seperti kail dan satu lagi seperti penusuk. Temuan lain, di Gua Shanidar di Mergasur, Irak, berisi manik-manik tembaga, berasal dari 8.700 SM. [2]
Salah satu tambang tembaga tertua di dunia, yang bertentangan dengan penggunaan deposit permukaan, adalah di Lembah Timna, Israel, sejak milenium keempat SM, dengan penggunaan deposit permukaan sejak milenium keenam hingga kelima. [3] [4]
Situs arkeologi Pločnik di Eropa tenggara (Serbia) berisi bukti [ meragukan – diskusikan ] tertua yang tertanggal dengan aman tentang pembuatan tembaga pada suhu tinggi, dari 5.000 SM. Penemuan pada bulan Juni 2010 memperpanjang 500 tahun tambahan rekor peleburan tembaga sebelumnya dari Rudna Glava (Serbia), tertanggal hingga milenium ke-5 SM. [5]
Teknologi peleburan tembaga memunculkan Zaman Tembaga, alias Zaman Kalkolitik, dan kemudian Zaman Perunggu. Zaman Perunggu tidak akan mungkin terjadi tanpa manusia mengembangkan teknologi peleburan.
Konsentrasi
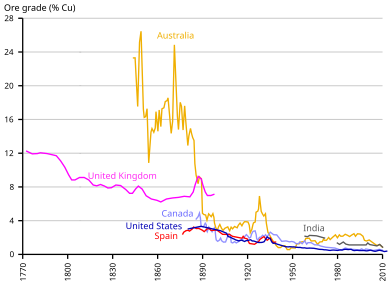
Penurunan konsentrasi tembaga dalam bijih sekarang membutuhkan pra-perawatan bijih.
Sebagian besar bijih tembaga hanya mengandung sebagian kecil logam tembaga yang terikat di dalam mineral bijih berharga, dengan sisa bijih berupa batuan atau mineral gangue yang tidak diinginkan, biasanya mineral silikat atau mineral oksida yang seringkali tidak ada nilainya. Dalam beberapa kasus, tailing telah ditarik untuk memulihkan nilai yang hilang karena teknologi untuk memulihkan tembaga telah meningkat. Nilai rata-rata bijih tembaga di abad ke-21 adalah di bawah 0,6% tembaga, dengan proporsi mineral bijih ekonomis (termasuk tembaga) kurang dari 2% dari total volume batuan bijih. Tujuan utama dalam pengolahan metalurgi dari setiap bijih adalah pemisahan mineral bijih dari mineral gangue di dalam batuan.
Tahap pertama dari setiap proses dalam rangkaian perawatan metalurgi adalah penggilingan atau penghancuran yang akurat , di mana batu dihancurkan untuk menghasilkan partikel kecil (<100 m) yang terdiri dari fase mineral individu. Partikel-partikel ini kemudian dipisahkan untuk menghilangkan gangue (residu batuan), kemudian dilanjutkan dengan proses pembebasan fisik mineral bijih dari batuan. Proses pembebasan bijih tembaga tergantung pada apakah mereka bijih oksida atau sulfida. [6]
Langkah selanjutnya tergantung pada sifat bijih yang mengandung tembaga dan apa yang akan diekstraksi. Untuk bijih oksida, proses pembebasan hidrometalurgi biasanya dilakukan, yang menggunakan sifat larut dari mineral bijih untuk keuntungan dari pabrik pengolahan metalurgi. Untuk bijih sulfida, baik sekunder (supergen) dan primer (hypogene), flotasi buih digunakan untuk memisahkan bijih dari gangue secara fisik. Untuk badan bijih bantalan tembaga asli khusus atau bagian dari badan bijih yang kaya akan tembaga asli supergen, mineral ini dapat diperoleh kembali dengan sirkuit gravitasi sederhana.
Flotasi buih

Sel flotasi buih untuk mengkonsentrasikan mineral tembaga dan nikel sulfida, Falconbridge, Ontario.
