Was ist Kupferextraktion?
Die Kupfergewinnung bezieht sich auf die Methoden, mit denen Kupfer aus seinen Erzen gewonnen wird. Die Umwandlung von Kupfer besteht aus einer Reihe von physikalischen und elektrochemischen Prozessen. Die Methoden haben sich weiterentwickelt und variieren von Land zu Land, abhängig von der Erzquelle, den örtlichen Umweltvorschriften und anderen Faktoren.
Wie bei allen Bergbaubetrieben muss das Erz normalerweise aufbereitet (konzentriert) werden. Die Verarbeitungstechniken hängen von der Art des Erzes ab. Wenn es sich bei dem Erz hauptsächlich um Sulfid-Kupfer-Mineralien (wie Chalkopyrit) handelt, wird das Erz zerkleinert und gemahlen, um die wertvollen Mineralien aus den Abfallmineralien ('Gangart') freizusetzen. Anschließend wird es mittels Mineralflotation aufkonzentriert. Das Konzentrat wird dann in der Regel an entfernte Hütten verkauft, obwohl einige große Minen Hütten in der Nähe haben. Eine solche Anordnung von Bergwerken und Schmelzhütten war eher im 19. und frühen 20. Jahrhundert üblich, als kleinere Schmelzhütten wirtschaftlich sein konnten. Die Sulfidkonzentrate werden typischerweise in solchen Öfen wie dem Schnellofen von Outokumpu oder Inco oder dem ISASMELT-Ofen geschmolzen, um Rohstein zu erzeugen, der umgewandelt und raffiniert werden muss, um Anodenkupfer herzustellen. Schließlich ist der letzte Raffinationsprozess die Elektrolyse. Aus wirtschaftlichen und ökologischen Gründen werden viele Nebenprodukte der Extraktion zurückgewonnen. Schwefeldioxidgas wird beispielsweise aufgefangen und in Schwefelsäure umgewandelt – die dann im Extraktionsprozess verwendet oder für Zwecke wie die Düngemittelherstellung verkauft werden kann.
Oxidierte Kupfererze können durch hydrometallurgische Extraktion behandelt werden.
Geschichte

Bergleute in der Tamarack-Mine im Copper Country, 1905
Der früheste Beweis für das Kalthämmern von einheimischem Kupfer stammt aus der Ausgrabung bei Çayönü Tepesi in Ostanatolien, die zwischen 7200 und 6600 v. Chr. Datiert wird. [1] Unter den verschiedenen Gegenständen, die als Votive oder Amulette angesehen wurden, gab es einen, der wie ein Angelhaken und einer wie eine Ahle aussah. Ein weiterer Fund in der Shanidar-Höhle in Mergasur, Irak, enthielt Kupferperlen und stammt aus dem Jahr 8.700 v. [2]
Eine der ältesten bekannten Kupferminen der Welt, im Gegensatz zur Nutzung von Oberflächenvorkommen, befindet sich seit dem vierten Jahrtausend v. Chr. Im Timna-Tal, Israel, mit einer Nutzung von Oberflächenvorkommen seit dem sechsten bis fünften Jahrtausend. [3] [4]
Die archäologische Stätte Pločnik in Südosteuropa (Serbien) enthält die ältesten sicher datierten [ zweifelhaften – diskutieren ] Beweise für die Kupferherstellung bei hohen Temperaturen aus dem Jahr 5.000 v. Der Fund im Juni 2010 erweitert die frühere Aufzeichnung der Kupferschmelze von Rudna Glava (Serbien) um weitere 500 Jahre, datiert auf das 5. Jahrtausend v. Chr. [5]
Die Kupferschmelztechnologie führte zur Kupferzeit, auch Chalkolithikum genannt, und dann zur Bronzezeit. Die Bronzezeit wäre ohne die Entwicklung der Schmelztechnologie durch den Menschen nicht möglich gewesen.
Konzentration
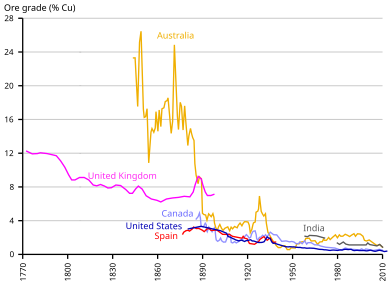
Die abnehmende Konzentration von Kupfer in Erzen erfordert nun eine Vorbehandlung der Erze.
