Co to jest ekstrakcja miedzi?
Wydobycie miedzi odnosi się do metod stosowanych do pozyskiwania miedzi z jej rud. Konwersja miedzi składa się z szeregu procesów fizycznych i elektrochemicznych. Metody ewoluowały i różnią się w zależności od kraju, w zależności od źródła rudy, lokalnych przepisów środowiskowych i innych czynników.
Jak we wszystkich operacjach wydobywczych, ruda zwykle musi być wzbogacona (zagęszczona). Techniki przetwarzania zależą od rodzaju rudy. Jeśli ruda składa się głównie z minerałów siarczkowych miedzi (takich jak chalkopiryt), ruda jest kruszona i mielona w celu uwolnienia cennych minerałów z minerałów odpadowych (tzw. skały płonnej). Następnie jest zagęszczany za pomocą flotacji mineralnej. Koncentrat jest następnie zwykle sprzedawany do odległych hut, chociaż w pobliżu niektórych dużych kopalń znajdują się huty. Taka kolokacja kopalń i hut była bardziej typowa w XIX i na początku XX wieku, kiedy mniejsze huty mogły być ekonomiczne. Koncentraty siarczków są zwykle wytapiane w takich piecach jak piec zawiesinowy Outokumpu lub Inco lub piec ISASMELT w celu wytworzenia kamienia, który musi być przetwarzany i rafinowany w celu wytworzenia miedzi anodowej. Ostatnim procesem rafinacji jest elektroliza. Ze względów ekonomicznych i środowiskowych wiele produktów ubocznych wydobycia jest odzyskiwanych. Na przykład dwutlenek siarki jest wychwytywany i przekształcany w kwas siarkowy, który można następnie wykorzystać w procesie ekstrakcji lub sprzedać do celów takich jak produkcja nawozów.
Utlenione rudy miedzi mogą być przetwarzane przez ekstrakcję hydrometalurgiczną.
Historia

Górnicy w kopalni Tamarack w Kraju Miedzi, w 1905 r.
Najwcześniejsze dowody kucia na zimno rodzimej miedzi pochodzą z wykopalisk w Çayönü Tepesi we wschodniej Anatolii, datowanych na okres od 7200 do 6600 pne. [1] Wśród różnych przedmiotów uważanych za wotywne lub amulety był jeden, który wyglądał jak haczyk na ryby, a drugi jak szydło. Inne znalezisko, w jaskini Shanidar w Mergasur w Iraku, zawiera miedziane paciorki, datowane na 8700 p.n.e. [2]
Jedna z najstarszych znanych kopalń miedzi na świecie, w przeciwieństwie do eksploatacji złóż powierzchniowych, znajduje się w dolinie Timna w Izraelu od czwartego tysiąclecia pne, z wykorzystaniem złóż powierzchniowych od szóstego do piątego tysiąclecia. [3] [4]
Stanowisko archeologiczne w Pločniku w południowo-wschodniej Europie (Serbia) zawiera najstarsze, bezpiecznie datowane [ wątpliwe – dyskutować ] dowody na wytwarzanie miedzi w wysokiej temperaturze, pochodzące z 5000 lat p.n.e. Znalezisko z czerwca 2010 roku przedłuża o kolejne 500 lat wcześniejsze zapisy dotyczące wytopu miedzi z Rudnej Glava (Serbia), datowane na 5 tysiąclecie p.n.e. [5]
Technologia wytopu miedzi dała początek epoce miedzi, czyli epoce chalkolitu, a następnie epoce brązu. Epoka brązu nie byłaby możliwa bez rozwoju technologii wytapiania przez ludzi.
Stężenie
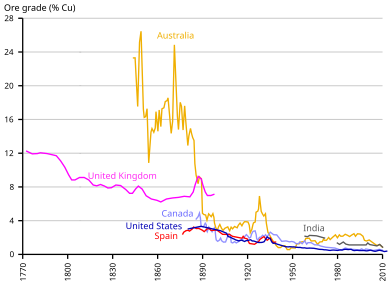
Zmniejszające się stężenie miedzi w rudach wymaga obecnie wstępnej obróbki rud.
