銅山とは何ですか?
銅抽出 とは、鉱石から銅を取得するために使用される方法を指します。 銅の変換は、一連の物理的および電気化学的プロセスで構成されます。 方法は進化しており、鉱石の出所、地域の環境規制、およびその他の要因に応じて国によって異なります。
すべての採掘作業と同様に、鉱石は通常、選鉱(濃縮)されなければなりません。 処理技術は鉱石の性質に依存します。 鉱石が主に硫化銅鉱物(黄銅鉱など)である場合、鉱石を粉砕して粉砕し、廃棄物(「脈石」)鉱物から貴重な鉱物を解放します。 その後、ミネラル浮選を使用して濃縮されます。 精鉱は通常、遠くの製錬所に販売されますが、一部の大規模な鉱山では近くに製錬所があります。 鉱山と製錬所のこのようなコロケーションは、19世紀から20世紀初頭にかけてより一般的であり、小規模な製錬所が経済的であった可能性があります。 硫化物精鉱は通常、OutokumpuやIncoの自溶炉、またはISASMELT炉などの炉で製錬されてマットが生成され、これを変換および精製してアノード銅を生成する必要があります。 最後に、最後の精製プロセスは電気分解です。 経済的および環境的理由から、抽出の副産物の多くは再生利用されます。 たとえば、二酸化硫黄ガスは捕捉されて硫酸に変換されます。これは、抽出プロセスで使用したり、肥料の製造などの目的で販売したりすることができます。
酸化銅鉱石は湿式製錬抽出によって処理できます。
歴史

1905年に銅国のタマラック鉱山の鉱山労働者
自然銅のコールドハンマーの最も初期の証拠は、紀元前7200年から6600年にかけてのアナトリア東部のチャユニュー遺跡での発掘調査に由来しています。[1] 奉納品またはお守りと見なされるさまざまなアイテムの中には、釣り針のように見えるものと、千枚通しのように見えるものがありました。 イラクのマーガサにあるシャニダール洞窟での別の発見には、紀元前8、700年にさかのぼる銅ビーズが含まれていました。[2]
地表堆積物の使用とは対照的に、世界で最も古い既知の銅鉱山の1つは、紀元前4千年紀からイスラエルのティムナ渓谷にあり、表面堆積物の使用量は6〜5千年紀です。[3] [4]。
The Pločnik archaeological site in southeastern Europe (Serbia) contains the oldest securely datedヨーロッパ南東部(セルビア)のプロシュニク]紀元前5、000年からの高温での銅の製造の証拠が[5]。
銅製錬技術は、銅器時代、別名銅器時代、そして青銅器時代を生み出しました。 青銅器時代は、人間が製錬技術を開発しなければ実現できなかったでしょう。
集中
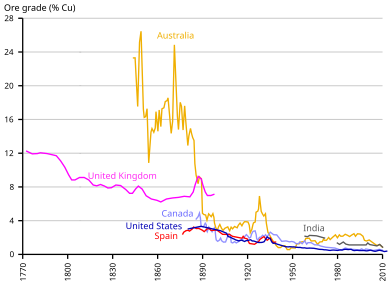
鉱石中の銅濃度の低下は、現在、鉱石の前処理を必要としています。
ほとんどの銅鉱石は、貴重な鉱石鉱物内に結合した銅金属のごく一部しか含まず、残りの鉱石は不要な岩石またはガングミネラル、通常は価値のないケイ酸塩鉱物または酸化物鉱物です。 場合によっては、銅を回収する技術が向上したため、失われた価値を回収するために尾鉱が後退しました。 21世紀の銅鉱石の平均グレードは0.6%未満の銅であり、経済的な鉱石鉱物(銅を含む)の割合は鉱石の総量の2%未満です。 鉱石の冶金学的処理の主な目的は、岩石内の脈石鉱物から鉱石鉱物を分離することです。
冶金処理回路内のプロセスの最初の段階は、正確な粉砕または 粉砕であり、岩石を粉砕して、個々の鉱物相からなる小さな粒子(<100μm)を生成します。 次に、これらの粒子を分離して脈石(岩石の残留物)を除去し、その後、岩石から鉱石鉱物を物理的に遊離させるプロセスが続きます。 銅鉱石の遊離のプロセスは、それらが酸化物鉱石であるか硫化鉱石であるかによって異なります。[6]