Die meisten Kupfererze enthalten nur einen kleinen Prozentsatz an Kupfermetall, das in wertvollen Erzmineralien gebunden ist, wobei der Rest des Erzes unerwünschte Gesteins- oder Gangminerale sind, typischerweise Silikatminerale oder Oxidmineralien, für die es oft keinen Wert gibt. In einigen Fällen wurden Rückstände zurückgezogen, um den verlorenen Wert zurückzugewinnen, da sich die Technologie zur Rückgewinnung von Kupfer verbessert hat. Der durchschnittliche Gehalt an Kupfererzen im 21. Jahrhundert liegt unter 0,6 % Kupfer, wobei der Anteil an wirtschaftlichen Erzmineralien (einschließlich Kupfer) weniger als 2 % des Gesamtvolumens des Erzgesteins ausmacht. Ein Hauptziel bei der metallurgischen Behandlung von Erzen ist die Trennung von Erzmineralien von Gangmineralien innerhalb des Gesteins.
Die erste Stufe eines jeden Prozesses innerhalb eines metallurgischen Behandlungskreislaufs ist das genaue Mahlen oder Zerkleinern , bei dem das Gestein zerkleinert wird, um kleine Partikel (<100 μm) zu erzeugen, die aus einzelnen Mineralphasen bestehen. Diese Partikel werden dann getrennt, um Gangart (Gesteinsrückstände) zu entfernen, danach folgt ein Prozess der physikalischen Befreiung der Erzminerale aus dem Gestein. Der Prozess der Freisetzung von Kupfererzen hängt davon ab, ob es sich um Oxid- oder Sulfiderze handelt. [6]
Die nachfolgenden Schritte hängen von der Art des Erzes ab, das das Kupfer enthält, und davon, was extrahiert werden soll. Für oxidische Erze wird normalerweise ein hydrometallurgischer Freisetzungsprozess durchgeführt, der die Löslichkeit der Erzminerale zum Vorteil der metallurgischen Aufbereitungsanlage nutzt. Für Sulfiderze, sowohl sekundäre (supergene) als auch primäre (hypogene), wird die Schaumflotation verwendet, um das Erz physikalisch von der Gangart zu trennen. Bei speziellen Erzkörpern, die natives Kupfer enthalten, oder Abschnitten von Erzkörpern, die reich an supergenem nativem Kupfer sind, kann dieses Mineral durch einen einfachen Gravitationskreislauf gewonnen werden.
Schaumflotation

Schaumflotationszellen zur Konzentration von Kupfer- und Nickelsulfidmineralien, Falconbridge, Ontario.
Das moderne Schaumflotationsverfahren wurde Anfang des 20. Jahrhunderts in Australien von CV Potter und etwa zur gleichen Zeit von GD Delprat unabhängig voneinander erfunden. [7]

Mit Kupfersulfid beladene Luftblasen auf einer Jameson-Zelle in der Flotationsanlage der Prominent Hillmine in Südaustralien
Alle primären Sulfiderze von Kupfersulfiden und die meisten Konzentrate von sekundären Kupfersulfiden (Chalkozit) werden einer Verhüttung unterzogen. Es gibt einige Bottichlaugungs- oder Drucklaugungsverfahren, um Chalkosinkonzentrate zu solubilisieren und Kupferkathoden aus der resultierenden Laugungslösung herzustellen, aber dies ist ein kleiner Teil des Marktes.
Karbonatkonzentrate sind ein relativ unbedeutendes Produkt, das in Kupferzementanlagen produziert wird, typischerweise als Endstufe eines Haufenlaugungsverfahrens. Solche Carbonatkonzentrate können durch eine Lösungsmittelextraktions- und Elektrogewinnungsanlage (SX-EW) behandelt oder geschmolzen werden.
Das Kupfererz wird zerkleinert und auf eine solche Größe gemahlen, dass zwischen den Kupfersulfid-Erzmineralien und den Gangmineralien ein annehmbar hoher Freisetzungsgrad aufgetreten ist. Das Erz wird dann benetzt, in einer Aufschlämmung suspendiert und mit Xanthogenaten oder anderen Reagenzien gemischt, die die Sulfidpartikel hydrophob machen. Typische Reagenzien umfassen Kaliumethylxanthat und Natriumethylxanthat, aber auch Dithiophosphate und Dithiocarbamate werden verwendet.