Większość rud miedzi zawiera tylko niewielki procent miedzi metalicznej związanej z cennymi minerałami rudy, przy czym pozostałą część rudy stanowią niechciane skały lub skały płonne, zazwyczaj minerały krzemianowe lub tlenki, dla których często nie ma żadnej wartości. W niektórych przypadkach odpady poflotacyjne były wycofywane w celu odzyskania utraconej wartości, ponieważ technologia odzyskiwania miedzi uległa poprawie. Średnia zawartość rud miedzi w XXI wieku wynosi poniżej 0,6% miedzi, przy czym udział surowców gospodarczych (w tym miedź) wynosi mniej niż 2% całkowitej objętości skały rudnej. Kluczowym celem w metalurgicznej obróbce każdej rudy jest oddzielenie minerałów rudy od minerałów skały płonnej w skale.
Pierwszym etapem każdego procesu w obwodzie obróbki metalurgicznej jest dokładne rozdrabnianie lub rozdrabnianie , gdzie skała jest kruszona w celu wytworzenia małych cząstek (<100 μm) składających się z poszczególnych faz mineralnych. Cząstki te są następnie oddzielane w celu usunięcia skały płonnej (pozostałości skał), po czym następuje proces fizycznego uwalniania minerałów rudy ze skały. Proces uwalniania rud miedzi zależy od tego, czy są to rudy tlenkowe czy siarczkowe. [6]
Kolejne etapy zależą od rodzaju rudy zawierającej miedź i tego, co zostanie wydobyte. W przypadku rud tlenkowych zwykle przeprowadza się hydrometalurgiczny proces uwalniania, w którym wykorzystuje się rozpuszczalny charakter minerałów rudy z korzyścią dla zakładu obróbki metalurgicznej. W przypadku rud siarczkowych, zarówno wtórnych (supergen), jak i pierwotnych (hipogen), do fizycznego oddzielenia rudy od skały płonnej stosuje się flotację pianową. W przypadku specjalnych brył rudy zawierającej miedź rodzimą lub odcinków brył rud bogatych w miedź supergeniczną, minerał ten można odzyskać za pomocą prostego obwodu grawitacyjnego.
Flotacja piany

Komórki flotacyjne z pianką do koncentracji minerałów siarczkowych miedzi i niklu, Falconbridge, Ontario.
Nowoczesny proces flotacji piany został niezależnie wynaleziony na początku XX wieku w Australii przez CV Pottera i mniej więcej w tym samym czasie przez GD Delprata. [7]

Pęcherzyki powietrza załadowane siarczkiem miedzi na ogniwie Jamesona w zakładzie flotacyjnym Prominent Hillmine w Australii Południowej
Wszystkie pierwotne rudy siarczkowe siarczków miedzi oraz większość koncentratów wtórnych siarczków miedzi (będących chalkocytem) poddaje się wytapianiu. Istnieją pewne procesy ługowania w kadzi lub ługowania ciśnieniowego w celu solubilizacji koncentratów chalkocytu i wytworzenia katody miedziowej z powstałego roztworu ługowania, ale jest to niewielka część rynku.
Koncentraty węglanowe są stosunkowo niewielkim produktem wytwarzanym w cementowniach miedzi, zwykle jako końcowy etap operacji ługowania na hałdzie. Takie koncentraty węglanowe można poddać obróbce w instalacji ekstrakcji rozpuszczalnikowej i elektrolitycznej (SX-EW) lub przetopić.
Rudę miedzi rozdrabnia się i miele do takich rozmiarów, aby pomiędzy minerałami rudy siarczku miedzi a minerałami skały płonnej wystąpił akceptowalnie wysoki stopień uwolnienia. Rudę następnie zwilża się, zawiesza w zawiesinie i miesza z ksantogenianami lub innymi odczynnikami, co nadaje cząstkom siarczku hydrofobowość. Typowe odczynniki obejmują etyloksantogenian potasu i etyloksantogenian sodu, ale stosuje się również ditiofosforany i ditiokarbaminiany.