その後のステップは、銅を含む鉱石の性質と何が抽出されるかによって異なります。 酸化物鉱石の場合、通常、湿式製錬の解放プロセスが実施されます。これは、鉱石鉱物の可溶性の性質を利用して、冶金処理プラントの利点を生かします。 二次(超遺伝子)と一次(低遺伝子)の両方の硫化鉱の場合、泡浮選を使用して、鉱石を脈石から物理的に分離します。 特殊な自然銅を含む鉱体または超遺伝子の自然銅が豊富な鉱体のセクションの場合、この鉱物は単純な重力回路で回収できます。
泡浮選

オンタリオ州ファルコンブリッジの硫化銅および硫化ニッケル鉱物を濃縮するためのフロス浮選セル。
現代の泡浮選プロセスは、オーストラリアで1900年代初頭に、CV Potterによって、そしてほぼ同時にGDDelpratによって独自に発明されました。[7]

南オーストラリア州のプロミネントヒルマインの浮選プラントにあるジェイムソンセルに硫化銅を充填した気泡
硫化銅のすべての一次硫化鉱、および二次硫化銅のほとんどの精鉱(輝銅鉱)は、製錬にかけられます。 輝銅鉱濃縮物を可溶化し、得られた浸出液から銅カソードを生成するために、いくつかのバット浸出または圧力浸出プロセスが存在しますが、これは市場のごく一部です。
炭酸塩精鉱は、通常、ヒープリーチ操作の最終段階として、銅セメンテーションプラントから生産される比較的マイナーな製品です。 このような炭酸塩濃縮物は、溶媒抽出および電解採取(SX-EW)プラントで処理するか、製錬することができます。
銅鉱石は、硫化銅鉱石鉱物と脈石鉱物の間で許容できる程度の遊離が発生するようなサイズに粉砕および粉砕されます。 次に、鉱石を湿らせ、スラリーに懸濁し、キサントゲン酸塩または他の試薬と混合します。これにより、硫化物粒子が疎水性になります。 典型的な試薬には、エチルキサントゲン酸カリウムとエチルキサントゲン酸ナトリウムが含まれますが、ジチオホスフェートとジチオカルバメートも使用されます。
処理された鉱石は、メチルイソブチルカルビノール(MIBC)などの界面活性剤を含む水で満たされた曝気槽に導入されます。 空気は常にスラリーに押し込まれ、気泡は疎水性の硫化銅粒子に付着します。硫化銅粒子は表面に導かれ、そこで泡を形成してすくい取られます。 これらのスキミングは通常、クリーナースカベンジャーセルにかけられ、過剰なケイ酸塩を除去し、濃縮物の品質に悪影響を与える可能性のある他の硫化鉱物(通常は方鉛鉱)を除去し、最終的な濃縮物を製錬に送ります。 浮選セルに浮き上がっていない岩石は、尾鉱として廃棄されるか、鉛(方鉛鉱から)や亜鉛(閃亜鉛鉱から)などの他の金属が存在する場合は、それらを抽出するためにさらに処理されます。 プロセス効率を改善するために、石灰を使用して水浴のpHを上げ、コレクターをよりイオン化し、黄銅鉱(CuFeS 2、黄鉄鉱(FeS 2)を回避します。 鉄は両方の一次ゾーンの鉱物に存在します。 黄銅鉱を含む銅鉱石を濃縮して、20%から30%の濃縮銅(通常は27から29%の銅)を含む精鉱を製造することができます。 濃縮物の残りは、黄銅鉱中の鉄と硫黄、およびケイ酸塩脈石鉱物や他の硫化鉱物、通常は少量の黄鉄鉱、閃亜鉛鉱、方鉛鉱などの不要な不純物です。 輝銅鉱は鉱物内に鉄を含まないため、輝銅鉱の精鉱は通常、37%から40%の濃縮銅に分類されます。
湿式製錬抽出
硫化鉱
二次硫化物(超遺伝子の二次濃縮によって形成されるもの耐火性)。これらの鉱石は、炭酸銅、硫酸塩、リン酸塩、酸化物の鉱物と二次硫化鉱物の混合物であり、主に輝銅鉱ですが、方輝銅鉱などの他の鉱物が一部の鉱床で重要になる場合があります。
硫化物に富む超遺伝子鉱石は、泡浮選を使用して濃縮することができます。 輝銅鉱の典型的な濃縮物は、硫化物中の銅を37%から40%の間で等級分けすることができ、黄銅鉱濃縮物と比較して、それらを比較的安価に精錬することができます。