Das behandelte Erz wird in einen mit Wasser gefüllten Belüftungstank eingeführt, der Tenside wie Methylisobutylcarbinol (MIBC) enthält. Ständig wird Luft durch die Aufschlämmung gepresst und die Luftbläschen lagern sich an den hydrophoben Kupfersulfidpartikeln an, die an die Oberfläche geleitet werden, wo sie aufschäumen und abgeschöpft werden. Diese Abschöpfungen werden im Allgemeinen einer Reiniger-Scavenger-Zelle unterzogen, um überschüssige Silikate und andere Sulfidmineralien zu entfernen, die die Konzentratqualität (typischerweise Bleiglanz) nachteilig beeinflussen können, und das endgültige Konzentrat zum Schmelzen geschickt. Das in der Flotationszelle nicht abgeschwemmte Gestein wird entweder als Tailings entsorgt oder weiterverarbeitet, um andere Metalle wie Blei (aus Bleiglanz) und Zink (aus Sphalerit) zu extrahieren, falls vorhanden. Um die Prozesseffizienz zu verbessern, wird Kalk verwendet, um den pH-Wert des Wasserbades zu erhöhen, was bewirkt, dass der Kollektor stärker ionisiert und bevorzugt an Chalkopyrit (CuFeS 2) bindet und Pyrit (FeS 2) vermeidet. Eisen kommt in beiden Primärzonenmineralien vor. Kupfererze, die Chalkopyrit enthalten, können konzentriert werden, um ein Konzentrat mit zwischen 20 % und 30 % Kupfer-in-Konzentrat (normalerweise 27–29 % Kupfer) herzustellen; der Rest des Konzentrats sind Eisen und Schwefel im Chalkopyrit und unerwünschte Verunreinigungen wie Gangart-Silikatmineralien oder andere Sulfidmineralien, typischerweise geringe Mengen an Pyrit, Sphalerit oder Bleiglanz. Chalcocit-Konzentrate enthalten typischerweise zwischen 37 % und 40 % Kupfer im Konzentrat, da Chalcocit kein Eisen im Mineral enthält.
Hydrometallurgische Gewinnung
Sulfid-Erze
Sekundärsulfide – solche, die durch supergene Sekundäranreicherung gebildet werden – sind resistent ( feuerfest ) gegen Schwefelauswaschung. Diese Erze sind eine Mischung aus Kupferkarbonat-, Sulfat-, Phosphat- und Oxidmineralien und sekundären Sulfidmineralien, hauptsächlich Chalkosin, aber andere Mineralien wie Digenit können in einigen Lagerstätten wichtig sein.
Supergene Erze, die reich an Sulfiden sind, können durch Schaumflotation konzentriert werden. Ein typisches Chalkozit-Konzentrat kann zwischen 37 % und 40 % Kupfer im Sulfid enthalten, wodurch es im Vergleich zu Chalkopyrit-Konzentraten relativ günstig zu verhütten ist.
Einige supergene Sulfidablagerungen können unter Verwendung eines bakteriellen Oxidations-Haufenlaugungsverfahrens ausgelaugt werden, um die Sulfide zu Schwefelsäure zu oxidieren, was auch ein gleichzeitiges Auslaugen mit Schwefelsäure zur Herstellung einer Kupfersulfatlösung ermöglicht. Wie bei Oxiderzen werden Lösungsmittelextraktion und Elektrogewinnungstechnologien verwendet, um das Kupfer aus der übersättigten Laugungslösung zu gewinnen.
Supergene Sulfiderze, die reich an nativen Kupfermineralien sind, widerstehen der Behandlung mit Schwefelsäurelaugung in allen praktikablen Zeitskalen, und die dichten Metallpartikel reagieren nicht mit Schaumflotationsmedien. Wenn natives Kupfer nur ein kleiner Teil eines Supergenprofils ist, wird es normalerweise nicht gewonnen und in den Tailings gemeldet. Wenn sie reich genug sind, können natürliche Kupfererzkörper behandelt werden, um das enthaltene Kupfer über einen Schwerkraft-Trennkreislauf zu gewinnen, wo die Dichte des Metalls verwendet wird, um es von den leichteren Silikatmineralien zu befreien. Oft ist die Art der Gangart wichtig, da sich tonreiche einheimische Kupfererze als schwierig zu befreien erweisen.
Oxiderze
Oxidierte Kupfererzkörper können über mehrere Prozesse behandelt werden, wobei hydrometallurgische Prozesse verwendet werden, um Oxiderze zu behandeln, die von Kupferkarbonatmineralien wie Azurit und Malachit und anderen löslichen Mineralien wie Silikaten wie Chrysokoll oder Sulfaten wie Atacamit usw. dominiert werden.