Proses flotasi buih modern ditemukan secara independen pada awal 1900-an di Australia oleh CV Potter dan sekitar waktu yang sama oleh GD Delprat. [7]

Tembaga sulfida memuat gelembung udara pada Sel Jameson di pabrik flotasi Prominent Hillmine di Australia Selatan
Semua bijih sulfida primer dari sulfida tembaga, dan sebagian besar konsentrat sulfida tembaga sekunder (menjadi kalkosit), mengalami peleburan. Beberapa proses pelindian tong atau pelindian bertekanan ada untuk melarutkan konsentrat kalkosit dan menghasilkan katoda tembaga dari larutan lindi yang dihasilkan, tetapi ini adalah bagian kecil dari pasar.
Konsentrat karbonat adalah produk yang relatif kecil yang dihasilkan dari pabrik sementasi tembaga, biasanya sebagai tahap akhir dari operasi pelindian tumpukan. Konsentrat karbonat tersebut dapat diolah dengan ekstraksi pelarut dan pabrik electrowinning (SX-EW) atau dilebur.
Bijih tembaga dihancurkan dan digiling ke ukuran sedemikian rupa sehingga tingkat pembebasan tinggi yang dapat diterima telah terjadi antara mineral bijih tembaga sulfida dan mineral gangue. Bijih tersebut kemudian dibasahi, disuspensikan dalam bubur, dan dicampur dengan xantat atau reagen lainnya, yang membuat partikel sulfida menjadi hidrofobik. Reagen yang khas termasuk kalium etilksantat dan natrium etilksantat, tetapi ditiofosfat dan ditiokarbamat juga digunakan.
Bijih yang diolah dimasukkan ke tangki aerasi berisi air yang mengandung surfaktan seperti methylisobutyl carbinol (MIBC). Udara terus-menerus dipaksa melalui bubur dan gelembung udara menempel pada partikel tembaga sulfida hidrofobik, yang dibawa ke permukaan, di mana mereka membentuk buih dan dihilangkan. Skimming ini umumnya dikenai sel pembersih-pemulung untuk menghilangkan kelebihan silikat dan untuk menghilangkan mineral sulfida lain yang dapat merusak kualitas konsentrat (biasanya, galena), dan konsentrat akhir dikirim untuk peleburan. Batuan yang belum terapung dalam sel flotasi dibuang sebagai tailing atau diproses lebih lanjut untuk mengekstrak logam lain seperti timbal (dari galena) dan seng (dari sfalerit), jika ada. Untuk meningkatkan efisiensi proses, kapur digunakan untuk menaikkan pH penangas air, menyebabkan kolektor lebih terionisasi dan lebih suka berikatan dengan kalkopirit (CuFeS 2) dan menghindari pirit (FeS 2). Besi ada di kedua mineral zona primer. Bijih tembaga yang mengandung kalkopirit dapat dipekatkan untuk menghasilkan konsentrat dengan antara 20% dan 30% tembaga dalam konsentrat (biasanya 27-29% tembaga); sisa konsentratnya adalah besi dan belerang dalam kalkopirit, dan pengotor yang tidak diinginkan seperti mineral gangue silikat atau mineral sulfida lainnya, biasanya sejumlah kecil pirit, sphalerit atau galena. Konsentrat kalkosit biasanya memiliki kadar antara 37% dan 40% tembaga dalam konsentrat, karena kalkosit tidak memiliki zat besi di dalam mineral.
Ekstraksi hidrometalurgi
bijih sulfida
Sulfida sekunder - yang dibentuk oleh pengayaan sekunder supergen - tahan ( tahan api ) terhadap pencucian sulfat. Bijih ini adalah campuran mineral tembaga karbonat, sulfat, fosfat, dan oksida dan mineral sulfida sekunder, terutama kalkosit tetapi mineral lain seperti digenit dapat menjadi penting dalam beberapa endapan.