一部の超遺伝子硫化物堆積物は、細菌酸化ヒープ浸出プロセスを使用して浸出させ、硫化物を硫酸に酸化することができます。これにより、硫酸と同時に浸出して硫酸銅溶液を生成することもできます。 酸化物鉱石と同様に、溶媒抽出および電解採取技術を使用して、妊娠中の浸出液から銅を回収します。
自然銅鉱物が豊富な超遺伝子硫化鉱は、実行可能なすべての時間スケールで硫酸浸出による処理に耐性があり、高密度の金属粒子はフロス浮選媒体と反応しません。 通常、自然銅がスーパージーンプロファイルのマイナーな部分である場合、それは回復されず、テーリングに報告されます。 十分に豊富な場合、自然銅鉱体は、金属の密度を使用して軽いケイ酸塩鉱物から銅を解放する重力分離回路を介して、含まれている銅を回収するように処理できます。 多くの場合、脈石の性質は重要です。粘土が豊富な自然銅鉱石は解放が難しいことがわかっているからです。
酸化物鉱石
酸化銅鉱体は、アズライトやマラカイトなどの炭酸銅鉱物、および珪孔雀石などのケイ酸塩やアタカマ石などの硫酸塩などの他の可溶性鉱物が優勢な酸化鉱石を処理するために使用される水文冶金プロセスで、いくつかのプロセスを介して処理できます。
このような酸化物鉱石は、通常、硫酸によって浸出され、通常、ヒープ浸出またはダンプ浸出プロセスで、溶液中に硫酸銅を含む硫酸の溶液に銅鉱物を遊離させる。 次に、硫酸銅溶液(妊娠中の浸出液)は、溶媒抽出および電解採取(SX-EW)プラントを介して銅が除去され、禁止された(露出した)硫酸がヒープに再循環されます。 あるいは、銅を鉄くずと接触させることにより、妊娠中の溶液から銅を沈殿させることができます。 セメンテーションと呼ばれるプロセス。 セメント銅は通常、SX-EW銅よりも純度が低くなります。 酸化銅の浸出液として一般的に硫酸が使用されますが、特に超可溶性硫酸塩鉱物が豊富な鉱石には水を使用することもできます。ヨーロッパ南東部(セルビア)の要出典]
一般に、酸化物鉱物はフロス浮選化学物質またはプロセスに反応しないため(すなわち、それらは灯油ベースの化学物質に結合しないため)、フロス浮選は銅酸化物鉱石の濃縮には使用されません。 酸化物銅鉱石は、酸化物鉱物粒子と反応して硫化物の薄いライム(通常はカルコサイト)を生成する特定の化学物質で酸化物鉱物を硫化することによるフロス浮選によって処理されることがあり、これはフロス浮選プラントによって活性化されます。
硫化物製錬
20世紀の後半まで、硫化鉱の製錬は、採掘された鉱石から銅金属を生産する(一次 銅生産)ほとんど唯一の手段でした。 Davenportらは、2002年に、それでも世界の一次銅生産の80%が銅-鉄-硫黄鉱物からのものであり、これらの大部分が製錬によって処理されたことを指摘しました。
銅は、最初に硫化鉱を炉で直接製錬することによって硫化鉱から回収されました。[9] 製錬所は当初、輸送コストを最小限に抑えるために鉱山の近くに配置されていました。 これにより、銅含有ミネラルに含まれる廃ミネラルと硫黄および鉄の輸送にかかる法外なコストを回避できました。 しかし、鉱体中の銅の濃度が低下するにつれて、鉱石全体を製錬するためのエネルギーコストも法外に高くなり、最初に鉱石を濃縮する必要がありました。
初期濃縮技術には、手作業による選別[10] と重力濃縮が含まれていました。 それらは銅の高い損失をもたらしました。 その結果、泡浮選プロセスの開発は、鉱物処理における大きな前進でした。[11] ユタ州の巨大なビンガムキャニオン鉱山の開発を可能にしました。[12]
20世紀には、ほとんどの鉱石は製錬前に濃縮されていました。 製錬は当初、焼結プラントと高炉を使用して[13] 、またはロースターと反射炉を使用して行われました。[14] 1960年代まで、焙焼および反射炉製錬が一次銅生産を支配していた。[8]
焙煎
焙焼工程は一般的に反射炉と組み合わせて行われます。 ロースターでは、銅精鉱が部分的に酸化されて「煆焼」と二酸化硫黄ガスが生成されます。 発生する反応の化学量論は次のとおりです。