Obrobiona ruda jest wprowadzana do wypełnionego wodą zbiornika napowietrzającego zawierającego środek powierzchniowo czynny, taki jak metyloizobutylokarbinol (MIBC). Powietrze jest stale przetłaczane przez zawiesinę, a pęcherzyki powietrza przyczepiają się do hydrofobowych cząstek siarczku miedzi, które są odprowadzane na powierzchnię, gdzie tworzą pianę i są usuwane. Te szumowiny są na ogół poddawane działaniu oczyszczającej komórki oczyszczającej w celu usunięcia nadmiaru krzemianów i usunięcia innych minerałów siarczkowych, które mogą szkodliwie wpływać na jakość koncentratu (zazwyczaj galena), a końcowy koncentrat wysyła się do wytopu. Skała, która nie odpłynęła w komorze flotacyjnej, jest albo odrzucana jako odpady poflotacyjne, albo dalej przetwarzana w celu wydobycia innych metali, takich jak ołów (z galeny) i cynk (z sfalerytu), jeśli takie istnieją. Aby poprawić wydajność procesu, stosuje się wapno w celu podniesienia pH kąpieli wodnej, powodując większą jonizację kolektora i preferencyjne wiązanie się z chalkopirytem (CuFeS 2) i unikaniem pirytu (FeS 2). Żelazo występuje w obu minerałach strefy pierwotnej. Rudy miedzi zawierające chalkopiryt można zagęszczać w celu wytworzenia koncentratu o zawartości od 20% do 30% miedzi w koncentracie (zwykle 27-29% miedzi); pozostałą część koncentratu stanowi żelazo i siarka w chalkopirycie oraz niepożądane zanieczyszczenia, takie jak krzemianowe minerały skały płonnej lub inne minerały siarczkowe, zazwyczaj niewielkie ilości pirytu, sfalerytu lub galeny. Koncentraty chalkocytu zazwyczaj zawierają od 37% do 40% miedzi w koncentracie, ponieważ chalkocyt nie zawiera żelaza w minerale.
Ekstrakcja hydrometalurgiczna
Rudy siarczkowe
Wtórne siarczki – te powstałe w wyniku wtórnego wzbogacania supergenów – są odporne ( ogniotrwałe ) na ługowanie siarką. Rudy te są mieszaniną węglanu miedzi, siarczanu, fosforanu i minerałów tlenkowych oraz wtórnych minerałów siarczkowych, głównie chalkocytu, ale inne minerały, takie jak digenit, mogą być ważne w niektórych złożach.
Rudy supergenów bogate w siarczki można zatężać za pomocą flotacji pianowej. Typowy koncentrat chalkocytu może klasyfikować od 37% do 40% miedzi w siarczku, co czyni go stosunkowo tanim w wytapianiu w porównaniu z koncentratami chalkopirytu.
Niektóre osady siarczków supergenów można ługować przy użyciu procesu ługowania bakteryjnego na hałdzie utleniania w celu utlenienia siarczków do kwasu siarkowego, co pozwala również na jednoczesne ługowanie kwasem siarkowym w celu wytworzenia roztworu siarczanu miedzi. Podobnie jak w przypadku rud tlenkowych, do odzyskiwania miedzi z macierzystego roztworu ługującego stosuje się technologie ekstrakcji rozpuszczalnikowej i elektrolitycznego otrzymywania metali.
Rudy siarczku supergenu bogate w naturalne minerały miedzi są oporne na ługowanie kwasem siarkowym we wszystkich możliwych do zastosowania skalach czasowych, a gęste cząstki metalu nie reagują z pianą flotacyjną. Zazwyczaj, jeśli natywna miedź stanowi niewielką część profilu supergenu, nie będzie ona odzyskiwana i będzie zgłaszana do odpadów przeróbczych. Gdy są wystarczająco bogate, bryły rodzimej rudy miedzi mogą być przetwarzane w celu odzyskania zawartej miedzi za pomocą obwodu rozdzielania grawitacyjnego, w którym gęstość metalu jest wykorzystywana do uwalniania go z lżejszych minerałów krzemianowych. Często istotna jest natura skały płonnej, ponieważ bogate w glinę rodzime rudy miedzi okazują się trudne do wyzwolenia.
Rudy tlenkowe
Utlenione bryły rudy miedzi można poddawać obróbce kilkoma procesami, przy czym procesy hydrometalurgiczne stosuje się do obróbki rud tlenkowych zdominowanych przez minerały z węglanu miedzi, takie jak azuryt i malachit, oraz inne rozpuszczalne minerały, takie jak krzemiany, takie jak chryzokola, lub siarczany, takie jak atacamit i tak dalej.