Bijih supergen yang kaya akan sulfida dapat dipekatkan menggunakan flotasi buih. Konsentrat khas kalkosit dapat memiliki kadar antara 37% dan 40% tembaga dalam sulfida, membuatnya relatif murah untuk dilebur dibandingkan dengan konsentrat kalkopirit.
Beberapa endapan supergen sulfida dapat dilindi menggunakan proses pelindian tumpukan oksidasi bakteri untuk mengoksidasi sulfida menjadi asam sulfat, yang juga memungkinkan pelindian simultan dengan asam sulfat untuk menghasilkan larutan tembaga sulfat. Seperti bijih oksida, ekstraksi pelarut dan teknologi electrowinning digunakan untuk memulihkan tembaga dari larutan pelindian hamil.
Bijih supergen sulfida yang kaya akan mineral tembaga asli tahan terhadap perlakuan dengan pencucian asam sulfat pada semua skala waktu yang memungkinkan, dan partikel logam padat tidak bereaksi dengan media flotasi buih. Biasanya, jika tembaga asli adalah bagian kecil dari profil supergen, itu tidak akan dipulihkan dan akan dilaporkan ke tailing. Ketika cukup kaya, badan bijih tembaga asli dapat diolah untuk memulihkan tembaga yang terkandung melalui sirkuit pemisahan gravitasi di mana kerapatan logam digunakan untuk membebaskannya dari mineral silikat yang lebih ringan. Seringkali, sifat gangue itu penting, karena bijih tembaga asli yang kaya akan tanah liat terbukti sulit untuk dibebaskan.
bijih oksida
Badan bijih tembaga yang teroksidasi dapat diolah melalui beberapa proses, dengan proses hidrometalurgi yang digunakan untuk mengolah bijih oksida yang didominasi oleh mineral tembaga karbonat seperti azurit dan perunggu, dan mineral terlarut lainnya seperti silikat seperti chrysocolla, atau sulfat seperti atacamit dan sebagainya.
Bijih oksida tersebut biasanya dilindi dengan asam sulfat, biasanya dalam proses pelindian tumpukan atau pelindian pembuangan untuk membebaskan mineral tembaga ke dalam larutan asam sulfat yang sarat dengan tembaga sulfat dalam larutan. Larutan tembaga sulfat (larutan pelindian hamil) kemudian dilepaskan dari tembaga melalui ekstraksi pelarut dan pabrik electrowinning (SX-EW), dengan asam sulfat yang dilarang (digunduli) didaur ulang kembali ke tumpukan. Sebagai alternatif, tembaga dapat diendapkan dari larutan hamil dengan mengontakkannya dengan besi tua; proses yang disebut sementasi. Tembaga semen biasanya kurang murni dibandingkan tembaga SX-EW. Umumnya asam sulfat digunakan sebagai pelindian untuk oksida tembaga, meskipun dimungkinkan untuk menggunakan air, terutama untuk bijih yang kaya akan mineral sulfat yang sangat larut. [ rujukan? ]
Secara umum, flotasi buih tidak digunakan untuk mengkonsentrasikan bijih tembaga oksida, karena mineral oksida tidak responsif terhadap bahan kimia atau proses flotasi buih (yaitu; mereka tidak mengikat bahan kimia berbasis minyak tanah). Bijih tembaga oksida kadang-kadang diolah melalui flotasi buih melalui sulfidasi mineral oksida dengan bahan kimia tertentu yang bereaksi dengan partikel mineral oksida untuk menghasilkan lapisan tipis sulfida (biasanya kalkosit), yang kemudian dapat diaktifkan oleh pabrik flotasi buih.
Peleburan sulfida
Sampai paruh kedua abad ke-20, peleburan bijih sulfida hampir merupakan satu-satunya cara untuk menghasilkan logam tembaga dari bijih yang ditambang ( primer ). Davenport, et al, mencatat pada tahun 2002 bahwa bahkan 80% dari produksi tembaga primer global berasal dari mineral tembaga-besi-sulfur dan sebagian besar dari ini diolah dengan peleburan.
