¿Qué es la extracción de cobre?
La extracción de cobre se refiere a los métodos utilizados para obtener cobre de sus minerales. La conversión del cobre consiste en una serie de procesos físicos y electroquímicos. Los métodos han evolucionado y varían según el país según la fuente del mineral, las regulaciones ambientales locales y otros factores.
Como en todas las operaciones mineras, el mineral generalmente debe ser beneficiado (concentrado). Las técnicas de procesamiento dependen de la naturaleza del mineral. Si el mineral es principalmente mineral de sulfuro de cobre (como la calcopirita), el mineral se tritura y se muele para liberar los minerales valiosos de los minerales de desecho ("ganga"). Luego se concentra mediante flotación de minerales. El concentrado generalmente se vende luego a fundiciones distantes, aunque algunas minas grandes tienen fundiciones ubicadas cerca. Tal colocación de minas y fundiciones era más típica en el siglo XIX y principios del XX, cuando las fundiciones más pequeñas podían ser económicas. Los concentrados de sulfuro generalmente se funden en hornos como el horno flash Outokumpu o Inco o el horno ISASMELT para producir mata, que debe convertirse y refinarse para producir cobre anódico. Finalmente, el proceso de refinación final es la electrólisis. Por razones económicas y medioambientales, muchos de los subproductos de la extracción se recuperan. El gas de dióxido de azufre, por ejemplo, se captura y se convierte en ácido sulfúrico, que luego puede usarse en el proceso de extracción o venderse para fines tales como la fabricación de fertilizantes.
Los minerales de cobre oxidados se pueden tratar mediante extracción hidrometalúrgica.
Historia

Mineros en la mina Tamarack en Copper Country, en 1905
La evidencia más temprana de martillado en frío de cobre nativo proviene de la excavación en Çayönü Tepesi en el este de Anatolia, que data entre 7200 y 6600 a. [1] Entre los diversos artículos considerados votivos o amuletos había uno que parecía un anzuelo y otro como un punzón. Otro hallazgo, en la cueva de Shanidar en Mergasur, Irak, contenía cuentas de cobre, data del 8700 a. [2]
Una de las minas de cobre conocidas más antiguas del mundo, a diferencia del uso de depósitos de superficie, se encuentra en Timna Valley, Israel, desde el cuarto milenio antes de Cristo, con uso de depósitos de superficie desde el sexto al quinto milenio. [3] [4]
El sitio arqueológico de Pločnik en el sureste de Europa (Serbia) contiene la evidencia [ dudosa – discutir ] más antigua con fecha segura de fabricación de cobre a alta temperatura, desde el año 5000 a. El hallazgo de junio de 2010 amplía 500 años más el registro anterior de fundición de cobre de Rudna Glava (Serbia), que data del quinto milenio a. [5]
La tecnología de fundición de cobre dio lugar a la Edad del Cobre, también conocida como Edad Calcolítica, y luego a la Edad del Bronce. La Edad del Bronce no habría sido posible sin que los humanos desarrollaran tecnología de fundición.
Concentración
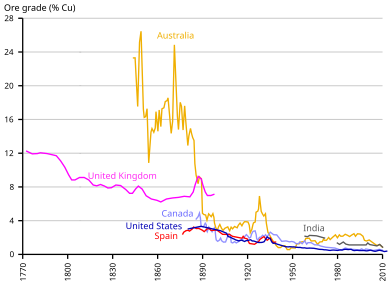
La concentración decreciente de cobre en los minerales ahora requiere un pretratamiento de los minerales.
La mayoría de los minerales de cobre contienen solo un pequeño porcentaje de metal de cobre ligado a minerales valiosos, y el resto del mineral es roca o gangueminerales no deseados, típicamente minerales de silicato o minerales de óxido para los que a menudo no hay valor. En algunos casos, los relaves se han retirado para recuperar el valor perdido a medida que ha mejorado la tecnología para recuperar cobre. La ley promedio de los minerales de cobre en el siglo XXI es inferior al 0,6 % de cobre, con una proporción de minerales económicos (incluido el cobre) inferior al 2 % del volumen total de la roca mineral. Un objetivo clave en el tratamiento metalúrgico de cualquier mineral es la separación de los minerales de los minerales de ganga dentro de la roca.