Takie rudy tlenkowe są zwykle ługowane kwasem siarkowym, zwykle w procesie ługowania na hałdzie lub na hałdzie w celu uwolnienia minerałów miedzi do roztworu kwasu siarkowego obciążonego siarczanem miedzi w roztworze. Roztwór siarczanu miedzi (ciężarny roztwór ługujący) jest następnie usuwany z miedzi za pomocą instalacji do ekstrakcji rozpuszczalnikowej i otrzymywania elektrolitycznego (SX-EW), z zakorkowanym (oczyszczonym) kwasem siarkowym zawracanym z powrotem na hałdy. Alternatywnie miedź można wytrącić z roztworu macierzystego przez kontaktowanie go ze złomem żelaza; proces zwany cementacją. Miedź cementowa jest zwykle mniej czysta niż miedź SX-EW. Powszechnie kwas siarkowy jest stosowany jako środek odcieku tlenku miedzi, chociaż możliwe jest użycie wody, szczególnie w przypadku rud bogatych w ultrarozpuszczalne minerały siarczanowe. [ potrzebne cytowanie ]
Ogólnie rzecz biorąc, flotacja pianowa nie jest stosowana do zagęszczania rud tlenku miedzi, ponieważ minerały tlenkowe nie reagują na chemikalia lub proces flotacji pianowej (tj. nie wiążą się z chemikaliami na bazie nafty). Rudy tlenku miedzi czasami poddaje się obróbce metodą flotacji pianowej poprzez siarczkowanie minerałów tlenkowych pewnymi chemikaliami, które reagują z cząstkami minerałów tlenkowych w celu wytworzenia cienkiej szadzi siarczkowej (zwykle chalkocytu), która może być następnie aktywowana przez instalację do flotacji pianowej.
Wytapianie siarczków
Do drugiej połowy XX wieku wytapianie rud siarczkowych było prawie jedynym sposobem produkcji miedzi metalicznej z rud górniczych ( produkcja miedzi pierwotna ). Davenport i in. zauważyli w 2002 r., że już wtedy 80% światowej produkcji miedzi pierwotnej pochodziło z minerałów miedziowo-żelazowo-siarkowych i że zdecydowaną większość z nich poddano wytapianiu.
Miedź była początkowo odzyskiwana z rud siarczkowych poprzez bezpośrednie przetapianie rudy w piecu. [9] Huty początkowo lokowano w pobliżu kopalń, aby zminimalizować koszty transportu. Pozwoliło to uniknąć zaporowych kosztów transportu minerałów odpadowych oraz siarki i żelaza obecnych w minerałach zawierających miedź. Jednak wraz ze spadkiem stężenia miedzi w bryłach rudy, koszty energii związane z wytopem całej rudy również stały się zaporowe i konieczne stało się skoncentrowanie rud w pierwszej kolejności.
Początkowe techniki koncentracji obejmowały sortowanie ręczne [10] i koncentrację grawitacyjną. Powodowały one duże straty miedzi. W konsekwencji rozwój procesu flotacji pianowej był ważnym krokiem naprzód w przetwarzaniu minerałów. [11] Umożliwiło to rozwój gigantycznej kopalni Bingham Canyon w stanie Utah. [12]
W XX wieku większość rud koncentrowano przed wytopem. Wytapiania prowadzono początkowo za pomocą spiekalni i wielkich pieców [13] lub palarni i pieców rewerberacyjnych. [14] Prażenie i wytapianie w piecach rewerberacyjnych dominowało w produkcji miedzi pierwotnej do lat 60. XX wieku. [8]
Prażenie
Proces prażenia odbywa się na ogół w połączeniu z piecami pogłosowymi. W piecu do prażenia koncentrat miedzi jest częściowo utleniany w celu wytworzenia „kalcynu” i gazowego dwutlenku siarki. Stechiometria zachodzącej reakcji to:
- 2 CuFeS 2 + 3 O 2 → 2 FeO + 2 CuS + 2 SO 2
Prażenie generalnie pozostawia więcej siarki w kalcynowanym produkcie (15% w przypadku palarni w Mount Isa Mines [15] ) niż liście spiekalni w spiekanym produkcie (około 7% w przypadku huty rafinacji elektrolitycznej i wytapiania) [ 16] ).