Tembaga awalnya diperoleh dari bijih sulfida dengan langsung melebur bijih dalam tungku. [9] Pabrik peleburan pada awalnya terletak di dekat tambang untuk meminimalkan biaya transportasi. Ini menghindari biaya yang mahal untuk mengangkut mineral limbah dan sulfur serta besi yang ada dalam mineral yang mengandung tembaga. Namun, karena konsentrasi tembaga dalam badan bijih menurun, biaya energi peleburan seluruh bijih juga menjadi penghalang, dan menjadi perlu untuk mengonsentrasikan bijih terlebih dahulu.
Teknik konsentrasi awal termasuk penyortiran tangan [10] dan konsentrasi gravitasi. Mereka menghasilkan kerugian tembaga yang tinggi. Akibatnya, pengembangan proses flotasi buih merupakan langkah maju yang besar dalam pengolahan mineral. [11] Ini memungkinkan pengembangan tambang Bingham Canyon raksasa di Utah. [12]
Pada abad kedua puluh, sebagian besar bijih terkonsentrasi sebelum peleburan. Peleburan awalnya dilakukan dengan menggunakan pabrik sinter dan tanur sembur, [13] atau dengan pemanggang dan tungku reverberatory. [14] Pemanggangan dan peleburan tungku reverberatory mendominasi produksi tembaga primer sampai tahun 1960-an. [8]
Memanggang
Proses pemanggangan umumnya dilakukan dalam kombinasi dengan tungku reverberatory. Dalam pemanggang, konsentrat tembaga dioksidasi sebagian untuk menghasilkan "kalsin" dan gas sulfur dioksida. Stoikiometri reaksi yang terjadi adalah:
- 2 CuFeS 2 + 3 O 2 → 2 FeO + 2 CuS + 2 SO 2
Pemanggangan umumnya meninggalkan lebih banyak belerang dalam produk yang dikalsinasi (15% dalam kasus pemanggang di Pertambangan Gunung Isa [15] ) daripada daun tanaman sinter dalam produk sinter (sekitar 7% dalam kasus Pemurnian Elektrolit dan Peleburan peleburan [ 16] ).
Mulai tahun 2005, pemanggangan tidak lagi umum dalam pengolahan konsentrat tembaga, karena kombinasinya dengan tungku reverberatory tidak hemat energi dan konsentrasi SO 2 dalam offgas pemanggang terlalu encer untuk penangkapan yang hemat biaya. [8] Peleburan langsung sekarang lebih disukai, misalnya menggunakan teknologi peleburan berikut: peleburan cepat, tungku Isasmelt, Noranda, Mitsubishi atau El Teniente. [8]
Peleburan

Penggantian peleburan reverberatory furnace dengan flash smelting, terkait dengan jumlah smelter tembaga yang menggunakan teknologi ini.