Solche Oxiderze werden üblicherweise durch Schwefelsäure ausgelaugt, üblicherweise in einem Haufenlaugungs- oder Haldenlaugungsverfahren, um die Kupfermineralien in eine Schwefelsäurelösung freizusetzen, die mit Kupfersulfat in Lösung beladen ist. Die Kupfersulfatlösung (die übersättigte Laugungslösung) wird dann über eine Anlage zur Lösungsmittelextraktion und Elektrogewinnung (SX-EW) von Kupfer befreit, wobei die gesperrte (entblößte) Schwefelsäure auf die Halden zurückgeführt wird. Alternativ kann das Kupfer aus der übersättigten Lösung ausgefällt werden, indem es mit Eisenschrott in Kontakt gebracht wird; ein Prozess namens Zementierung. Zementkupfer ist normalerweise weniger rein als SX-EW-Kupfer. Üblicherweise wird Schwefelsäure als Auswaschmittel für Kupferoxid verwendet, obwohl es möglich ist, Wasser zu verwenden, insbesondere für Erze, die reich an ultralöslichen Sulfatmineralien sind. [ Zitat erforderlich ]
Im Allgemeinen wird die Schaumflotation nicht verwendet, um Kupferoxiderze zu konzentrieren, da Oxidmineralien nicht auf die Chemikalien oder den Prozess der Schaumflotation ansprechen (dh sie binden nicht an die auf Kerosin basierenden Chemikalien). Kupferoxiderze wurden gelegentlich durch Schaumflotation durch Sulfidierung der Oxidmineralien mit bestimmten Chemikalien behandelt, die mit den Oxidmineralpartikeln reagieren, um einen dünnen Sulfidreif (normalerweise Chalkosin) zu erzeugen, der dann durch die Schaumflotationsanlage aktiviert werden kann.
Sulfidverhüttung
Bis in die zweite Hälfte des 20. Jahrhunderts war die Verhüttung von Sulfiderzen fast das einzige Mittel zur Gewinnung von Kupfermetall aus abgebauten Erzen ( Primärkupfererzeugung ). Davenport et al. stellten 2002 fest, dass schon damals 80 % der weltweiten Primärkupferproduktion aus Kupfer-Eisen-Schwefel-Mineralien stammte und dass die überwiegende Mehrheit davon durch Schmelzen behandelt wurde.
Kupfer wurde ursprünglich aus Sulfiderzen gewonnen, indem das Erz direkt in einem Ofen geschmolzen wurde. Die Schmelzhütten befanden sich ursprünglich in der Nähe der Minen, um die Transportkosten zu minimieren. Dadurch wurden die unerschwinglichen Kosten für den Transport der Abfallmineralien und des in den kupferhaltigen Mineralien vorhandenen Schwefels und Eisens vermieden. Als jedoch die Kupferkonzentration in den Erzkörpern abnahm, wurden auch die Energiekosten zum Schmelzen des gesamten Erzes unerschwinglich, und es wurde notwendig, die Erze zuerst zu konzentrieren.
Anfängliche Konzentrationstechniken umfassten Handsortierung [10] und Schwerkraftkonzentration. Sie führten zu hohen Kupferverlusten. Folglich war die Entwicklung des Schaumflotationsverfahrens ein großer Fortschritt in der Aufbereitung von Mineralien. [11] Es ermöglichte die Entwicklung der riesigen Mine Bingham Canyon in Utah. [12]
Im zwanzigsten Jahrhundert wurden die meisten Erze vor dem Schmelzen konzentriert. Das Schmelzen erfolgte zunächst mit Sinteranlagen und Hochöfen [13] oder mit Röstern und Flammöfen. [14] Bis in die 1960er-Jahre dominierten Röst- und Flammofenschmelzen die Primärkupferproduktion. [8]
Braten
Der Röstprozess wird in der Regel in Kombination mit Flammöfen durchgeführt. Im Röster wird das Kupferkonzentrat teilweise oxidiert, um „Kalzin“ und Schwefeldioxidgas zu erzeugen. Die Stöchiometrie der auftretenden Reaktion ist:
- 2 CuFeS 2 + 3 O 2 → 2 FeO + 2 CuS + 2 SO 2
Das Rösten hinterlässt im Allgemeinen mehr Schwefel im kalzinierten Produkt (15 % im Fall des Rösters in den Mount Isa Mines [15] ) als eine Sinteranlage im gesinterten Produkt hinterlässt (etwa 7 % im Fall des elektrolytischen Raffinations- und Schmelzofens [ 16] ).
Seit 2005 ist das Rösten bei der Behandlung von Kupferkonzentraten nicht mehr üblich, da seine Kombination mit Flammöfen nicht energieeffizient ist und die SO 2 -Konzentration im Abgas des Rösters für eine kosteneffiziente Abscheidung zu verdünnt ist. [8] Direktschmelzen wird jetzt bevorzugt, zB unter Verwendung der folgenden Schmelztechnologien: Schwebeschmelzöfen, Isasmelt-, Noranda-, Mitsubishi- oder El-Teniente-Öfen. [8]
Schmelzen

Ersatz des Flammofenschmelzens durch das Schwebeschmelzen, bezogen auf die Anzahl der Kupferhütten, die diese Technologie einsetzen.