La primera etapa de cualquier proceso dentro de un circuito de tratamiento metalúrgico es la trituración o trituración precisa , donde la roca se tritura para producir partículas pequeñas (<100 μm) que consisten en fases minerales individuales. Luego, estas partículas se separan para eliminar la ganga (residuos de rocas), seguido de un proceso de liberación física de los minerales de la roca. El proceso de liberación de los minerales de cobre depende de si son minerales de óxido o de sulfuro. [6]
Los pasos subsiguientes dependen de la naturaleza del mineral que contiene el cobre y de lo que se extraerá. Para los minerales oxidados, normalmente se lleva a cabo un proceso de liberación hidrometalúrgica, que utiliza la naturaleza soluble de los minerales de la mena en beneficio de la planta de tratamiento metalúrgico. Para minerales de sulfuro, tanto secundarios (supergénicos) como primarios (hipógenos), la flotación por espuma se utiliza para separar físicamente el mineral de la ganga. Para yacimientos especiales que contengan cobre nativo o secciones de yacimientos ricos en cobre nativo supergénico, este mineral puede recuperarse mediante un circuito de gravedad simple.
Flotación por espuma

Celdas de flotación de espuma para concentrar minerales de sulfuro de cobre y níquel, Falconbridge, Ontario.
El proceso moderno de flotación por espuma fue inventado de forma independiente a principios del siglo XX en Australia por CV Potter y casi al mismo tiempo por GD Delprat. [7]

Burbujas de aire cargadas de sulfuro de cobre en una celda Jameson en la planta de flotación de Prominent Hillmine en Australia del Sur
Todos los minerales de sulfuros primarios de sulfuros de cobre y la mayoría de los concentrados de sulfuros de cobre secundarios (como la calcocita) se someten a fundición. Existen algunos procesos de lixiviación en cuba o lixiviación a presión para solubilizar concentrados de calcocita y producir cátodos de cobre a partir de la solución de lixiviado resultante, pero esta es una parte menor del mercado.
Los concentrados de carbonato son un producto relativamente menor que se produce en las plantas de cementación de cobre, generalmente como la etapa final de una operación de lixiviación en pilas. Dichos concentrados de carbonato pueden tratarse mediante una planta de extracción por solvente y electroobtención (SX-EW) o fundirse.
El mineral de cobre se tritura y muele hasta un tamaño tal que se ha producido un grado aceptablemente alto de liberación entre los minerales de sulfuro de cobre y los minerales de ganga. Luego, el mineral se humedece, se suspende en una lechada y se mezcla con xantatos u otros reactivos, lo que hace que las partículas de sulfuro sean hidrofóbicas. Los reactivos típicos incluyen etilxantato de potasio y etilxantato de sodio, pero también se usan ditiofosfatos y ditiocarbamatos.
El mineral tratado se introduce en un tanque de aireación lleno de agua que contiene un tensioactivo como metilisobutilcarbinol (MIBC). El aire se fuerza constantemente a través de la suspensión y las burbujas de aire se adhieren a las partículas de sulfuro de cobre hidrofóbico, que son conducidas a la superficie, donde forman una espuma y se eliminan. Estos desnatados generalmente se someten a una celda limpiadora-depuradora para eliminar el exceso de silicatos y eliminar otros minerales de sulfuro que pueden afectar negativamente la calidad del concentrado (típicamente, galena) y el concentrado final enviado para su fundición. La roca que no ha flotado en la celda de flotación se desecha como relave o se procesa más para extraer otros metales como plomo (de la galena) y zinc (de la esfalerita), en caso de que existan. Para mejorar la eficiencia del proceso, se utiliza cal para elevar el pH del baño de agua, haciendo que el colector se ionice más y se una preferentemente a la calcopirita (CuFeS 2) y evite la pirita (FeS 2). El hierro existe en ambos minerales de la zona primaria. Los minerales de cobre que contienen calcopirita se pueden concentrar para producir un concentrado con entre 20% y 30% de cobre en concentrado (generalmente 27-29% de cobre); el resto del concentrado es hierro y azufre en la calcopirita e impurezas no deseadas como minerales de ganga de silicato u otros minerales de sulfuro, típicamente cantidades menores de pirita, esfalerita o galena. Los concentrados de chalcocita suelen clasificar entre un 37 % y un 40 % de cobre en el concentrado, ya que la chalcocita no contiene hierro dentro del mineral.