Peleburan awal bahan yang akan dilebur biasanya disebut sebagai tahap peleburan atau peleburan matte . Ini dapat dilakukan di berbagai tungku, termasuk tungku ledakan dan tungku reverberatory yang sebagian besar usang, serta tungku flash, tungku Isasmelt, dll. [8] Produk dari tahap peleburan ini adalah campuran tembaga, besi dan belerang yang diperkaya dengan tembaga, dan yang disebut matte atau tembaga matte.[8] Istilah kelas matte biasanya digunakan untuk merujuk pada kandungan tembaga dari matte. [17]
Tujuan dari tahap peleburan matte adalah untuk menghilangkan sebanyak mungkin mineral besi, belerang, dan gangue yang tidak diinginkan (seperti silika, magnesia, alumina, dan batu kapur), sambil meminimalkan hilangnya tembaga. [17] Hal ini dicapai dengan mereaksikan sulfida besi dengan oksigen (di udara atau udara yang kaya oksigen) untuk menghasilkan oksida besi (terutama sebagai FeO, tetapi dengan beberapa magnetit (Fe 3O 4)) dan belerang dioksida. [17]
Tembaga sulfida dan oksida besi dapat bercampur, tetapi ketika silika yang cukup ditambahkan, lapisan terak terpisah akan terbentuk. [18] Penambahan silika juga mengurangi titik leleh (atau, lebih tepatnya, suhu liquidus) terak, yang berarti bahwa proses peleburan dapat dioperasikan pada suhu yang lebih rendah. [18]
Reaksi pembentukan terak adalah:
- FeO + SiO 2 → FeO.SiO 2[17]
Terak kurang padat dari matte, sehingga membentuk lapisan yang mengapung di atas matte. [19]
Tembaga dapat hilang dari matte dengan tiga cara: sebagai tembaga oksida (Cu 2O) yang dilarutkan dalam terak, [20] sebagai tembaga sulfida yang dilarutkan dalam terak [21] atau sebagai tetesan kecil (atau butiran kecil ) dari matte yang tersuspensi dalam terak. [22] [23]
Jumlah tembaga yang hilang sebagai tembaga oksida meningkat dengan meningkatnya potensi oksigen terak. [23] Potensi oksigen umumnya meningkat karena kandungan tembaga matte meningkat. [24] Dengan demikian, hilangnya tembaga sebagai oksida meningkat seiring dengan meningkatnya kandungan tembaga pada matte. [25]
Di sisi lain, kelarutan tembaga sulfida dalam terak menurun karena kandungan tembaga dari matte meningkat melebihi sekitar 40%. [21] Nagamori menghitung bahwa lebih dari setengah tembaga terlarut dalam terak dari matte yang mengandung kurang dari 50% tembaga adalah tembaga sulfida. Di atas angka ini, tembaga oksida mulai mendominasi. [21]
Hilangnya tembaga sebagai butiran tersuspensi dalam terak tergantung pada ukuran butiran, viskositas terak dan waktu pengendapan yang tersedia. [26] Rosenqvist menyarankan bahwa sekitar setengah kerugian tembaga terak adalah karena prills ditangguhkan. [26]
Massa terak yang dihasilkan pada tahap peleburan tergantung pada kandungan besi dari bahan yang dimasukkan ke dalam tungku peleburan dan tingkat matte target. Semakin besar kandungan besi umpan, semakin banyak besi yang perlu dibuang ke terak untuk tingkat matte yang diberikan. Demikian pula, meningkatkan tingkat matte target membutuhkan penolakan lebih banyak besi dan peningkatan volume terak.
Dengan demikian, dua faktor yang paling mempengaruhi hilangnya tembaga menjadi terak pada tahap peleburan adalah:
- kelas matte
- massa terak. [18]
Ini berarti bahwa ada batasan praktis tentang seberapa tinggi kadar matte jika kehilangan tembaga menjadi terak ingin diminimalkan. Oleh karena itu, diperlukan tahapan pengolahan lebih lanjut (konversi dan pemurnian api).
Subbagian berikut menjelaskan secara singkat beberapa proses yang digunakan dalam peleburan matte.
Peleburan tungku reverberatory
Tungku reverberatory adalah tungku panjang yang dapat mengolah konsentrat basah, kering atau panggang. [8] Sebagian besar tungku reverberatory yang digunakan pada tahun-tahun terakhir mengolah konsentrat panggang karena memasukkan bahan pakan kering ke dalam tungku reverberatory lebih hemat energi, dan karena penghilangan beberapa belerang dalam roaster menghasilkan nilai matte yang lebih tinggi. [8]
Umpan tungku reverberatory ditambahkan ke tungku melalui lubang umpan di sepanjang sisi tungku. [8] Silika tambahan biasanya ditambahkan untuk membantu membentuk terak. Tungku dibakar dengan pembakar menggunakan batu bara bubuk, bahan bakar minyak atau gas alam [27] dan muatan padatnya dilebur.