- 2 CuFeS 2 + 3 O2 2 2FeO + 2 CuS + 2 SO 2
Roasting generally leaves more sulfur in the calcined product (15% in the case of the roaster at Mount Isa Mines15] )。 ) than a sinter plant leaves in the sintered product (about 7% in the case of the Electrolytic Refining and Smelting smelter[16]).
As of 2005, roasting is no longer common in copper concentrate treatment, because its combination with reverberatory furnaces is not energy efficient and the SO2 濃度が希薄すぎて費用効果の高い回収ができ[8] 現在、直接製錬が好まれています。たとえば、自溶製錬、イサスメルト、ノランダ、三菱、エルテニエンテの各製錬技術を使用しています。[8]
製錬

この技術を使用する銅製錬所の数に関連して、反射炉製錬を自溶製錬に置き換える。
製錬される材料の最初の溶融は、通常、 製錬 または マット製錬 段階と呼ばれます。 これは、ほとんど廃止されたブラスト炉や残響炉、フラッシュ炉、イサスメルト炉など、さまざまな炉で実施できます。[8] この製錬段階の製品は、銅、鉄、硫黄の混合物です。銅が豊富で、マット または 銅マット.[8] という用語 マットグレード is normally used to refer to the copper content of the matte.[17]
マット製錬段階の目的は、銅の損失を最小限に抑えながら、不要な鉄、硫黄、 脈石 の鉱物(シリカ、マグネシア、アルミナ、石灰石など)を可能な限り排除することです。[17] これは、硫化鉄を酸素(空気中または酸素富化空気中)と反応させて酸化鉄(主にFeOとして、ただし一部のマグネタイト(Fe 3O 4)と)および二酸化硫黄を生成することによって達成されます。[17]
硫化銅と酸化鉄は混合する可能性がありますが、十分なシリカを添加すると、別のスラグ層が形成されます。[18] シリカを添加すると、スラグの融点(より正確には液相線温度)も低下します。これは、製錬プロセスをより低い温度で操作できることを意味します。[18]
スラグ形成反応は次のとおりです。
- FeO + SiO2 2 [ 2[17]
スラグはマットよりも密度が低いため、マットの上に浮かぶ層を形成します。[19]
銅は3つの方法でマットから失われる可能性があります:スラグに溶解した亜酸化銅(Cu 2O)、[20]スラグに 溶解した硫化銅[21] 、または 小さな液滴(または プリル)としてスラグ。[22] [23]
スラグの酸素ポテンシャルが増加するにつれて酸化物銅が増加するにつれて失われる銅の量。[23] マットの銅含有量が増加すると、一般に酸素ポテンシャルが増加します。[24] したがって、マットの銅含有量が増加すると、酸化物としての銅の損失が増加します。[25]
一方、マットの銅含有量が約40%を超えると、スラグへの硫化銅の溶解度は低下します。[21] 、または 長森は、50%未満の銅を含むマットからのスラグに溶解した銅の半分以上が硫化銅であると計算しました。 この図の上では、酸化銅が優勢になり始めています。[21] 、または
スラグに懸濁されたプリルとしての銅の損失は、プリルのサイズ、スラグの粘度、および利用可能な沈降時間に依存します。[26] ローゼンクヴィストは、スラグによる銅損の約半分は、吊り下げられたプリルによるものであると示唆した。[26]