Extracción hidrometalúrgica
minerales de sulfuro
Los sulfuros secundarios, los formados por el enriquecimiento secundario supergénico, son resistentes ( refractarios ) a la lixiviación sulfúrica. Estos minerales son una mezcla de minerales de carbonato, sulfato, fosfato y óxido de cobre y minerales de sulfuro secundario, predominantemente calcocita, pero otros minerales como la digenita pueden ser importantes en algunos depósitos.
Los minerales supergénicos ricos en sulfuros se pueden concentrar mediante flotación por espuma. Un concentrado típico de calcocita puede clasificar entre un 37 % y un 40 % de cobre en sulfuro, lo que los hace relativamente baratos de fundir en comparación con los concentrados de calcopirita.
Algunos depósitos de sulfuros supergénicos se pueden lixiviar mediante un proceso de lixiviación en pilas de oxidación bacteriana para oxidar los sulfuros a ácido sulfúrico, lo que también permite la lixiviación simultánea con ácido sulfúrico para producir una solución de sulfato de cobre. Al igual que con los minerales de óxido, se utilizan tecnologías de extracción por solvente y electroobtención para recuperar el cobre de la solución de lixiviación cargada.
Los minerales de sulfuro supergénico ricos en minerales de cobre nativo son refractarios al tratamiento con lixiviación con ácido sulfúrico en todas las escalas de tiempo practicables, y las partículas metálicas densas no reaccionan con los medios de flotación de espuma. Por lo general, si el cobre nativo es una parte menor de un perfil supergénico, no se recuperará y se reportará a los relaves. Cuando son lo suficientemente ricos, los yacimientos de cobre nativo pueden tratarse para recuperar el cobre contenido a través de un circuito de separación por gravedad en el que se utiliza la densidad del metal para liberarlo de los minerales de silicato más livianos. A menudo, la naturaleza de la ganga es importante, ya que los minerales de cobre nativo ricos en arcilla resultan difíciles de liberar.
Minerales de óxido
Los cuerpos de mineral de cobre oxidado pueden tratarse a través de varios procesos, con procesos hidrometalúrgicos utilizados para tratar minerales de óxido dominados por minerales de carbonato de cobre como azurita y malaquita, y otros minerales solubles como silicatos como crisocola o sulfatos como atacamita, etc.
Dichos minerales de óxido generalmente se lixivian con ácido sulfúrico, generalmente en un proceso de lixiviación en pilas o lixiviación en volcado para liberar los minerales de cobre en una solución de ácido sulfúrico cargado con sulfato de cobre en solución. La solución de sulfato de cobre (la solución de lixiviación preñada) luego se despoja de cobre a través de una planta de extracción por solventes y electroobtención (SX-EW), con el ácido sulfúrico en barra (desnudado) reciclado nuevamente a las pilas. Alternativamente, el cobre se puede precipitar fuera de la solución cargada poniéndolo en contacto con chatarra; un proceso llamado cementación. El cobre de cemento es normalmente menos puro que el cobre SX-EW. Comúnmente, el ácido sulfúrico se usa como lixiviante para el óxido de cobre, aunque es posible usar agua, particularmente para minerales ricos en minerales de sulfato ultrasolubles. [ cita requerida ]
En general, la flotación por espuma no se usa para concentrar minerales de óxido de cobre, ya que los minerales de óxido no responden a los productos químicos o al proceso de flotación por espuma (es decir, no se unen a los productos químicos a base de queroseno). Ocasionalmente, los minerales de óxido de cobre se han tratado mediante flotación por espuma mediante la sulfuración de los minerales de óxido con ciertos productos químicos que reaccionan con las partículas del mineral de óxido para producir una fina capa de sulfuro (generalmente calcocita), que luego puede activarse en la planta de flotación por espuma.
fundición de sulfuro
Hasta la segunda mitad del siglo XX, la fundición de minerales de sulfuro era casi el único medio para producir cobre metálico a partir de minerales extraídos ( producción primaria de cobre). Davenport, et al., señalaron en 2002 que, incluso entonces, el 80 % de la producción mundial de cobre primario procedía de minerales de cobre, hierro y azufre, y que la gran mayoría de estos se trataba mediante fundición.