Das anfängliche Schmelzen des zu schmelzenden Materials wird üblicherweise als Schmelz- oder Mattschmelzstufe bezeichnet . Sie kann in einer Vielzahl von Öfen vorgenommen werden, darunter die weitgehend veralteten Hochöfen und Flammöfen, aber auch Flashöfen, Isasmelt-Öfen etc. [8] Das Produkt dieser Schmelzstufe ist ein Gemisch aus Kupfer, Eisen und Schwefel ist mit Kupfer angereichert und wird matt oder kupfermatt.[8] Der Begriff Mattgrad wird normalerweise verwendet, um sich auf den Kupfergehalt des Rohsteins zu beziehen. [17]
Der Zweck der Mattschmelzstufe besteht darin, so viel wie möglich von den unerwünschten Eisen-, Schwefel- und Gangmineralien (wie Siliziumoxid, Magnesia, Aluminiumoxid und Kalkstein) zu eliminieren und gleichzeitig den Kupferverlust zu minimieren. [17] Dies wird erreicht, indem Eisensulfide mit Sauerstoff (in Luft oder mit Sauerstoff angereicherter Luft) umgesetzt werden, um Eisenoxide (hauptsächlich als FeO, aber mit etwas Magnetit (Fe 3O 4)) und Schwefeldioxid zu erzeugen. [17]
Kupfersulfid und Eisenoxid können sich vermischen, aber wenn ausreichend Kieselsäure hinzugefügt wird, bildet sich eine separate Schlackenschicht. [18] Die Zugabe von Kieselsäure senkt auch den Schmelzpunkt (oder besser gesagt die Liquidustemperatur) der Schlacke, was bedeutet, dass der Schmelzprozess bei einer niedrigeren Temperatur betrieben werden kann. [18]
Die Schlackenbildungsreaktion ist:
- FeO + SiO 2 → FeO.SiO 2[17]
Schlacke ist weniger dicht als Stein, daher bildet sie eine Schicht, die auf dem Stein schwimmt. [19]
Kupfer kann auf drei Arten aus dem Stein verloren gehen: als in der Schlacke gelöstes Kupferoxid (Cu 2O), [20] als in der Schlacke gelöstes Sulfidkupfer [21] oder als winzige Tröpfchen (oder Prills ) des Steins, die darin suspendiert sind Schlacke. [22] [23]
Die als Oxidkupfer verlorene Kupfermenge steigt mit steigendem Sauerstoffpotential der Schlacke. [23] Das Sauerstoffpotential steigt im Allgemeinen, wenn der Kupfergehalt des Steins erhöht wird. [24] Somit nimmt der Kupferverlust als Oxid zu, wenn der Kupfergehalt des Steins zunimmt. [25]
Andererseits nimmt die Löslichkeit von sulfidischem Kupfer in Schlacke ab, wenn der Kupfergehalt des Steins über etwa 40 % hinaus ansteigt. [21] Nagamori berechnete, dass mehr als die Hälfte des in Schlacken gelösten Kupfers aus Steinen mit weniger als 50 % Kupfer sulfidisches Kupfer ist. Oberhalb dieser Zahl beginnt oxidisches Kupfer zu dominieren. [21]
Der Kupferverlust als in der Schlacke suspendierte Prills hängt von der Größe der Prills, der Viskosität der Schlacke und der verfügbaren Absetzzeit ab. [26] Rosenqvist schlug vor, dass etwa die Hälfte der Kupferverluste an die Schlacke auf suspendierte Prills zurückzuführen seien. [26]
Die Masse der in der Schmelzstufe erzeugten Schlacke hängt vom Eisengehalt des dem Schmelzofen zugeführten Materials und der angestrebten Steingüte ab. Je größer der Eisengehalt der Beschickung ist, desto mehr Eisen muss für einen gegebenen Mattgrad in die Schlacke zurückgewiesen werden. In ähnlicher Weise erfordert die Erhöhung des Ziel-Steingrades die Zurückweisung von mehr Eisen und eine Erhöhung des Schlackenvolumens.
Somit sind die zwei Faktoren, die den Verlust von Kupfer an die Schlacke in der Schmelzphase am stärksten beeinflussen, folgende:
- Mattgrad
- Masse Schlacke. [18]
Dies bedeutet, dass es eine praktische Grenze dafür gibt, wie hoch der Mattgrad sein kann, wenn der Kupferverlust an die Schlacke minimiert werden soll. Daher sind weitere Verarbeitungsstufen (Konvertierung und Feuerveredelung) erforderlich.