Tungku reverberatory tambahan dapat diumpankan dengan terak cair dari tahap konversi kemudian untuk memulihkan tembaga yang terkandung dan bahan lainnya dengan kandungan tembaga tinggi. [27]
Karena rendaman tungku reverberatory diam, sangat sedikit oksidasi umpan yang terjadi (dan dengan demikian sangat sedikit belerang yang dihilangkan dari konsentrat). Ini pada dasarnya adalah proses peleburan. [26] Akibatnya, tungku reverberatory bermuatan basah memiliki lebih sedikit tembaga dalam produk mattenya daripada tungku bermuatan kalsin, dan mereka juga memiliki kehilangan tembaga terhadap terak yang lebih rendah. [27] Gill mengutip tembaga dalam nilai terak 0,23% untuk tungku dengung bermuatan basah vs 0,37% untuk tungku bermuatan kalsin. [27]
Dalam kasus tungku yang diisi kalsin, sebagian besar belerang telah dihilangkan selama tahap pemanggangan, dan kalsin terdiri dari campuran tembaga dan oksida besi dan sulfida. Tungku reverberatory bertindak untuk memungkinkan spesies ini mendekati kesetimbangan kimia pada suhu operasi tungku (sekitar 1600 °C di ujung burner tungku dan sekitar 1200 °C di ujung cerobong; [28] matte sekitar 1100 °C dan terak adalah sekitar 1195 °C [27] ). Dalam proses kesetimbangan ini, oksigen yang terkait dengan senyawa tembaga bertukar dengan belerang yang terkait dengan senyawa besi, meningkatkan kandungan oksida besi dari tungku, dan oksida besi berinteraksi dengan silika dan bahan oksida lainnya untuk membentuk terak. [27]
Reaksi kesetimbangan utama adalah:
- Cu 2O + FeS = Cu 2S + FeO [27]
Terak dan matte membentuk lapisan berbeda yang dapat dikeluarkan dari tungku sebagai aliran terpisah. Lapisan terak secara berkala dibiarkan mengalir melalui lubang di dinding tungku di atas ketinggian lapisan matte. Matte dihilangkan dengan mengalirkannya melalui lubang ke sendok untuk dibawa oleh derek ke konverter. [27] Proses pengeringan ini dikenal sebagai penyadapan tungku. [27] Taphole matte biasanya merupakan lubang melalui blok tembaga berpendingin air yang mencegah erosi batu bata tahan api yang melapisi tungku. Ketika penghapusan matte atau terak selesai, lubang biasanya ditutup dengan tanah liat, yang dihilangkan ketika tungku siap untuk disadap lagi.
Tungku reverberatory sering digunakan untuk mengolah slag konverter cair untuk memulihkan tembaga yang terkandung. [27] Ini akan dituangkan ke dalam tungku dari sendok yang dibawa oleh derek. Namun, terak konverter memiliki magnetit yang tinggi [29] dan beberapa magnetit ini akan mengendap dari terak konverter (karena titik lelehnya yang lebih tinggi), membentuk akresi di perapian tungku reverberatory dan mengharuskan penghentian tungku untuk menghapus akresi. [29] Pembentukan akresi ini membatasi jumlah terak konverter yang dapat diolah dalam tungku reverberatory. [29]
Sementara tungku reverberatory memiliki kehilangan tembaga yang sangat rendah terhadap terak, mereka tidak terlalu hemat energi dan konsentrasi sulfur dioksida yang rendah dalam gas buangnya membuat penangkapannya tidak ekonomis. [8] Akibatnya, operator peleburan menghabiskan banyak uang pada 1970-an dan 1980-an untuk mengembangkan proses peleburan tembaga baru yang lebih efisien. [30] Selain itu, teknologi flash smelting telah dikembangkan di tahun-tahun sebelumnya dan mulai menggantikan tungku reverberatory. Pada tahun 2002, 20 dari 30 tungku reverberatory yang masih beroperasi pada tahun 1994 telah ditutup. [8]
Peleburan tungku flash