El cobre se recuperó inicialmente de minerales de sulfuro fundiendo directamente el mineral en un horno. [9] Las fundiciones se ubicaron inicialmente cerca de las minas para minimizar el costo de transporte. Esto evitó los costos prohibitivos de transportar los minerales de desecho y el azufre y el hierro presentes en los minerales que contienen cobre. Sin embargo, a medida que disminuía la concentración de cobre en los cuerpos minerales, los costos de energía para fundir todo el mineral también se volvieron prohibitivos y se hizo necesario concentrar los minerales primero.
Las técnicas de concentración iniciales incluían la clasificación manual [10] y la concentración por gravedad. Resultaron en altas pérdidas de cobre. En consecuencia, el desarrollo del proceso de flotación por espuma fue un gran paso adelante en el procesamiento de minerales. [11] Hizo posible el desarrollo de la mina gigante Bingham Canyon en Utah. [12]
En el siglo XX, la mayoría de los minerales se concentraban antes de la fundición. La fundición se llevó a cabo inicialmente utilizando plantas de sinterización y altos hornos, [13] o con tostadores y hornos de reverbero. [14] La tostación y la fundición en hornos de reverbero dominaron la producción de cobre primario hasta la década de 1960. [8]
Asado
El proceso de tostado se realiza generalmente en combinación con hornos de reverbero. En el tostador, el concentrado de cobre se oxida parcialmente para producir gas “calcinado” y dióxido de azufre. La estequiometría de la reacción que ocurre es:
- 2 CuFeS 2 + 3 O 2 → 2 FeO + 2 CuS + 2 SO 2
El tostado generalmente deja más azufre en el producto calcinado (15 % en el caso del tostador en Mount Isa Mines [15] ) que lo que deja una planta de sinterización en el producto sinterizado (alrededor del 7 % en el caso de la fundición de Refinación y Fundición Electrolítica [ 16] ).
A partir de 2005, la tostación ya no es común en el tratamiento de concentrados de cobre, porque su combinación con hornos de reverbero no es energéticamente eficiente y la concentración de SO 2 en el gas de escape de la tostación es demasiado diluida para una captura rentable. [8] Ahora se prefiere la fundición directa, por ejemplo, utilizando las siguientes tecnologías de fundición: fundición flash, hornos Isasmelt, Noranda, Mitsubishi o El Teniente. [8]
Fundición

Sustitución de fundición en horno de reverbero por fundición flash, en relación con el número de fundiciones de cobre que utilizan esta tecnología.
La fusión inicial del material a fundir se suele denominar etapa de fundición o fundición de la mata . Puede llevarse a cabo en una variedad de hornos, incluidos los altos hornos y los hornos de reverbero, en gran parte obsoletos, así como los hornos flash, los hornos Isasmelt, etc. [8] El producto de esta etapa de fundición es una mezcla de cobre, hierro y azufre que está enriquecido en cobre, y que recibe el nombre de mata o fundición de la mata de cobre.[8] El término grado de la mata se usa normalmente para referirse al contenido de cobre de la mata. [17]
El propósito de la etapa de fundición de la mata es eliminar la mayor cantidad posible de minerales de hierro, azufre y ganga no deseados (como sílice, magnesia, alúmina y piedra caliza), mientras se minimiza la pérdida de cobre. [17] Esto se logra haciendo reaccionar sulfuros de hierro con oxígeno (en aire o aire enriquecido con oxígeno) para producir óxidos de hierro (principalmente como FeO, pero con algo de magnetita (Fe 3O 4)) y dióxido de azufre. [17]
El sulfuro de cobre y el óxido de hierro se pueden mezclar, pero cuando se agrega suficiente sílice, se forma una capa de escoria separada. [18] La adición de sílice también reduce el punto de fusión (o, más correctamente, la temperatura de liquidus) de la escoria, lo que significa que el proceso de fundición se puede operar a una temperatura más baja. [18]
La reacción de formación de escoria es:
- FeO + SiO 2 → FeO.SiO 2[17]
La escoria es menos densa que la mata, por lo que forma una capa que flota sobre la mata. [19]
El cobre se puede perder de la mata de tres maneras: como óxido cuproso (Cu 2O) disuelto en la escoria, [20] como sulfuro de cobre disuelto en la escoria [21] o como pequeñas gotas (o gránulos ) de mata suspendida en la escoria. [22] [23]
La cantidad de cobre perdido como óxido de cobre aumenta a medida que aumenta el potencial de oxígeno de la escoria. [23] El potencial de oxígeno generalmente aumenta a medida que aumenta el contenido de cobre de la mata. [24] Así, la pérdida de cobre como óxido aumenta a medida que aumenta el contenido de cobre de la mata. [25]
Por otro lado, la solubilidad del cobre sulfurado en la escoria disminuye a medida que el contenido de cobre de la mata aumenta más allá del 40%. [21] Nagamori calculó que más de la mitad del cobre disuelto en escorias de matas que contienen menos del 50% de cobre es cobre sulfuroso. Por encima de esta cifra, el cobre oxídico comienza a dominar. [21]
La pérdida de cobre en forma de gránulos suspendidos en la escoria depende del tamaño de los gránulos, la viscosidad de la escoria y el tiempo de sedimentación disponible. [26] Rosenqvist sugirió que aproximadamente la mitad de las pérdidas de cobre a la escoria se debieron a gránulos suspendidos. [26]
La masa de escoria generada en la etapa de fundición depende del contenido de hierro del material alimentado al horno de fundición y del grado objetivo de la mata. Cuanto mayor sea el contenido de hierro de la alimentación, más hierro deberá rechazarse a la escoria para un grado de mata determinado. De manera similar, aumentar el grado objetivo de la mata requiere el rechazo de más hierro y un aumento en el volumen de escoria.