In den folgenden Unterabschnitten werden einige der beim Mattschmelzen verwendeten Prozesse kurz beschrieben.
Schmelzen im Flammofen
Flammöfen sind lange Öfen, die nasses, trockenes oder geröstetes Konzentrat behandeln können. [8] Die meisten der in den letzten Jahren verwendeten Flammöfen behandelten geröstetes Konzentrat, weil das Einbringen von trockenen Ausgangsmaterialien in den Flammofen energieeffizienter ist und weil die Eliminierung eines Teils des Schwefels im Röster zu höheren Mattgraden führt. [8]
Die Flammofenbeschickung wird dem Ofen durch Beschickungslöcher entlang den Seiten des Ofens zugeführt. [8] Zusätzliche Kieselsäure wird normalerweise hinzugefügt, um die Bildung der Schlacke zu unterstützen. Der Ofen wird mit Kohlenstaub-, Heizöl- oder Erdgasbrennern [27] befeuert und die feste Charge aufgeschmolzen.
Flammöfen können zusätzlich mit flüssiger Schlacke aus der späteren Umwandlungsstufe beschickt werden, um das enthaltene Kupfer und andere hochkupferhaltige Materialien zurückzugewinnen. [27] befeuert
Da das Hallofenbad ruhig ist, findet eine sehr geringe Oxidation der Beschickung statt (und somit wird sehr wenig Schwefel aus dem Konzentrat eliminiert). Es ist im Wesentlichen ein Schmelzprozess. [26] Folglich haben nass beschickte Nachhallöfen weniger Kupfer in ihrem Steinprodukt als kalzinierte Öfen, und sie haben auch geringere Kupferverluste an die Schlacke. [27] befeuert Gill gibt einen Kupfer-in-Schlacke-Wert von 0,23 % für einen feucht beschickten Hallofen gegenüber 0,37 % für einen calcinbeschickten Ofen an. [27] befeuert
Bei mit Kalzinierung beschickten Öfen wurde ein erheblicher Teil des Schwefels während der Röststufe eliminiert, und die Kalzinierung besteht aus einer Mischung aus Kupfer- und Eisenoxiden und -sulfiden. Der Nachhallofen bewirkt, dass sich diese Spezies bei der Betriebstemperatur des Ofens (etwa 1600 ° C am Brennerende des Ofens und etwa 1200 ° C am Abzugsende; [28] der Stein beträgt etwa 1100 ° C und etwa 1100 ° C ) dem chemischen Gleichgewicht annähern die Schlacke hat eine Temperatur von etwa 1195 °C [27] befeuert ). In diesem Äquilibrierungsprozess tauscht mit Kupferverbindungen verbundener Sauerstoff mit mit Eisenverbindungen verbundenem Schwefel aus, wodurch der Eisenoxidgehalt des Ofens erhöht wird, und die Eisenoxide interagieren mit Siliciumdioxid und anderen Oxidmaterialien, um die Schlacke zu bilden. [27] befeuert
Die wichtigste Gleichgewichtsreaktion ist:
- Cu 2O + FeS = Cu 2S + FeO [27] befeuert
Die Schlacke und der Stein bilden getrennte Schichten, die als getrennte Ströme aus dem Ofen entfernt werden können. Die Schlackenschicht wird periodisch durch ein Loch in der Wand des Ofens oberhalb der Höhe der Mattierungsschicht fließen gelassen. Der Stein wird entfernt, indem er durch ein Loch in Pfannen abgelassen wird, damit er mit einem Kran zu den Konvertern transportiert wird. [27] befeuert Dieser Entwässerungsprozess wird als Abstich des Ofens bezeichnet. [27] befeuert ist normalerweise ein Loch durch einen wassergekühlten Kupferblock, der die Erosion der feuerfesten Steine verhindert, die den Ofen auskleiden. Wenn das Entfernen des Steins oder der Schlacke abgeschlossen ist, wird das Loch normalerweise mit Ton verstopft, der entfernt wird, wenn der Ofen für einen erneuten Abstich bereit ist.