製錬段階で発生するスラグの質量は、製錬炉に供給される材料の鉄含有量と目標のマットグレードによって異なります。 飼料の鉄含有量が多いほど、特定のマットグレードのスラグに拒否される必要のある鉄が多くなります。 同様に、目標マットグレードを上げるには、より多くの鉄を排除し、スラグの量を増やす必要があります。
したがって、製錬段階での銅のスラグへの損失に最も影響を与える2つの要因は次のとおりです。
- マットグレード
- スラグの質量。[18]
これは、スラグへの銅の損失を最小限に抑える場合、マットグレードの高さに実際的な制限があることを意味します。 したがって、処理のさらなる段階(変換および火の精製)が必要です。
次のサブセクションでは、マット製錬で使用されるプロセスのいくつかについて簡単に説明します。
反射炉製錬
反射炉は、湿った、乾いた、または焙煎した濃縮物を処理できる長い炉です。[8] 後年に使用された反射炉のほとんどは、乾燥供給材料を反射炉に入れる方がエネルギー効率が高く、ロースター内の硫黄の一部を除去するとより高いマットグレードになるため、焙煎濃縮物を処理しました。[8]
反射炉フィードは、炉の側面に沿ったフィードホールを介して炉に追加されます。[8] 通常、スラグの形成を助けるために追加のシリカが追加されます。 微粉炭、燃料油または天然ガスを使用してバーナーで炉を燃焼させ[27] 、固体装入物を溶解します。
反射炉には、後の変換段階から溶融スラグを追加で供給して、含まれている銅および銅含有量の高い他の材料を回収することができます。[27]
反射炉浴は静止しているため、原料の酸化はほとんど発生しません(したがって、濃縮物から硫黄がほとんど除去されません)。 それは本質的に溶融プロセスです。[26] その結果、湿式反射炉は、煆焼炉よりもマット製品中の銅が少なく、スラグに対する銅損も少ない。[27] Gillは、スラグ中の銅の値を、湿式反射炉では0.23%、煆焼炉では0.37%と見積もっています。[27]
煆焼炉の場合、焙焼段階で硫黄のかなりの部分が除去されており、煆焼は銅と鉄の酸化物と硫化物の混合物で構成されています。 反射炉は、これらの種が炉の動作温度(炉のバーナー端で約1600°C、煙道端で約1200°C)で化学平衡に近づくことを可能にするように機能します。[28] マットは約1100°Cであり、スラグは約1195°Cです[27] )。 この平衡化プロセスでは、銅化合物に関連する酸素が鉄化合物に関連する硫黄と交換し、炉の酸化鉄含有量が増加し、酸化鉄がシリカや他の酸化物材料と相互作用してスラグを形成します。[27]
主な平衡反応は次のとおりです。
- Cu 2O + FeS = Cu 2S + FeO [27]
スラグとマットは別個の層を形成し、別々の流れとして炉から取り除くことができます。 スラグ層は、マット層の高さより上の炉の壁の穴を通って定期的に流れることができます。 マットは、クレーンでコンバーターに運ばれるように、穴から取鍋に排出することによって除去されます。[27] この排水プロセスは タッピングとして知られています。 the furnace.[27] The matte taphole is normally a hole through a water-cooled copper block that prevents erosion of the refractory bricks lining the furnace. When the removal of the matte or slag is complete, the hole is normally plugged with clay, which is removed when the furnace is ready to be tapped again.