Od 2005 r. prażenie nie jest już powszechne w obróbce koncentratu miedzi, ponieważ jego połączenie z piecami pogłosowymi nie jest wydajne energetycznie, a stężenie SO2 w gazie 2 jest zbyt rozcieńczone, aby opłacalne było wychwytywanie. [8] Preferowane jest obecnie wytapianie bezpośrednie, np. z wykorzystaniem następujących technologii wytapiania: wytapianie zawiesinowe, piece Isasmelt, Noranda, Mitsubishi czy El Teniente. [8]
Wytapianie

Zastąpienie wytopu pieca rewerberacyjnego przez wytapianie zawiesinowe, związane z liczbą hut miedzi stosujących tę technologię.
Początkowe topienie materiału przeznaczonego do wytapiania jest zwykle określane jako wytapiania lub wytapiania kamienia . Może być wykonywana w różnych piecach, w tym w dużej mierze przestarzałych wielkich piecach i piecach płomieniowych, a także piecach zawiesinowych, piecach Isasmelt itp. [8] Produktem tego etapu wytapiania jest mieszanina miedzi, żelaza i siarki, która jest wzbogacony w miedź, który nazywa się matowym lub miedzianym matowym.[8] Termin gatunek matowy jest zwykle używany w odniesieniu do zawartości miedzi w macie. [17]
Celem etapu wytapiania kamienia jest wyeliminowanie jak największej ilości niechcianych minerałów żelaza, siarki i skały płonnej (takich jak krzemionka, magnezja, tlenek glinu i wapień) przy jednoczesnej minimalizacji utraty miedzi. [17] Osiąga się to poprzez reakcję siarczków żelaza z tlenem (w powietrzu lub powietrzu wzbogaconym tlenem) w celu wytworzenia tlenków żelaza (głównie jako FeO, ale z pewną ilością magnetytu (Fe 3O 4)) i dwutlenku siarki. [17]
Siarczek miedzi i tlenek żelaza mogą się mieszać, ale po dodaniu wystarczającej ilości krzemionki tworzy się oddzielna warstwa żużla. [18] Dodanie krzemionki obniża również temperaturę topnienia (a właściwie temperaturę likwidusu) żużla, co oznacza, że proces wytapiania może przebiegać w niższej temperaturze. [18]
Reakcja tworzenia żużla to:
- FeO + SiO 2 → FeO.SiO 2[17]
Żużel jest mniej gęsty niż mat, więc tworzy warstwę, która unosi się na macie. [19]
Miedź może być tracona z kamienia na trzy sposoby: jako tlenek miedzi (Cu 2O) rozpuszczony w żużlu, [20] jako miedź siarczkowa rozpuszczona w żużlu [21] lub jako drobne kropelki (lub bryłki ) kamienia zawieszone w żużel. [22] [23]
Ilość miedzi traconej w postaci miedzi tlenkowej wzrasta wraz ze wzrostem potencjału tlenowego żużla. [23] Potencjał tlenu generalnie wzrasta wraz ze wzrostem zawartości miedzi w kamieniu. [24] Zatem utrata miedzi w postaci tlenku wzrasta wraz ze wzrostem zawartości miedzi w kamieniu. [25]
Z drugiej strony rozpuszczalność miedzi siarczkowej w żużlu zmniejsza się, gdy zawartość miedzi w kamieniu wzrasta powyżej około 40%. [21] Nagamori obliczył, że ponad połowa miedzi rozpuszczonej w żużlach z kamieni zawierających mniej niż 50% miedzi to miedź siarczkowa. Powyżej tej liczby zaczyna dominować miedź tlenkowa. [21]
Strata miedzi w postaci bryłek zawieszonych w żużlu zależy od wielkości bryłek, lepkości żużla i dostępnego czasu osiadania. [26] Rosenqvist zasugerował, że około połowa strat miedzi w żużlu była spowodowana zawieszonymi bryłkami. [26]
Masa żużla powstającego na etapie wytopu zależy od zawartości żelaza w materiale wprowadzanym do pieca do wytapiania oraz docelowego gatunku kamienia. Im większa zawartość żelaza w paszy, tym więcej żelaza będzie musiało zostać odrzucone do żużla dla danego gatunku kamienia. Podobnie zwiększenie docelowego stopnia matowienia wymaga odrzucenia większej ilości żelaza i zwiększenia objętości żużla.