Dalam flash smelting, konsentrat didispersikan dalam aliran udara atau oksigen dan reaksi peleburan sebagian besar selesai sementara partikel mineral masih dalam penerbangan. [30] Partikel yang bereaksi kemudian mengendap di bak di bagian bawah tungku, di mana mereka berperilaku seperti halnya kalsin dalam tungku reverberatory. [31] Lapisan terak terbentuk di atas lapisan matte, dan lapisan tersebut dapat disadap secara terpisah dari tungku. [31]
Mengonversi

Tembaga bebas oksigen alias tembaga “Tough-pitch” (sekitar 98% murni), mengandung antimon dan nikel
Matte, yang diproduksi di smelter, mengandung 30–70% tembaga (tergantung pada proses yang digunakan dan filosofi pengoperasian smelter), terutama sebagai tembaga sulfida, serta besi sulfida. Belerang dihilangkan pada suhu tinggi sebagai belerang dioksida dengan meniupkan udara melalui matte cair:
- 2 CuS + 3 O 2 → 2 CuO + 2 SO 2
- CuS + O2 → Cu + 2
Dalam reaksi paralel besi sulfida diubah menjadi terak:
- 2 FeS + 3 O 2 → 2 FeO + 2 SO 2
- 2 FeO + SiO 2 → Fe 2SiO 4
Kemurnian produk ini adalah 98%, dikenal sebagai blister karena permukaan pecah yang disebabkan oleh pelepasan gas belerang dioksida saat babi atau batangan tembaga melepuh didinginkan. Produk sampingan yang dihasilkan dalam proses ini adalah sulfur dioksida dan terak. Sulfur dioksida ditangkap untuk digunakan dalam proses pelindian sebelumnya.
Pemurnian api
Tembaga melepuh dimasukkan ke dalam tungku anoda, tungku yang memurnikan tembaga melepuh menjadi tembaga tingkat anoda dalam dua tahap dengan menghilangkan sebagian besar belerang dan besi yang tersisa, dan kemudian menghilangkan oksigen yang dimasukkan selama tahap pertama. Tahap kedua ini, sering disebut sebagai poling , dilakukan dengan meniupkan gas alam, atau zat pereduksi lainnya, melalui oksida tembaga cair. Ketika nyala api ini menyala hijau, menunjukkan spektrum oksidasi tembaga, sebagian besar oksigen telah terbakar. Ini menciptakan tembaga sekitar 99% murni.
Pemurnian Elektro

Peralatan untuk pemurnian elektrolitik tembaga
Tembaga dimurnikan dengan elektrolisis. Anoda yang dilemparkan dari tembaga melepuh yang diproses ditempatkan ke dalam larutan berair 3–4% tembaga sulfat dan 10–16% asam sulfat. Katoda adalah lembaran tipis yang digulung dari tembaga yang sangat murni atau, yang lebih umum akhir-akhir ini, lembaran awal baja tahan karat yang dapat digunakan kembali (seperti dalam proses IsaKidd). [32] Sebuah potensi hanya 0,2-0,4 volt diperlukan untuk proses untuk memulai. Di pabrik industri, kepadatan arus hingga 420 A/m 2 dimungkinkan. [33] Di anoda, tembaga dan logam kurang mulia larut. Lebih banyak logam mulia seperti perak, emas, selenium, dan telurium mengendap di dasar sel sebagai lendir anoda, yang membentuk produk sampingan yang dapat dijual. Ion tembaga(II) bermigrasi melalui elektrolit ke katoda. Di katoda, pelat logam tembaga keluar, tetapi konstituen yang kurang mulia seperti arsenik dan seng tetap dalam larutan kecuali digunakan tegangan yang lebih tinggi. [34] Reaksinya adalah:
Di anoda: Cu (s) → Cu 2+ (aq) 2e−
Di katoda: Cu 2+ (aq) 2e− → Cu (s)
Pemasaran konsentrat dan tembaga
Konsentrat tembaga yang diproduksi oleh tambang dijual ke pabrik peleburan dan pemurnian yang mengolah bijih dan memurnikan tembaga dan mengenakan biaya untuk layanan ini melalui biaya perawatan (TC) dan biaya pemurnian (RC). Pasar konsentrat tembaga global [35] senilai US$ 81 Miliar pada 2019 dan diproyeksikan mencapai US$ 93 Miliar pada 2027 berkembang pada CAGR 2,5%. TC dikenakan biaya dalam US$ per ton konsentrat yang diolah dan RC dikenai biaya dalam sen per pon yang diolah, dalam mata uang dolar AS, dengan harga patokan yang ditetapkan setiap tahun oleh pabrik peleburan besar Jepang. Pelanggan dalam hal ini dapat berupa smelter, yang menjual ingot tembaga blister ke kilang, atau smelter-pemurni yang terintegrasi secara vertikal.