反射炉は、溶融した転炉スラグを処理して含まれている銅を回収するためによく使用されていました。[27] これはクレーンで運ばれる取鍋から炉に注がれるでしょう。 しかし、転炉スラグはマグネタイトを多く含み[29] 、このマグネタイトの一部は転炉スラグから沈殿し(融点が高いため)、反射炉の炉床に付着物を形成し、付着物を取り除きます。[29] この降着形成は、反射炉で処理できるコンバータスラグの量を制限します。[29]
反射炉はスラグに対する銅損が非常に少ないですが、エネルギー効率があまり高くなく、オフガス中の二酸化硫黄の濃度が低いため、捕獲が不経済になります。[8] その結果、製錬所のオペレーターは1970年代と1980年代に、新しい、より効率的な銅製錬プロセスの開発に多額の資金を費やしました。[30] さらに、自溶製錬技術は初期に開発され、反射炉に取って代わり始めた。 2002年までに、1994年にまだ稼働している30基の反射炉のうち20基が停止されていた。[8]
自溶炉製錬
自溶製錬では、精鉱は空気または酸素の流れに分散され、鉱物粒子がまだ飛行している間に製錬反応がほぼ完了します。[30] 次に、反応した粒子は炉の底にある浴に沈殿し、反射炉での煆焼と同じように振る舞います。[31] マット層の上にスラグ層が形成され、炉から個別にタップすることができます。[31]
変換

アンチモンとニッケルを含む無酸素銅、別名「タフピッチ」銅(純度約98%)
製錬所で生産されるマットには、主に硫化銅と硫化鉄として、30〜70%の銅が含まれています(使用するプロセスと製錬所の操作哲学によって異なります)。 硫黄は、溶融マットに空気を吹き込むことにより、二酸化硫黄として高温で除去されます。
- 2 CuS + 3 O2 2 → 2 CuO + 2 SO2
- CuS + O2 2 Cu + SO 2
並行反応では、硫化鉄がスラグに変換されます。
- 2 FeS + 3 O2 2 → 2 FeO + 2 SO2
- 2 FeO + SiO2 →Fe2 2SiO4
この製品の純度は98%で、 ブリスターブリスターとして知られています。 because of the broken surface created by the escape of sulfur dioxide gas as blister copper pigs or ingots are cooled. By-products generated in the process are sulfur dioxide and slag. The sulfur dioxide is captured for use in earlier leaching processes.