Zatem dwa czynniki, które najbardziej wpływają na utratę miedzi do żużla na etapie wytapiania, to:
- gatunek matowy
- masa żużla. [18]
Oznacza to, że istnieje praktyczna granica tego, jak wysoki może być gatunek matowy, jeśli ma być zminimalizowana utrata miedzi do żużla. Dlatego wymagane są dalsze etapy przetwarzania (konwersja i rafinacja ogniowa).
W poniższych podrozdziałach pokrótce opisano niektóre procesy stosowane w wytapianiu kamienia.
Wytapianie pieca rewerberacyjnego
Piece pogłosowe są długimi piecami, które mogą przetwarzać koncentrat mokry, suchy lub prażony. [8] Większość pieców płomiennych stosowanych w ostatnich latach poddawano obróbce prażonym koncentratem, ponieważ wprowadzanie suchych materiałów wsadowych do pieca płomiennego jest bardziej efektywne energetycznie, a eliminacja części siarki w prażalni skutkuje wyższymi klasami kamienia. [8]
Wsad pieca pogłosowego jest podawany do pieca przez otwory wsadowe wzdłuż boków pieca. [8] Zwykle dodaje się dodatkową krzemionkę, aby pomóc w tworzeniu żużla. Piec opalany jest palnikami na pył węglowy, olej opałowy lub gaz ziemny [27] , a wsad stały jest topiony.
Piece pogłosowe mogą być dodatkowo zasilane roztopionym żużlem z późniejszego etapu przetwarzania w celu odzyskania zawartej miedzi i innych materiałów o wysokiej zawartości miedzi. [27]
Ponieważ kąpiel pieca pogłosowego jest nieaktywna, następuje bardzo małe utlenianie wsadu (a tym samym bardzo mało siarki jest eliminowane z koncentratu). Jest to zasadniczo proces topienia. [26] W konsekwencji, piece płomieniowe ładowane na mokro mają mniej miedzi w swoim produkcie matowym niż piece kalcynowane, a także mają mniejsze straty miedzi w żużlu. [27] Gill podaje wartość miedzi w żużlu na poziomie 0,23% dla pieca płomiennego z wsadem mokrym w porównaniu z 0,37% dla pieca kalcynowanego. [27]
W przypadku pieców kalcynowanych znaczna część siarki została wyeliminowana na etapie prażenia, a kalcynat składa się z mieszaniny tlenków i siarczków miedzi i żelaza. Piec pogłosowy działa tak, aby umożliwić tym cząsteczkom osiągnięcie równowagi chemicznej w temperaturze roboczej pieca (około 1600 °C na końcu palnika pieca i około 1200 °C na końcu kanału spalinowego; [28] kamień wynosi około 1100 °C i żużel ma około 1195°C [27] ). W tym procesie równoważenia tlen związany ze związkami miedzi wymienia się z siarką związaną ze związkami żelaza, zwiększając zawartość tlenku żelaza w piecu, a tlenki żelaza oddziałują z krzemionką i innymi materiałami tlenkowymi, tworząc żużel. [27]
Główną reakcją równoważącą jest:
- Cu 2O + FeS = Cu 2S + FeO [27]
Żużel i kamień tworzą odrębne warstwy, które można usunąć z pieca jako oddzielne strumienie. Warstwa żużla może okresowo przepływać przez otwór w ścianie pieca powyżej wysokości warstwy kamienia. Kamień jest usuwany poprzez spuszczenie go przez otwór do kadzi, aby był przenoszony dźwigiem do konwertorów. [27] Ten proces opróżniania znany jest jako spust do pieca. [27] Matowy otwór spustowy jest zwykle otworem w chłodzonym wodą bloku miedzianym, który zapobiega erozji cegieł ogniotrwałych wyściełających piec. Po całkowitym usunięciu kamienia lub żużla otwór jest zwykle zatykany gliną, którą usuwa się, gdy piec jest gotowy do ponownego gwintowania.