Así, los dos factores que más inciden en la pérdida de cobre por escorias en la etapa de fundición son:
- grado de la mata
- masa de escoria. [18]
Esto significa que existe un límite práctico sobre qué tan alto puede ser el grado de la mata si se quiere minimizar la pérdida de cobre a la escoria. Por lo tanto, se requieren etapas adicionales de procesamiento (conversión y refinado al fuego).
Las siguientes subsecciones describen brevemente algunos de los procesos utilizados en la fundición de mata.
Fundición en horno de reverbero
Los hornos de reverbero son hornos largos que pueden tratar concentrados húmedos, secos o tostados. [8] La mayoría de los hornos de reverbero utilizados en los últimos años trataban concentrado tostado porque poner materias primas secas en el horno de reverbero es más eficiente desde el punto de vista energético y porque la eliminación de parte del azufre en el tostador da como resultado una mayor calidad de la mata. [8]
La alimentación del horno de reverbero se añade al horno a través de orificios de alimentación a lo largo de los lados del horno. [8] Normalmente se agrega sílice adicional para ayudar a formar la escoria. El horno se alimenta con quemadores de carbón pulverizado, fuel oil o gas natural [27] y se funde la carga sólida.
Los hornos de reverbero también pueden alimentarse con escoria fundida de la etapa de conversión posterior para recuperar el cobre contenido y otros materiales con un alto contenido de cobre. [27]
Debido a que el baño del horno de reverbero está inactivo, se produce muy poca oxidación de la alimentación (y, por lo tanto, se elimina muy poco azufre del concentrado). Es esencialmente un proceso de fusión. [26] En consecuencia, los hornos de reverbero de carga húmeda tienen menos cobre en su producto mate que los hornos de calcina, y también tienen menores pérdidas de cobre a la escoria. [27] Gill cita un valor de cobre en escoria del 0,23 % para un horno de reverbero de carga húmeda frente al 0,37 % para un horno de calcina. [27]
En el caso de los hornos cargados con calcina, una parte importante del azufre ha sido eliminada durante la etapa de tostado, y la calcina consiste en una mezcla de óxidos y sulfuros de cobre y hierro. El horno de reverbero actúa para permitir que estas especies se acerquen al equilibrio químico a la temperatura de funcionamiento del horno (aproximadamente 1600 °C en el extremo del quemador del horno y aproximadamente 1200 °C en el extremo de la chimenea; [28] la mata está a aproximadamente 1100 °C y la escoria está a unos 1195 °C [27] ). En este proceso de equilibrio, el oxígeno asociado con los compuestos de cobre se intercambia con el azufre asociado con los compuestos de hierro, aumentando el contenido de óxido de hierro del horno, y los óxidos de hierro interactúan con la sílice y otros materiales de óxido para formar la escoria. [27]
La principal reacción de equilibrio es:
- cobre2FeS = Cu2S 2FeO [27]
La escoria y la mata forman capas distintas que pueden retirarse del horno como corrientes separadas. La capa de escoria se deja fluir periódicamente a través de un agujero en la pared del horno por encima de la altura de la capa de mata. La mata se extrae escurriéndola por un orificio en cucharones para que sea transportada por grúa a los convertidores. [27] Este proceso de drenaje se conoce como tocar el horno. [27] El grifo mate es normalmente un agujero a través de un bloque de cobre enfriado por agua que evita la erosión de los ladrillos refractarios que recubren el horno. Cuando se completa la remoción de la mata o escoria, normalmente se tapa el orificio con arcilla, que se retira cuando el horno está listo para ser colado nuevamente.