Flammöfen wurden oft verwendet, um geschmolzene Konverterschlacke zu behandeln, um enthaltenes Kupfer zurückzugewinnen. [27] befeuert Dieses wurde aus von Kränen getragenen Pfannen in die Öfen gegossen. Die Konverterschlacke ist jedoch reich an Magnetit [29], und ein Teil dieses Magnetits würde aus der Konverterschlacke (aufgrund ihres höheren Schmelzpunkts) ausfallen, eine Ansammlung auf dem Herd des Nachhallofens bilden und ein Abschalten des Ofens erforderlich machen den Ansatz entfernen. [29], Diese Ansatzbildung begrenzt die Menge an Konverterschlacke, die in einem Flammofen behandelt werden kann. [29],
Während Flammöfen sehr geringe Kupferverluste an die Schlacke haben, sind sie nicht sehr energieeffizient und die geringen Schwefeldioxidkonzentrationen in ihren Abgasen machen ihre Abscheidung unwirtschaftlich. [8] Folglich investierten Hüttenbetreiber in den 1970er und 1980er Jahren viel Geld in die Entwicklung neuer, effizienterer Kupferschmelzverfahren. [30] Darüber hinaus wurden Schwebeschmelztechnologien in früheren Jahren entwickelt und begannen, Flammöfen zu ersetzen. Bis 2002 wurden 20 der 1994 noch in Betrieb befindlichen 30 Flammöfen stillgelegt. [8]
Flash-Ofen-Schmelzen
Beim Schwebeschmelzen wird das Konzentrat in einem Luft- oder Sauerstoffstrom dispergiert und die Schmelzreaktionen werden weitgehend abgeschlossen, während die Mineralpartikel noch im Flug sind. [30] Die reagierten Teilchen setzen sich dann in einem Bad am Boden des Ofens ab, wo sie sich wie das Kalzinieren in einem Flammofen verhalten. [31] Auf der Mattschicht bildet sich eine Schlackenschicht, die separat aus dem Ofen abgezapft werden kann. [31]
Konvertieren

Sauerstofffreies Kupfer, auch „Tough-Pitch“-Kupfer genannt (ca. 98 % rein), enthält Antimon und Nickel
Der in der Schmelze produzierte Stein enthält 30–70 % Kupfer (abhängig vom verwendeten Verfahren und der Betriebsphilosophie der Schmelze), hauptsächlich als Kupfersulfid, sowie Eisensulfid. Der Schwefel wird bei hoher Temperatur als Schwefeldioxid entfernt, indem Luft durch geschmolzenen Stein geblasen wird:
- 2 CuS + 3 O 2 → 2 CuO + 2 SO 2
- CuS + O 2 → Cu + SO 2
In einer Parallelreaktion wird das Eisensulfid in Schlacke umgewandelt:
- 2 FeS + 3 O 2 → 2 FeO + 2 SO 2
- 2 FeO + SiO 2 → Fe 2SiO 4
Die Reinheit dieses Produkts beträgt 98 %, es ist Kupfermolche because of the broken surface created by the escape of sulfur dioxide gas as blister copper pigs or ingots are cooled. By-products generated in the process are sulfur dioxide and slag. The sulfur dioxide is captured for use in earlier leaching processes.
Brandveredelung
Das Blisterkupfer wird in einen Anodenofen gegeben, einen Ofen, der das Blisterkupfer in zwei Stufen zu Kupfer in Anodenqualität raffiniert, indem er den größten Teil des verbleibenden Schwefels und Eisens entfernt und dann den während der ersten Stufe eingeführten Sauerstoff entfernt. Diese zweite Stufe, die oft als Polung bezeichnet wird, wird durchgeführt, indem Erdgas oder ein anderes Reduktionsmittel durch das geschmolzene Kupferoxid geblasen wird. Wenn diese Flamme grün brennt, was das Kupferoxidationsspektrum anzeigt, ist der Sauerstoff größtenteils abgebrannt. Dadurch entsteht Kupfer mit einer Reinheit von etwa 99 %.