Do obróbki stopionego żużla konwertorowego w celu odzyskania zawartej miedzi często używano pieców pogłosowych. [27] Miało to być wlewane do pieców z kadzi dźwiganych dźwigami. Jednak żużel konwertorowy ma wysoką zawartość magnetytu [29] i część tego magnetytu wytrącałaby się z żużla konwertorowego (ze względu na wyższą temperaturę topnienia), tworząc narost na palenisku pieca rewerberacyjnego i powodując konieczność przestojów pieca w celu usunąć narost. [29] To tworzenie się narostu ogranicza ilość żużla konwertorowego, które można poddać obróbce w piecu rewerberacyjnym. [29]
Chociaż piece rewerberacyjne mają bardzo niskie straty miedzi w żużlu, nie są one bardzo wydajne energetycznie, a niskie stężenie dwutlenku siarki w ich gazach odlotowych sprawia, że jego wychwytywanie jest nieopłacalne. [8] W konsekwencji operatorzy hut przeznaczyli w latach 70. i 80. dużo pieniędzy na opracowanie nowych, bardziej wydajnych procesów wytopu miedzi. [30] Ponadto we wcześniejszych latach opracowano technologie wytapiania rzutowego, które zaczęły zastępować piece rewerberacyjne. Do 2002 roku 20 z 30 pieców pogłosowych działających jeszcze w 1994 roku zostało wyłączonych. [8]
Wytapianie pieca błyskowego
Podczas wytapiania rzutowego koncentrat dysperguje się w strumieniu powietrza lub tlenu, a reakcje wytapiania są w dużej mierze zakończone, gdy cząstki minerału są jeszcze w locie. [30] Przereagowane cząstki osadzają się następnie w kąpieli na dnie pieca, gdzie zachowują się jak kalcynacja w piecu rewerberacyjnym. [31] Na wierzchu warstwy matowej tworzy się warstwa żużla, którą można oddzielnie spuszczać z pieca. [31]
Konwersja

Miedź beztlenowa, inaczej miedź „Tough-pitch” (czystość ok. 98%), zawierająca antymon i nikiel
Kamień, który jest wytwarzany w hucie, zawiera 30–70% miedzi (w zależności od zastosowanego procesu i filozofii działania huty), głównie w postaci siarczku miedzi, a także siarczku żelaza. Siarka jest usuwana w wysokiej temperaturze jako dwutlenek siarki przez przedmuchiwanie powietrza przez stopiony kamień:
- 2 CuS + 3 O 2 → 2 CuO + 2 SO 2
- CuS + O2 2 SO22
W równoległej reakcji siarczek żelaza przekształca się w żużel:
- 2 FeS + 3 O 2 → 2 FeO + 2 SO 2
- 2 FeO + SiO 2 → Fe 2SiO 4
Czystość tego produktu wynosi 98%, jest on znany jako blister ze względu na pękniętą powierzchnię utworzoną przez ulatnianie się gazowego dwutlenku siarki, gdy chłodzone są świnki lub wlewki z miedzi konwertorowej. Produkty uboczne powstające w procesie to dwutlenek siarki i żużel. Dwutlenek siarki jest wychwytywany do wykorzystania we wcześniejszych procesach ługowania.
Rafinacja ogniowa
Miedź konwertorowa jest umieszczana w piecu anodowym, piecu, który rafinuje miedź konwertorową do miedzi anodowej w dwóch etapach, usuwając większość pozostałej siarki i żelaza, a następnie usuwając tlen wprowadzony w pierwszym etapie. Ten drugi etap, często nazywany „ polingiem ”, polega na przepuszczaniu gazu ziemnego lub innego środka redukującego przez roztopiony tlenek miedzi. Kiedy ten płomień pali się na zielono, co wskazuje na widmo utleniania miedzi, tlen w większości został spalony. Tworzy to miedź o czystości około 99%.