Los hornos de reverbero se usaban a menudo para tratar la escoria fundida del convertidor para recuperar el cobre contenido. [27] Esto se vertía en los hornos desde cucharones transportados por grúas. Sin embargo, la escoria del convertidor tiene un alto contenido de magnetita [29] y parte de esta magnetita se precipitaría de la escoria del convertidor (debido a su punto de fusión más alto), formando una acumulación en la solera del horno de reverbero y necesitando apagar el horno para eliminar la acumulación. [29] Esta formación de acreción limita la cantidad de escoria de conversión que se puede tratar en un horno de reverbero. [29]
Si bien los hornos de reverbero tienen pérdidas de cobre muy bajas a la escoria, no son muy eficientes energéticamente y las bajas concentraciones de dióxido de azufre en sus gases de escape hacen que su captura no sea rentable. [8] En consecuencia, los operadores de fundición dedicaron una gran cantidad de dinero en las décadas de 1970 y 1980 al desarrollo de procesos de fundición de cobre nuevos y más eficientes. [30] Además, las tecnologías de fundición instantánea se habían desarrollado en años anteriores y comenzaron a reemplazar los hornos de reverbero. En 2002, 20 de los 30 hornos de reverbero que seguían en funcionamiento en 1994 se habían cerrado. [8]
Fundición en horno flash
En la fundición instantánea, el concentrado se dispersa en una corriente de aire u oxígeno y las reacciones de fundición se completan en gran medida mientras las partículas minerales aún están en vuelo. [30] Las partículas reaccionadas luego se asientan en un baño en el fondo del horno, donde se comportan como lo hace la calcina en un horno de reverbero. [31] Se forma una capa de escoria encima de la capa de mate, y se pueden extraer del horno por separado. [31]
Mudado

Cobre libre de oxígeno, también conocido como cobre "Tough-pitch" (aprox. 98 % de pureza), que contiene antimonio y níquel
La mata, que se produce en la fundición, contiene entre un 30 % y un 70 % de cobre (según el proceso utilizado y la filosofía operativa de la fundición), principalmente como sulfuro de cobre y sulfuro de hierro. El azufre se elimina a alta temperatura como dióxido de azufre soplando aire a través de la mata fundida:
- 2 Cu S + 3 O 2 → 2 Cu O + 2 SO 2
- CuS + O 2 → Cu + SO 2
En una reacción paralela, el sulfuro de hierro se convierte en escoria:
- 2 FeS + 3 O 2 → 2 FeO + 2 SO 2
- 2 FeO + SiO 2 → Fe 2SiO 4
La pureza de este producto es del 98%, se le conoce como ampolla debido a la superficie rota creada por el escape de gas de dióxido de azufre a medida que se enfrían los cerdos o lingotes de cobre de la ampolla. Los subproductos generados en el proceso son dióxido de azufre y escoria. El dióxido de azufre se captura para su uso en procesos de lixiviación anteriores.
Refinación de fuego
El cobre ampolloso se coloca en un horno de ánodo, un horno que refina el cobre ampolloso a cobre de calidad anódica en dos etapas al eliminar la mayor parte del azufre y el hierro restantes, y luego eliminar el oxígeno introducido durante la primera etapa. Esta segunda etapa, a menudo denominada polarización , se realiza inyectando gas natural, o algún otro agente reductor, a través del óxido de cobre fundido. Cuando esta llama se vuelve verde, lo que indica el espectro de oxidación del cobre, la mayor parte del oxígeno se ha quemado. Esto crea cobre con una pureza de aproximadamente el 99%.
Electrorefinación

Aparatos para el refinado electrolítico de cobre.