Salah satu bentuk konsentrat tembaga yang umum mengandung emas dan perak, seperti yang diproduksi oleh Bougainville Copper Limited dari tambang Panguna dari awal 1970-an hingga akhir 1980-an.
Kontrak tipikal untuk penambang didenominasi terhadap harga London Metal Exchange, dikurangi TC-RC dan penalti atau kredit yang berlaku. Hukuman dapat dinilai terhadap konsentrat tembaga sesuai dengan tingkat elemen merusak seperti arsenik, bismut, timbal atau tungsten. Karena sebagian besar badan bijih tembaga sulfida mengandung perak atau emas dalam jumlah yang cukup besar, kredit dapat dibayarkan kepada penambang untuk logam-logam ini jika konsentrasinya dalam konsentrat di atas jumlah tertentu. Biasanya kilang atau pabrik peleburan membebankan biaya kepada penambang berdasarkan konsentrasi; kontrak tipikal akan menentukan bahwa kredit jatuh tempo untuk setiap ons logam dalam konsentrat di atas konsentrasi tertentu; di bawah itu, jika diperoleh kembali, smelter akan menyimpan logam tersebut dan menjualnya untuk membiayai biaya.
Konsentrat tembaga diperdagangkan baik melalui kontrak spot atau kontrak jangka panjang sebagai produk antara dengan sendirinya. Seringkali pabrik peleburan menjual logam tembaga itu sendiri atas nama penambang. Penambang dibayar dengan harga pada saat pelebur-pemurni melakukan penjualan, bukan pada harga pada tanggal penyerahan konsentrat. Di bawah sistem Penetapan Harga Kuota, harga disepakati pada tanggal tetap di masa mendatang, biasanya 90 hari dari waktu pengiriman ke pabrik peleburan.
Katoda tembaga kelas-A terbuat dari 99,99% tembaga dalam lembaran setebal 1 cm, dan kira-kira 1 meter persegi dengan berat kira-kira 200 pon. Ini adalah komoditas sejati, dapat dikirim dan diperdagangkan di bursa logam di New York City (COMEX), London (London Metals Exchange) dan Shanghai (Shanghai Futures Exchange). Seringkali katoda tembaga diperdagangkan di bursa secara tidak langsung melalui waran, opsi, atau kontrak swap sedemikian rupa sehingga mayoritas tembaga diperdagangkan di LME/COMEX/SFE tetapi pengiriman dicapai secara langsung, memindahkan tembaga fisik secara logistik, dan mentransfer lembaran tembaga dari gudang fisik itu sendiri.
Spesifikasi kimia untuk tembaga tingkat elektrolitik adalah ASTM B 115-00 (standar yang menentukan kemurnian dan resistivitas listrik maksimum produk).
Mr. Nick Sun [email protected]
Waktu posting: 27-Sep-2020