火の精製
ブリスター銅はアノード炉に入れられます。アノード炉は、残りの硫黄と鉄の大部分を除去し、最初の段階で導入された酸素を除去することによって、ブリスター銅をアノードグレードの銅に精製する炉です。ポーリング 天然ガスまたはその他の還元剤を溶融酸化銅に吹き込むことによって行われます。 この炎が緑色に燃え、銅の酸化スペクトルを示しているとき、酸素はほとんど燃え尽きています。 これにより、約99%の純度で銅が作成されます。
電解精製

銅の電解精製装置
銅は電気分解によって精製されます。 処理されたブリスター銅から鋳造されたアノードは、3〜4%の硫酸銅と10〜16%の硫酸の水溶液に入れられます。 陰極は、高純度の銅の薄い圧延シート、または最近ではより一般的には、再利用可能なステンレス鋼の開始シートです(IsaKiddプロセスのように)。[32] プロセスを開始するには、わずか0.2〜0.4ボルトの電位が必要です。 産業プラントでは、最大420 A / m2の電流密度2 可能です。[33] アノードでは、銅と低貴金属が溶解します。 銀、金、セレン、テルルなどのより多くの貴金属がアノードスライムとしてセルの底に沈殿し、販売可能な副産物を形成します。 銅(II)イオンは、電解質を通ってカソードに移動します。 陰極では、銅の金属板が外に出ますが、より高い電圧を使用しない限り、ヒ素や亜鉛などの高貴でない成分が溶液中に残ります。[34] 反応は次のとおりです。
アノードで:Cu (s) →Cu 2+ (aq) + 2e −
カソードで:Cu 2+ (aq) + 2e − →Cu (s)
コンセントレートと銅のマーケティング
鉱山で生産された銅精鉱は、鉱石を処理して銅を精製し、処理料金(TC)と精製料金(RC)を介してこのサービスの料金を請求する製錬所と精製業者に販売されます。 世界の銅精鉱市場 [35]は、2019年に810億米ドルと評価され、2027年までに930億米ドルに達し、CAGR 2.5%で拡大すると予測されています。 TCは処理された精鉱1トンあたりUS $で請求され、RCは処理されたポンドあたりセントで請求され、米ドル建てで、ベンチマーク価格は日本の主要な製錬所によって毎年設定されます。 この場合の顧客は、ブリスター銅インゴットをリファイナーに販売する製錬所、または垂直統合された製錬所リファイナーである可能性があります。
銅精鉱の一般的な形態の1つには、1970年代初頭から1980年代後半にかけて、ブーゲンビルカッパーリミテッドがパングナ鉱山から生産したものと同様に、金と銀が含まれています。
鉱山労働者の一般的な契約は、ロンドン金属取引所の価格からTC-RCおよび該当するペナルティまたはクレジットを差し引いたものです。 ペナルティは、ヒ素、ビスマス、鉛、タングステンなどの有害元素のレベルに応じて、銅精鉱に対して評価される場合があります。 硫化銅鉱体の大部分にはかなりの量の銀または金が含まれているため、精鉱内のそれら の濃度 が特定の量を超える場合、これらの金属の鉱夫にクレジットを支払うことができます。 通常、精製業者または製錬所は、濃度に基づいて鉱夫に料金を請求します。 通常の契約では、特定の濃度を超える濃縮物中の金属のオンスごとにクレジットが支払われることを指定します。 その下で、それが回収された場合、製錬所は金属を保持し、費用を負担するためにそれを販売します。
銅精鉱は、それ自体が中間製品として、スポット契約または長期契約のいずれかで取引されます。 多くの場合、製錬所は鉱山労働者に代わって銅金属自体を販売します。 鉱夫には、精鉱の配達日の価格ではなく、製錬所の精製業者が販売した時点の価格が支払われます。 見積価格設定システムでは、価格は将来の決まった日付、通常は製錬所への配達時から90日であることが合意されています。
Aグレードの銅カソードは、厚さ1 cm、重さ約200ポンドの約1メートル四方のシートに99.99%の銅が含まれています。 これは真の商品であり、ニューヨーク市(COMEX)、ロンドン(ロンドン金属取引所)、上海(上海先物取引所)の金属取引所に配達され、取引可能です。 多くの場合、銅カソードは、ワラント、オプション、またはスワップ契約を介して間接的に取引所で取引され、銅の大部分はLME / COMEX / SFEで取引されますが、配送は直接行われ、物理的な銅をロジスティックに移動し、銅シートを物理的な倉庫自体。
電解グレードの銅の化学仕様は、ASTM B 115-00(製品の純度と最大電気抵抗率を指定する規格)です。
Mr. Nick Sun [email protected]
投稿時間:2020年9月27日