El cobre se refina por electrólisis. Los ánodos fundidos a partir de cobre ampolloso procesado se colocan en una solución acuosa de sulfato de cobre al 3-4 % y ácido sulfúrico al 10-16 %. Los cátodos son láminas delgadas laminadas de cobre de alta pureza o, más comúnmente en la actualidad, láminas iniciales de acero inoxidable reutilizables (como en el proceso IsaKidd). [32] Se requiere un potencial de solo 0,2 a 0,4 voltios para que comience el proceso. En plantas industriales son posibles densidades de corriente de hasta 420 A/m 2 . [33] En el ánodo se disuelven el cobre y los metales menos nobles. Los metales más nobles como la plata, el oro, el selenio y el telurio se asientan en el fondo de la celda como limo anódico, que forma un subproducto vendible. Los iones de cobre (II) migran a través del electrolito hacia el cátodo. En el cátodo, el metal de cobre sale, pero los componentes menos nobles, como el arsénico y el zinc, permanecen en solución a menos que se use un voltaje más alto. [34] Las reacciones son:
En el ánodo: Cu (s) → Cu 2+ (aq) + 2e −
En el cátodo: Cu 2+ (aq) + 2e − → Cu (s)
Comercialización de concentrados y cobre
Los concentrados de cobre producidos por las minas se venden a fundiciones y refinerías que tratan el mineral y refinan el cobre y cobran por este servicio a través de cargos por tratamiento (TC) y cargos por refinación (RC). El mercado mundial de concentrados de cobre [35] se valoró en US$ 81 mil millones en 2019 y se proyecta que alcance los US$ 93 mil millones para 2027, expandiéndose a una CAGR del 2,5 %. Los TC se cobran en dólares estadounidenses por tonelada de concentrado tratado y los RC se cobran en centavos por libra tratada, denominados en dólares estadounidenses, con precios de referencia establecidos anualmente por las principales fundiciones japonesas. El cliente en este caso puede ser una fundición, que vende lingotes de cobre blister a una refinería, o una fundición-refinadora integrada verticalmente.
Una forma predominante de concentrado de cobre contiene oro y plata, como la que produce Bougainville Copper Limited en la mina Panguna desde principios de la década de 1970 hasta finales de la década de 1980.
El contrato típico para un minero está denominado en función del precio de la Bolsa de Metales de Londres, menos los TC-RC y cualquier penalización o crédito aplicable. Se pueden imponer sanciones a los concentrados de cobre de acuerdo con el nivel de elementos nocivos como arsénico, bismuto, plomo o tungsteno. Debido a que una gran parte de los yacimientos de sulfuro de cobre contienen plata u oro en cantidades apreciables, se puede pagar un crédito al minero por estos metales si su concentración dentro del concentrado supera cierta cantidad. Por lo general, la refinería o fundición cobra al minero una tarifa basada en la concentración; un contrato típico especificará que se debe un crédito por cada onza del metal en el concentrado por encima de cierta concentración; por debajo de eso, si se recupera, la fundición se quedará con el metal y lo venderá para sufragar los costos.
El concentrado de cobre se comercializa ya sea a través de contratos al contado o bajo contratos a largo plazo como un producto intermedio por derecho propio. A menudo, la fundición vende el metal de cobre en nombre del minero. Al minero se le paga el precio en el momento en que la fundición-refinadora realiza la venta, no el precio en la fecha de entrega del concentrado. Bajo un sistema de cotización de precios, se acuerda que el precio sea en una fecha fija en el futuro, generalmente 90 días desde el momento de la entrega a la fundición.
El cátodo de cobre de grado A es de 99,99% de cobre en láminas de 1 cm de espesor y aproximadamente 1 metro cuadrado con un peso aproximado de 200 libras. Es una verdadera mercancía, que se puede entregar y comercializar en las bolsas de metales de la ciudad de Nueva York (COMEX), Londres (London Metals Exchange) y Shanghái (Shanghai Futures Exchange). A menudo, el cátodo de cobre se negocia en las bolsas indirectamente a través de garantías, opciones o contratos de intercambio, de modo que la mayoría del cobre se negocia en la LME/COMEX/SFE, pero la entrega se logra directamente, moviendo logísticamente el cobre físico y transfiriendo la hoja de cobre de los propios almacenes físicos.
La especificación química para el cobre de grado electrolítico es la norma ASTM B 115-00 (una norma que especifica la pureza y la resistividad eléctrica máxima del producto).
Mr. Nick Sun [email protected]
Hora de publicación: 27-sep-2020