Elektrorafinacja

Aparatura do elektrolitycznej rafinacji miedzi
Miedź jest rafinowana metodą elektrolizy. Anody odlane z przetworzonej miedzi konwertorowej umieszcza się w wodnym roztworze 3–4% siarczanu miedzi i 10–16% kwasu siarkowego. Katody to cienkie, walcowane arkusze z bardzo czystej miedzi lub, coraz częściej, arkusze wyjściowe ze stali nierdzewnej wielokrotnego użytku (jak w procesie IsaKidd). [32] Do rozpoczęcia procesu wymagany jest potencjał tylko 0,2–0,4 V. W zakładach przemysłowych możliwe są gęstości prądu do 420 A/ 2 . [33] Na anodzie rozpuszcza się miedź i metale mniej szlachetne. Bardziej szlachetne metale, takie jak srebro, złoto, selen i tellur osadzają się na dnie ogniwa jako szlam anodowy, który stanowi produkt uboczny, który można sprzedać. Jony miedzi(II) migrują przez elektrolit do katody. Na katodzie metalowe płytki miedziane wychodzą, ale mniej szlachetne składniki, takie jak arsen i cynk, pozostają w roztworze, chyba że stosuje się wyższe napięcie. [34] Reakcje to:
Na anodzie: Cu (s) → Cu 2+ (aq) + 2e −
Na katodzie: Cu 2+ (aq) + 2e − → Cu (s)
Marketing koncentratów i miedzi
Koncentraty miedzi produkowane przez kopalnie są sprzedawane hutom i rafineriom, które przerabiają rudę i rafinują miedź oraz pobierają opłatę za tę usługę za pomocą opłat przeróbczych (TC) i opłat rafinacyjnych (RC). Światowy rynek koncentratów miedzi [35] został wyceniony na 81 mld USD w 2019 r. i przewiduje się, że do 2027 r. osiągnie 93 mld USD, rozwijając się w tempie CAGR wynoszącym 2,5%. TC są naliczane w dolarach amerykańskich za tonę przetwarzanego koncentratu, a RC są rozliczane w centach za funt, denominowane w dolarach amerykańskich, z cenami referencyjnymi ustalanymi corocznie przez główne japońskie huty. Klientem w tym przypadku może być huta, która sprzedaje wlewki miedzi blister do rafinerii lub huta-rafiner, która jest zintegrowana pionowo.
Jedna z rozpowszechnionych form koncentratu miedzi zawiera złoto i srebro, jak ta produkowana przez Bougainville Copper Limited z kopalni Panguna od wczesnych lat 70. do późnych lat 80. XX wieku.
Typowy kontrakt dla górnika jest denominowany w stosunku do ceny Londyńskiej Giełdy Metali pomniejszonej o TC-RC i wszelkie obowiązujące kary lub kredyty. Kary mogą być nałożone na koncentraty miedzi w zależności od poziomu szkodliwych pierwiastków, takich jak arsen, bizmut, ołów lub wolfram. Ponieważ duża część rudy siarczkowej miedzi zawiera srebro lub złoto w znacznych ilościach, górnikowi można zapłacić kredyt za te metale, jeśli ich stężenie w koncentracie przekroczy określoną ilość. Zwykle rafineria lub huta pobiera od górnika opłatę w oparciu o koncentrację; typowa umowa określa, że kredyt jest należny za każdą uncję metalu w koncentracie powyżej pewnego stężenia; poniżej, jeśli zostanie odzyskany, huta zatrzyma metal i sprzeda go, aby pokryć koszty.
Koncentrat miedzi jest sprzedawany na podstawie kontraktów spot lub kontraktów długoterminowych jako samodzielny produkt pośredni. Często huta sprzedaje samą miedź w imieniu górnika. Górnikowi płaci się cenę z chwili sprzedaży przez hutę-rafinerię, a nie cenę z dnia dostawy koncentratu. W ramach systemu cen ofertowych ustala się, że cena będzie ustalona w ustalonym terminie w przyszłości, zwykle 90 dni od momentu dostawy do huty.
Katoda miedziana klasy A składa się z 99,99% miedzi w arkuszach o grubości 1 cm i około 1 metra kwadratowego o wadze około 200 funtów. Jest to prawdziwy towar, który można dostarczyć na giełdy metali w Nowym Jorku (COMEX), Londynie (London Metals Exchange) i Szanghaju (Shanghai Futures Exchange). Często handel katodą miedzianą na giełdach odbywa się pośrednio za pośrednictwem warrantów, opcji lub kontraktów swap, tak że większość miedzi jest przedmiotem obrotu na LME/COMEX/SFE, ale dostawa jest realizowana bezpośrednio, logistycznie przenosząc miedź fizyczną i przenosząc blachę z same magazyny fizyczne.
Specyfikacja chemiczna miedzi elektrolitycznej to ASTM B 115-00 (norma określająca czystość i maksymalną oporność elektryczną produktu).
Mr. Nick Sun [email protected]
Czas posta: 27-wrzesień-2020