Elektroraffination

Vorrichtung zum elektrolytischen Raffinieren von Kupfer
Das Kupfer wird durch Elektrolyse raffiniert. Die aus aufbereitetem Blisterkupfer gegossenen Anoden werden in eine wässrige Lösung aus 3–4 % Kupfersulfat und 10–16 % Schwefelsäure gegeben. Kathoden sind dünn gewalzte Bleche aus hochreinem Kupfer oder heute häufiger wiederverwendbare Ausgangsbleche aus Edelstahl (wie beim IsaKidd-Verfahren). [32] Ein Potential von nur 0,2–0,4 Volt ist erforderlich, damit der Prozess beginnt. In Industrieanlagen sind Stromdichten bis 420 A/m 2 möglich. [33] An der Anode lösen sich Kupfer und unedlere Metalle auf. Edelmetalle wie Silber, Gold, Selen und Tellur setzen sich als Anodenschleim am Boden der Zelle ab, der ein verkaufsfähiges Nebenprodukt bildet. Kupfer(II)-Ionen wandern durch den Elektrolyten zur Kathode. An der Kathode scheidet sich Kupfermetall ab, aber weniger edle Bestandteile wie Arsen und Zink bleiben in Lösung, sofern nicht eine höhere Spannung angelegt wird. [34] Die Reaktionen sind:
An der Anode: Cu (s) → Cu 2+ (aq) + 2e −
An der Kathode: Cu 2+ (aq) + 2e − → Cu (s)
Konzentrat- und Kupfervermarktung
Von Minen produzierte Kupferkonzentrate werden an Hütten und Raffinerien verkauft, die das Erz behandeln und das Kupfer raffinieren und diese Dienstleistung über Behandlungsgebühren (TCs) und Raffinationsgebühren (RCs) in Rechnung stellen. Der globale Markt für Kupferkonzentrate [35] wurde 2019 auf 81 Milliarden US-Dollar geschätzt und soll bis 2027 voraussichtlich 93 Milliarden US-Dollar erreichen und bei einer CAGR von 2,5 % wachsen. Die TCs werden in US$ pro Tonne behandelten Konzentrats berechnet und RCs werden in Cent pro behandeltem Pfund berechnet und lauten auf US-Dollar, wobei Benchmark-Preise jährlich von großen japanischen Hütten festgelegt werden. Der Kunde kann in diesem Fall eine Hütte sein, die Blisterkupferbarren an einen Veredler weiterverkauft, oder ein vertikal integrierter Hüttenveredler.
Eine vorherrschende Form von Kupferkonzentrat enthält Gold und Silber, wie das von Bougainville Copper Limited in der Panguna-Mine von Anfang der 1970er bis Ende der 1980er Jahre produzierte.
Der typische Vertrag für einen Miner wird gegen den Preis der London Metal Exchange abzüglich der TC-RCs und aller anwendbaren Strafen oder Gutschriften berechnet. Gegen Kupferkonzentrate können je nach Gehalt an schädlichen Elementen wie Arsen, Wismut, Blei oder Wolfram Sanktionen verhängt werden. Da ein großer Teil der Kupfersulfid-Erzkörper Silber oder Gold in nennenswerten Mengen enthält, kann dem Bergmann für diese Metalle eine Gutschrift gezahlt werden, wenn ihre Konzentration im Konzentrat über einer bestimmten Menge liegt. Normalerweise berechnet der Raffinerie- oder Schmelzer dem Bergmann eine Gebühr, die auf der Konzentration basiert; ein typischer Vertrag legt fest, dass für jede Unze des Metalls im Konzentrat oberhalb einer bestimmten Konzentration eine Gutschrift fällig wird; Darunter behält die Schmelzerei das Metall, wenn es wiedergewonnen wird, und verkauft es zur Deckung der Kosten.
Kupferkonzentrat wird entweder über Spotkontrakte oder als eigenständiges Zwischenprodukt im Rahmen von Langzeitkontrakten gehandelt. Oft verkauft die Hütte das Kupfermetall selbst im Auftrag des Bergmanns. Der Bergmann erhält den Preis zum Zeitpunkt des Verkaufs durch den Schmelzer und nicht den Preis am Tag der Lieferung des Konzentrats. Bei einem Angebotspreissystem wird vereinbart, dass der Preis zu einem festen Datum in der Zukunft liegt, typischerweise 90 Tage ab dem Zeitpunkt der Lieferung an die Schmelzhütte.
Eine Kupferkathode der Güteklasse A besteht zu 99,99 % aus Kupfer in 1 cm dicken Blechen mit einer Fläche von etwa 1 Quadratmeter und einem Gewicht von etwa 200 Pfund. Es ist ein echter Rohstoff, der an die Metallbörsen in New York City (COMEX), London (London Metals Exchange) und Shanghai (Shanghai Futures Exchange) geliefert und gehandelt werden kann. Kupferkathoden werden häufig indirekt über Optionsscheine, Optionen oder Swap-Kontrakte an den Börsen gehandelt, sodass der Großteil des Kupfers an der LME/COMEX/SFE gehandelt wird, die Lieferung jedoch direkt erfolgt, indem das physische Kupfer logistisch transportiert und das Kupferblech von dort übertragen wird die physischen Lager selbst.
Die chemische Spezifikation für Kupfer in Elektrolytqualität ist ASTM B 115-00 (eine Norm, die die Reinheit und den maximalen elektrischen Widerstand des Produkts angibt).
Mr. Nick Sun [email protected]
Postzeit: 27. September 2020